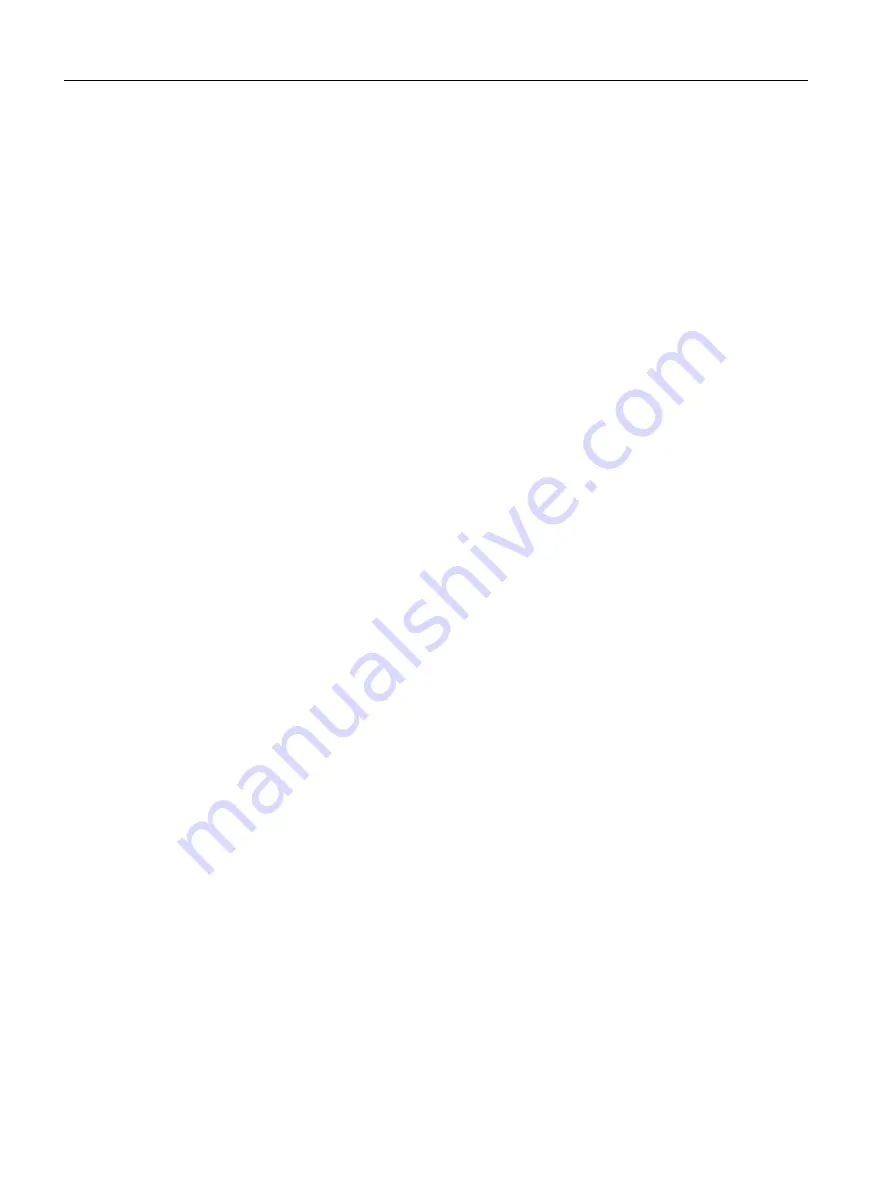
S1: Spindles
16.2 Operating modes
Basic Functions
1272
Function Manual, 09/2011, 6FC5397-0BP40-2BA0
Phase 1
Case 1: Spindle not synchronized
With the programming of
SPOS
,
M19
or
SPOSA
the spindle accelerates with the acceleration from the machine
data:
MD35200 $MA_GEAR_STEP_SPEEDCTRL_ACCEL (Acceleration in the speed control mode)
This direction of rotation is defined by the machine data:
MD35350 $MA_SPIND_POSITIONING_DIR (Direction of rotation while positioning to standstill)
Exception:
If
ACN
,
ACP
,
IC
is used for positioning, the programmed direction of travel is activated.
The spindle is synchronized at the next zero mark of the spindle position actual-value encoder and switches to
the position control mode.
Whether the zero mark is found in the traversed path (except for IC), is monitored:
MD34060 $MA_REFP_MAX_MARKER_DIST (maximum distance to the reference mark)
If the speed defined in machine data:
MD35300 $MA_SPIND_POSCTRL_VELO (Positioning speed)
is reached before the spindle is synchronized, the spindle will continue to rotate at the positioning activation
speed (it is not accelerated further).
Case 2: Spindle synchronized
SPOS
,
M19
or
SPOSA
will switch the spindle to position control mode.
The acceleration from the following machine data is active:
MD35210 $MA_GEAR_STEP_POSCTRL_ACCEL (acceleration in position control mode)
The direction of rotation is defined by the programmed motion (
ACP
,
ACN
,
IC
,
DC
) or via the pending distance-to-
go.
The speed entered in
MD35300 $MA_SPIND_POSCTRL_VELO (position control activation speed)
is not exceeded in the machine data.
The travel path to the end position is calculated.
The spindle travels to the programmed end point optimally in terms of time. This means that the end point is
approached at the highest possible speed (maximum MD35300 $MA_SPIND_POSCTRL_VELO). Depending on
the appropriate secondary conditions, the phases 1 - 2 - 3 - 4 or 1- 3a - 4a are executed.