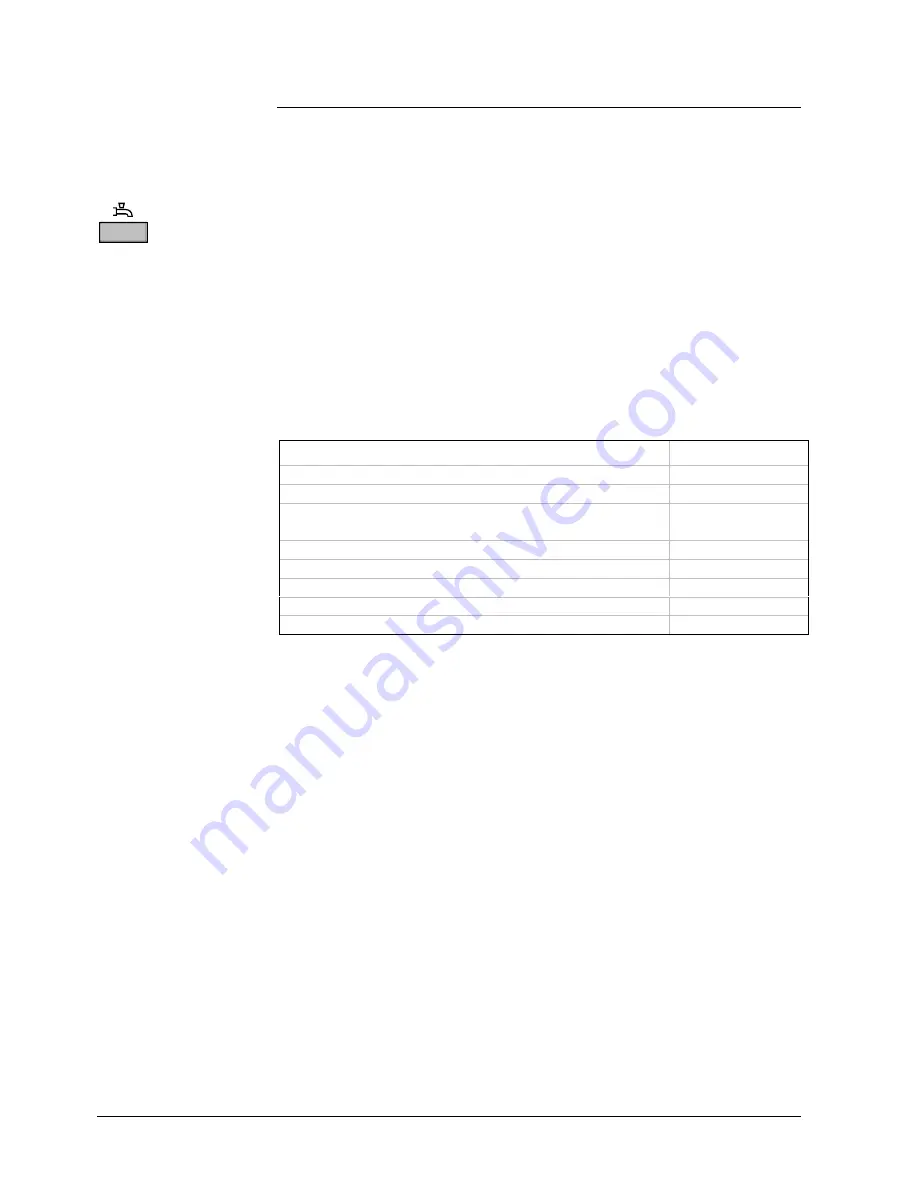
38/184
Siemens Building Technologies
Basic Dokumentation RVA63.280, RVA53.280
CE1P2374E
Landis & Staefa Division
19.04.2001
1.2
Operating mode of d.h.w. heating
Selection of d.h.w. heating mode independent of heating operation.
Selection is made directly on the user interface
D.h.w. heating is selected by pressing the respective button on the controller's user
interface.
By pressing the respective button, d.h.w. heating is switched on or off.
•
D.h.w. heating OFF - button dark.
D.h.w. is not being heated. Frost protection remains active, however, and prevents
the storage tank temperature from falling below a certain level
•
D.h.w. heating ON - button illuminated.
The d.h.w. is heated according to the settings made
The following settings affect d.h.w. heating and must be checked to ensure proper
functioning:
Setting
Setting
•
Time switch program 3
19-25
•
Nominal setpoint of the d.h.w. temperature
26
•
Summer / winter changeover HC1 and HC2 (when using an
electric immersion heater)
29
•
Assignment of d.h.w. heating
123
•
Reduced setpoint of d.h.w. temperature
120
•
D.h.w. heating program
121
•
D.h.w. charging
124
•
Type of d.h.w. demand
125
Benefit
Setting
Effect
Required settings