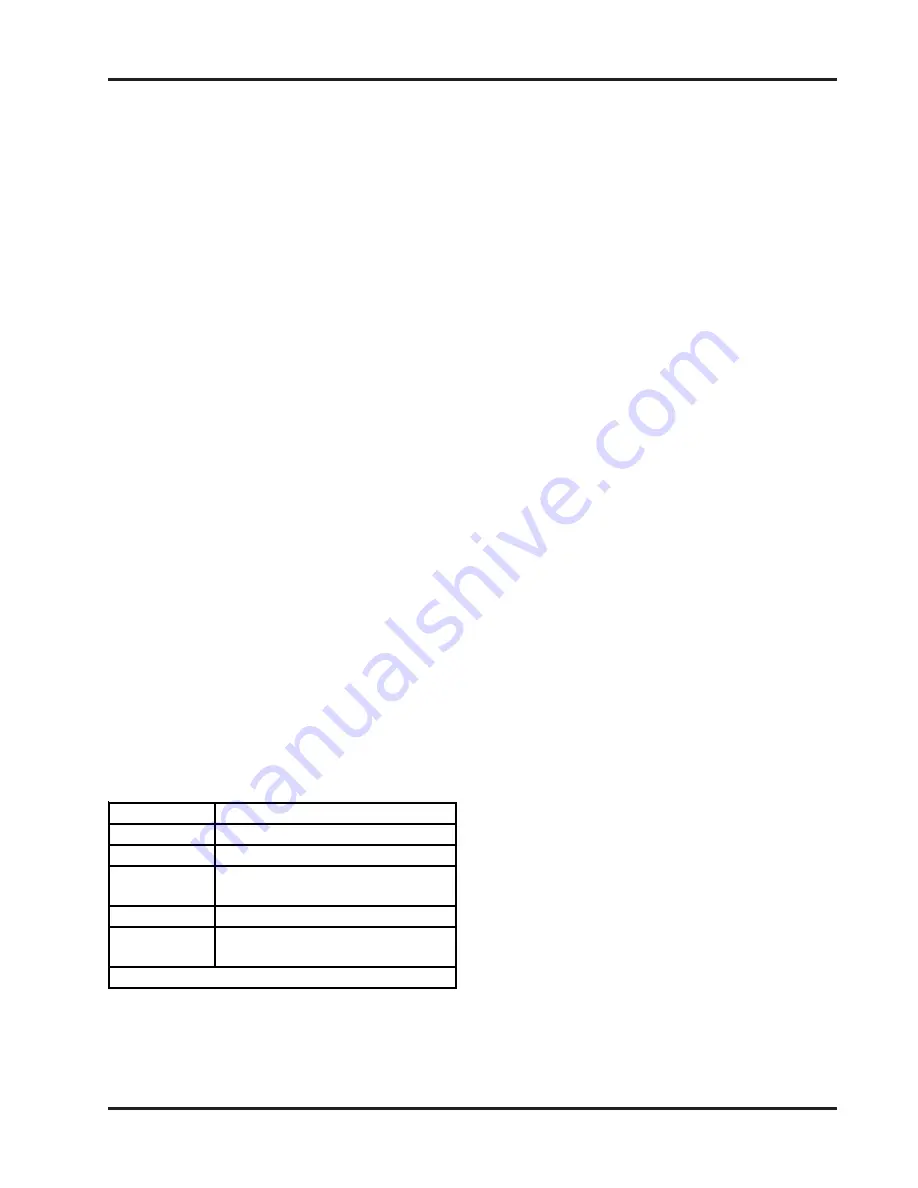
2050/2060 Gas Monitors (5/04)
Page:
Instruction Manual
8
6.0 INSTALLATION
6.1 Gas Sensor Module Locations
The gas sensor module is a diffusion type sensor
that should be located close to the anticipated source
or destination of the gas hazard. For heavy gases
such as H
2
S install the module within 24 inches of
the ground. For lighter gases such as CO and com-
bustible gases use a higher elevation.
After optimum locations are determined based on
the above recommendations, consideration should
be given to placing the sensors in locations that are
accessible for calibration service. Slight adjustments
to the location of the sensor may have little impact
on effectivity but major effect on accessibility.
6.2 Mounting
To mount the monitor, remove the four svrews in the
cover plate and move the cover plate aside. Use
screws through the monitoring holes visible in the
four corners of the housing to mount the monitor to
a wall.
- The installation must meed any hazardous envi-
ronmental codes for AC/DC electrical instrumenta-
tion.
6.3 Wiring
Interconnect wiring from the controller to the module
is by 4 conductor 22 AWG (or lower AWG) cable,
conduit as necessary. Shielding is not required.
For installations where the distance from the con-
troller to the sensor is greater than 500 feet, 18
AWG cable is recommended.
The terminal strip on the electronics board in the
module. The wiring must be connected as indi-
cated in Figure 6.1 depending upon the controller
or relay configuration being used.
6.4 Power Supply
The power supplied by the controlling device or an
external power supply must meet the following speci-
fications:
Voltage:9 - 24 VDC
Current: 250 mA
6.5 Alarm Devices
The internal relay is rated at 0.5 Amp, normally open
dry contact rated at 100 VDC/130 VAC.
Terminal Function
TB1-1
+ VDC (9 – 24)
TB1-2 GND
(0VDC)
TB2-1
Relay NC (Normally Closed) or
Output to Model 2102 Safe
TB2-2 Relay
Common
TB2-3
Relay NO (Normally Open) or
Output to Model 2102 Alarm
Table 6.1