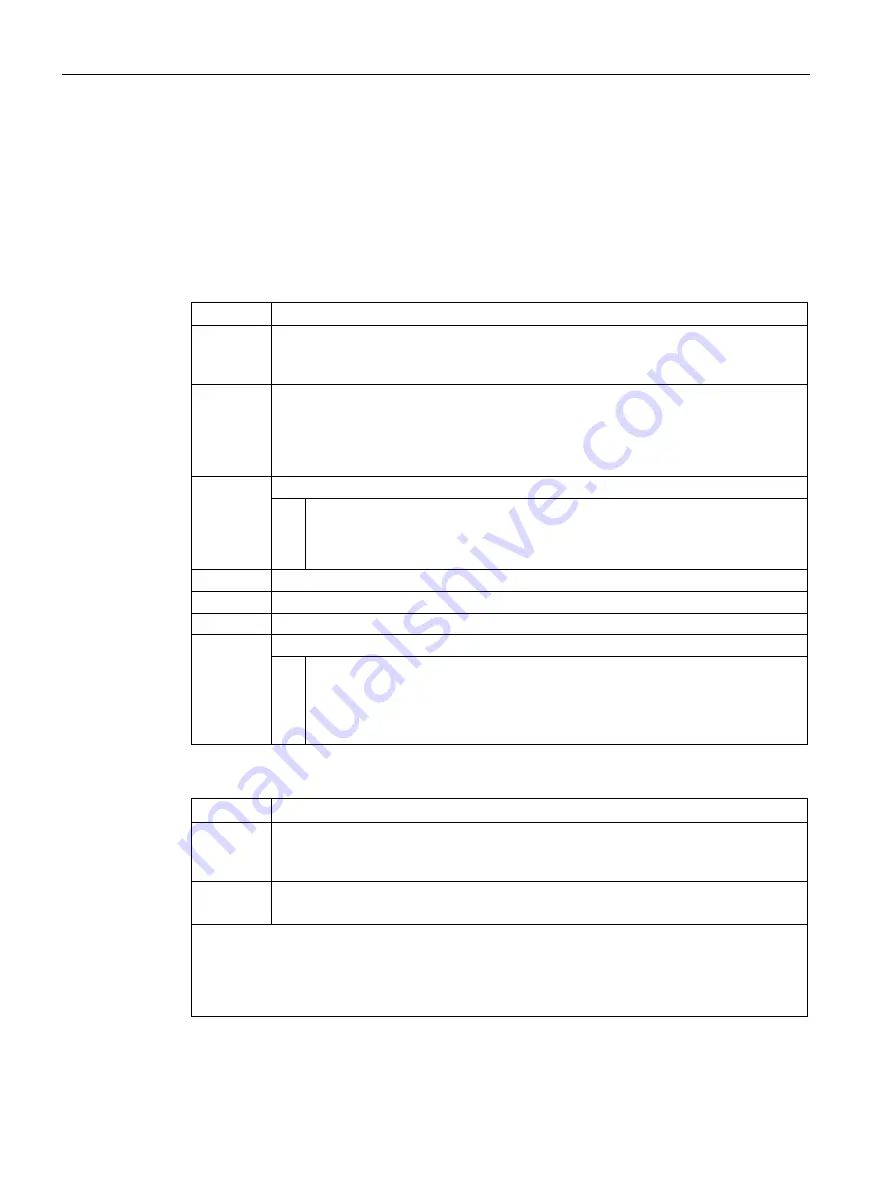
Advanced commissioning
7.8 Application-specific functions
Converter with control units CU250D-2
242
Operating Instructions, 04/2015, FW V4.7.3, A5E34261542B AB
DC braking when the motor is switched off
1.
The higher-level control switches off the motor (OFF1 or OFF3).
2.
The motor brakes along the down ramp to the speed for the start of DC braking.
3.
DC braking starts.
Settings for DC braking
Parameter Description
p0347
Motor de-excitation time (calculated after the basic commissioning)
The inverter can trip due to an overcurrent during DC braking if the de-excitation time is
too short.
p1230
DC braking activation (factory setting: 0)
Signal source to activate DC braking
•
0 signal: Deactivated
•
1 signal: Active
p1231
Configuring DC braking (factory setting: 0)
0
4
5
14
No DC braking
General release for DC braking
DC braking for OFF1/OFF3
DC braking below the starting speed
p1232
DC braking braking current (factory setting 0 A)
p1233
DC braking duration (factory setting 1 s)
p1234
DC braking start speed (factory setting 210000 rpm)
r1239
DC braking status word
.08
.10
.11
.12
.13
DC braking active
DC braking ready
DC braking selected
DC braking selection internally locked
DC braking for OFF1/OFF3
Table 7- 27 Configuring DC braking as a response to faults
Parameter Description
p2100
Set fault number for fault response (factory setting 0)
Enter the fault number for which DC braking should be activated, e.g. p2100[3] = 7860
(external fault 1).
p2101 = 6 Fault response setting (factory setting 0)
Assigning the fault response: p2101[3] = 6.
The fault is assigned an index of p2100. Assign the same index of p2100 or p2101 to the fault and
fault response.
The inverter's List Manual lists in the "Faults and alarms" list the possible fault responses for every
fault. The "DCBRAKE" entry means that it is permissible to set DC braking as response for this par-
ticular fault.