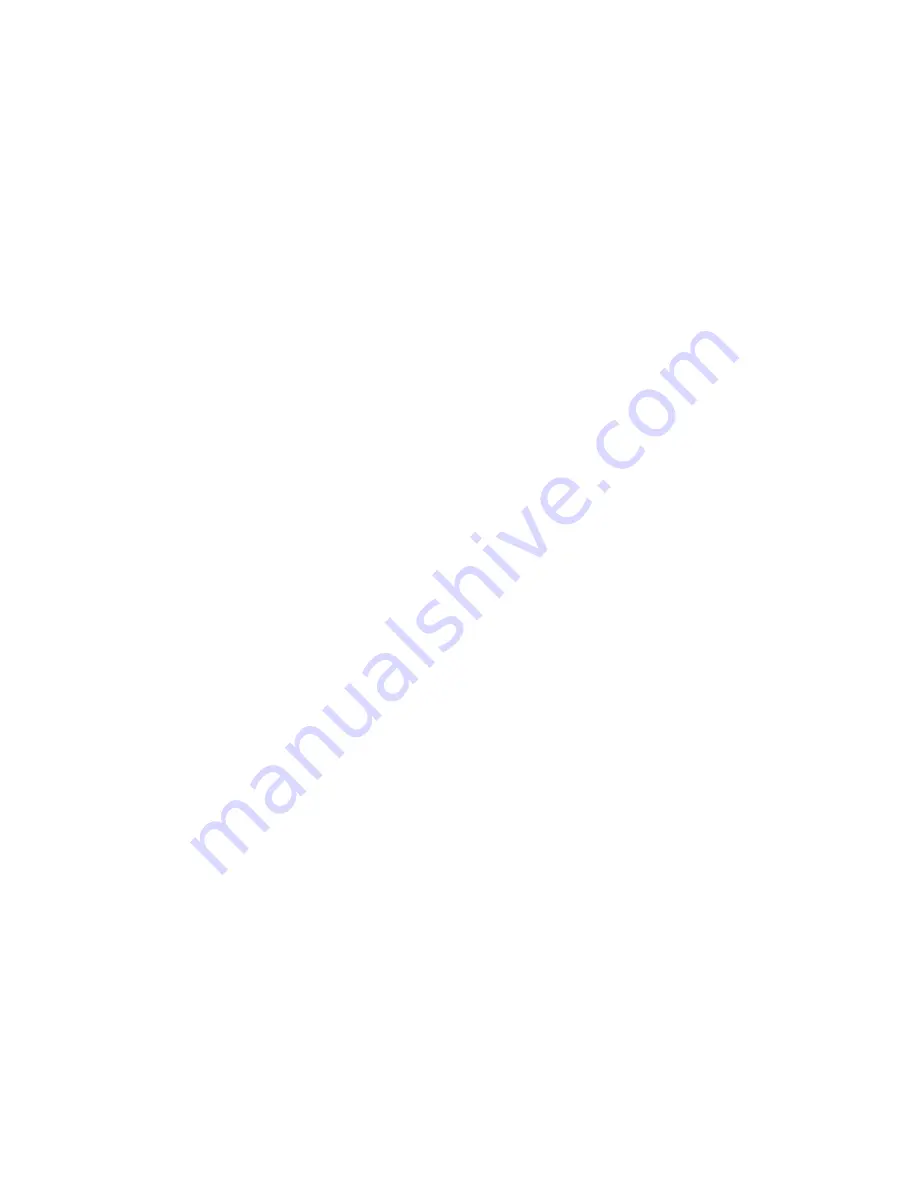
Siemens Industry, Inc. 5300 Triangle Parkway, Norcross, GA 30092
A5E33045207A
E87010-A0401-T002-A5-MCC
tiastar
TM
Motor Control Center
Page 7 of 12
5. Outgoing Power and Control Wiring
5.1. Connect power and control wires for the unit with
the unit stabs disengaged from the vertical bus.
5.2. Wiring between control units is pulled through the verti-
cal wireway at the right side of the section. These wires
can be fastened with the wireform wireties provided.
Route wiring to control units in other sections through
the horizontal wireways.
5.3. When load cable conduit is in the bottom of a Motor
Control Center, additional room for pulling cable may
be obtained by removing bottom plug-in units.
6. Pre-operation Checks
Before energizing and operating the motor control center,
perform the following checks
6.1. Operate all magnetic devices by hand to be sure that
all parts operate freely. Check all interlocks for proper
contact operation
6.2. Current transformers for customer remote devices are
hipped with their secondaries shorted out. Be sure all
such shunts are removed when the metering circuits are
completed.
6.3. Be sure that each motor is connected with the proper
starter
6.4. Check the overload setting or overload heater element
against the full load current shown on the nameplate of
each motor.
6.5. Check all heater elements to insure that they are
6.7. If instantaneous trip circuit breakers are used,
adjust as follows:
6.7.1. Determine motor full load current from the motor
nameplate data. Use screwdriver to set indicator
on adjustment screw to the appropriate position.
6.7.2. For maximum protection, the trip position should
be set as low as possible. Turn the adjustment
screw counterclockwise to successively lower
positions until the breaker trips on motor starting.
After this position is determined, turn the adjust-
ment screw clockwise to the next higher setting
for normal operation.
If the breaker does not trip at the lowest setting,
leave the indicator at this setting.
6.7.3. If tripping occurs at highest setting; re-check
motor nameplate information, then check voltage
and load with peak reading ammeter to locate
problem.
6.8. If fusible disconnect type starters are used, check for
proper fuse size. Fuse size should not exceed 150%
FLA for RK5 and 300% FLA for Type J.
6.9. Clean the motor control center and be sure that all
extraneous material has been removed.
6.10. Check the torque value of each connection.
Factory connections may loosen during shipment
storage. It is of utmost importance to inspect
all connections and bolted joints for tightness
PRIOR TO energizing the equipment. Follow torque
requirements of individual components for
motor / load connections.
6.11. Close all access plates and doors before the motor
control center is energized.
6.12. Jog motors to determine proper rotation.
5.4. For rear units of back-to-back Motor Control Centers,
connect motor T1 to terminal unit T3 and motor T3 to
terminal unit T1 in order to obtain the same motor rota-
tion as for motors controlled by front units.
properly installed.
6.6. Check all timers for proper time interval setting and
contact operations.