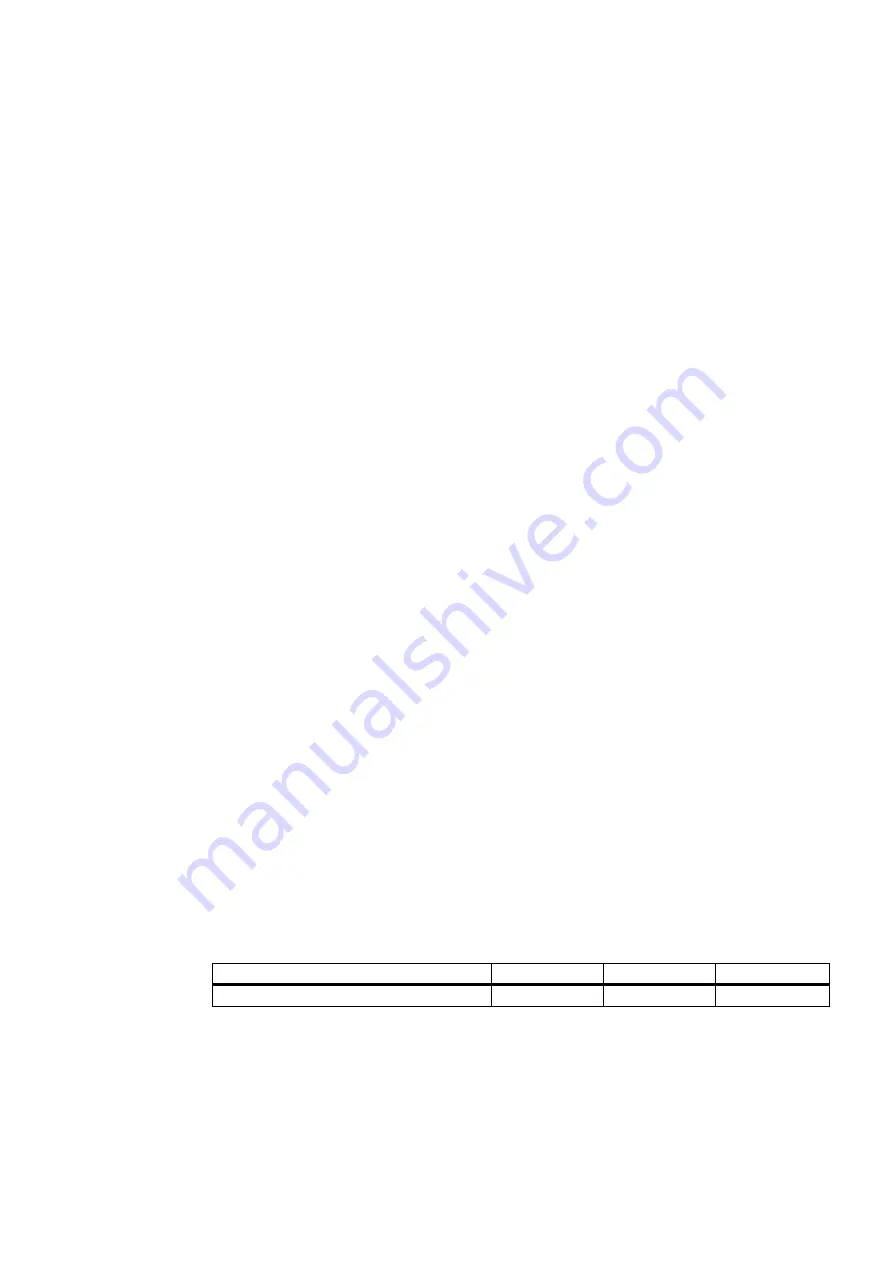
1PM6/1PM4 Hollow-Shaft Motors for Main Spindle Drives
Configuration Manual, PPMS, 04/2008, 6SN1197-0AD23-0BP0
35
Mechanical properties of the motors
3
3.1
Cooling
Hollow-shaft motors must be continually cooled independent of the duty type (S1, S6):
●
Liquid cooling with water or oil (1PM4)
●
Forced ventilation (1PM6)
3.1.1
Liquid cooling
For liquid-cooled motors, the cooling conditions (coolant intake temperature, liquid volume,
coolant pressure) must be maintained.
The coolants must be pre-cleaned or filtered in order to prevent the cooling circuit from
becoming blocked. After filtering, the max. permissible particle size may be 100 μm.
The checking and change intervals for the coolant should be agreed with the anti-corrosion
agent supplier and the cooling system manufacturer.
If the direction of the coolant flow is not specified by arrows, then the intake and outlet
openings can be freely selected.
Coolant intake temperature, required cooling power
In order to prevent moisture condensation, the coolant intake temperature must be higher
than the ambient temperature. Recommendation: T
cool
≥ T
ambient
-2°C
The motors are designed in accordance with EN 60034-1 for operation up to 30 °C coolant
temperature, maintaining all of the motor ratings.
If the motors are operated at higher coolant intake temperatures, the derating factors in the
following table must be taken into account:
Table 3-1
Derating factor for rated current and rated torque
Coolant intake temperature
≤ 30 °C
≤ 40 °C
≤ 50 °C
Derating factor
1,0
0,9
0,85