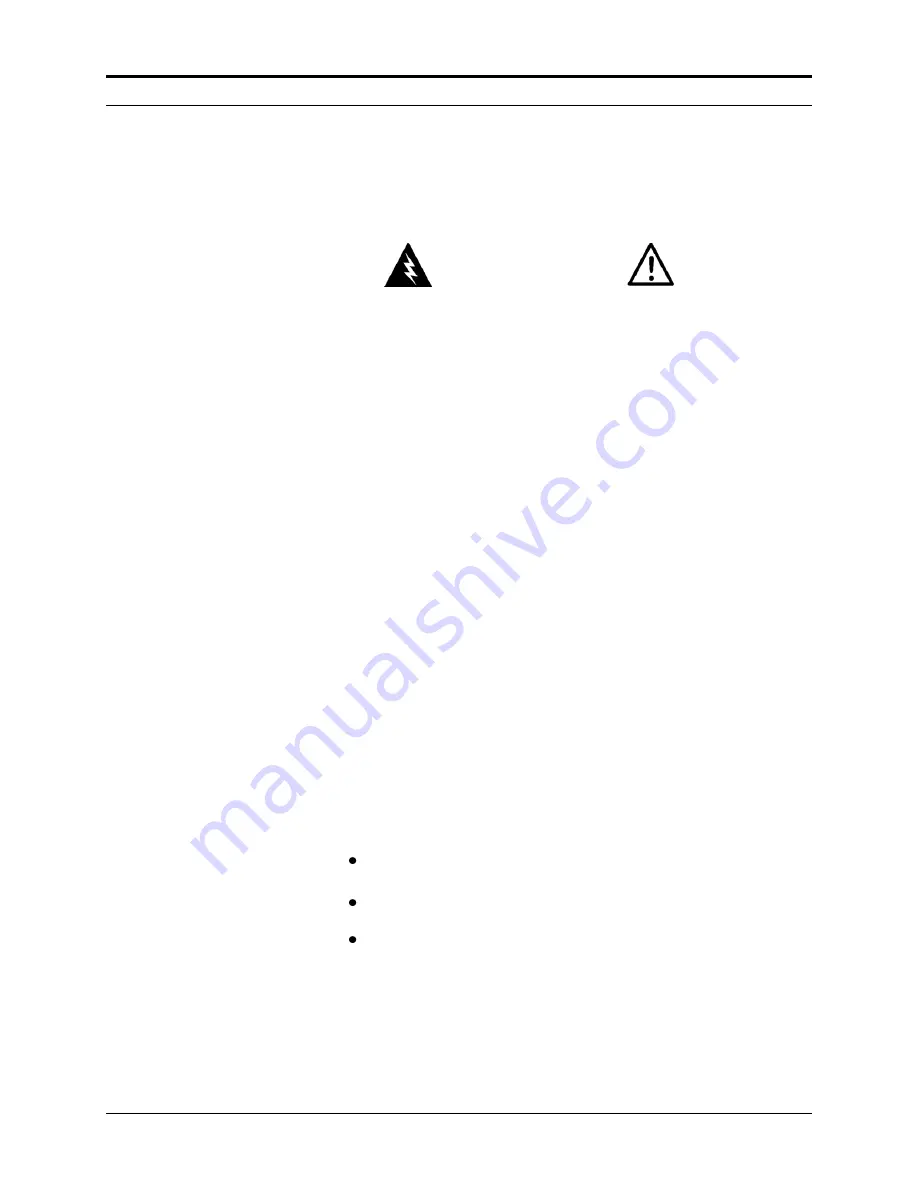
Series 810 Instruction Manual
Chapter 1 Introduction
Safety Information
Caution and warning statements are used throughout this book to
draw your attention to important information.
Warning!
Caution!
This statement appears with information that
This statement appears with information that is
is important to protect people and equipment
important for protecting your equipment and
from damage. Pay very close attention to all
performance. Read and follow all cautions that
warnings that apply to your application.
apply to your application.
Receipt of System Components
When receiving a Sierra transducer, carefully check the outside
packing carton for damage incurred in shipment. If the carton is
damaged, notify the local carrier and submit a report to the factory or
distributor. Remove the packing slip and check that all ordered
components are present and match your specifications (as ordered).
Make sure any spare parts or accessories are not discarded with the
packing material. Do not return any equipment to the factory without
first contacting Sierra Customer Service.
Technical Assistance
If you encounter a problem with your transducer, review the
configuration information for each step of the installation, operation
and set up procedures as explained in this manual. Verify that your
settings and adjustments are consistent with factory
recommendations. Refer to Chapter 5, Troubleshooting, for specific
information and recommendations.
If the problem persists after following the troubleshooting procedures
outlined in Chapter 5, contact Sierra Instruments by fax or by E-mail
(see inside front cover). For urgent phone support you may call (800)
866-0200 or (831) 373-0200 between 8:00 a.m. and 5:00 p.m. PST.
In Europe contact Sierra Instruments BV at +31 72 5071400. When
contacting Technical Support, make sure to include this information:
The flow range, serial number, Sierra order number and
model number (all marked on the transducer nameplate)
The problem you are encountering and any corrective action
taken
Application information (gas, pressure, temperature, pipe
and fitting configuration)
IM-81
1-3