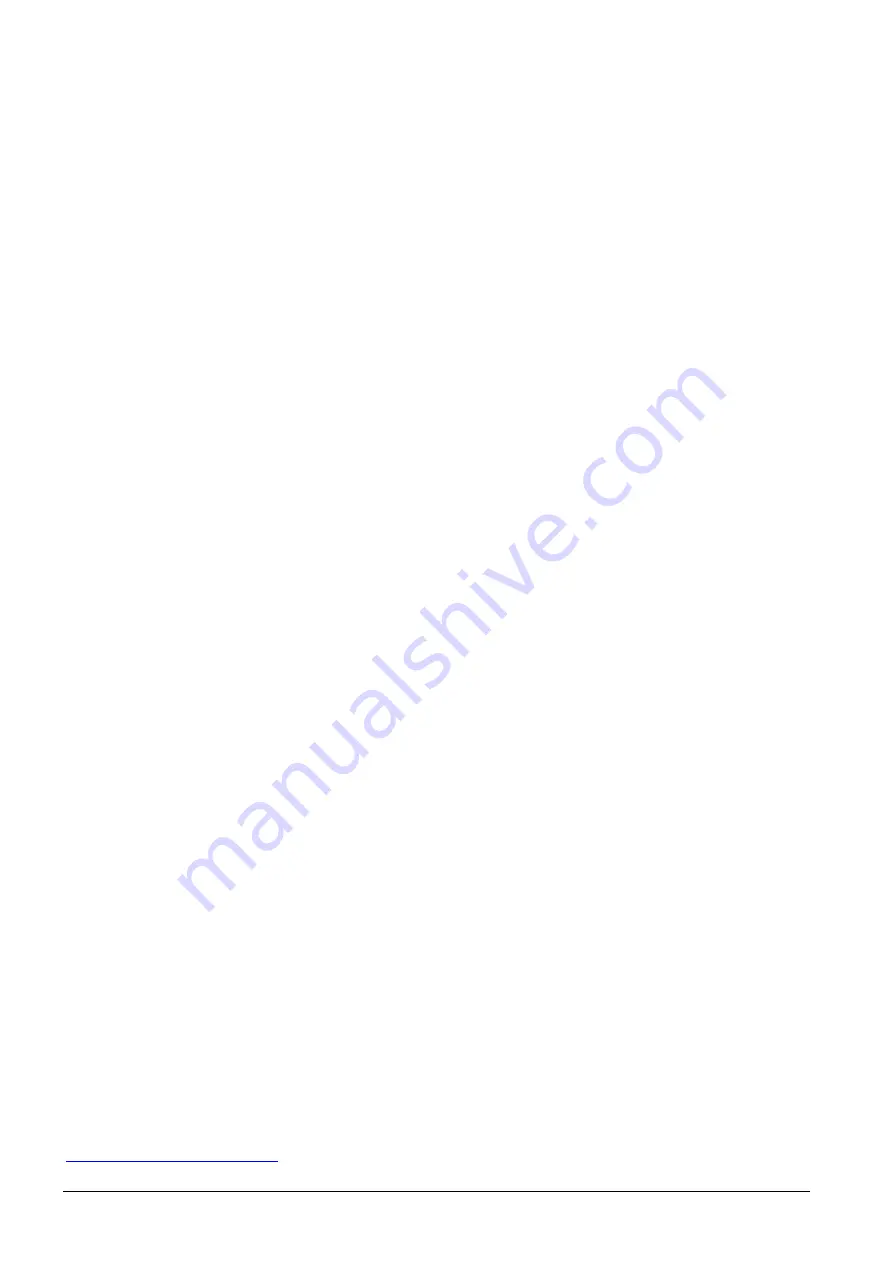
42 / 42
Siemens
VAV compact controller G..B181.1E/3 | VAV modular controller ASV181.1E/3
CE1P3544en
Building Technologies
2016-02-26
Issued by
Siemens Switzerland Ltd
Building Technologies Division
International Headquarters
Gubelstrasse 22
6301 Zug
Switzerland
Tel. +41 41-724 24 24
www.siemens.com/buildingtechnologies
© Siemens Switzerland Ltd, 2011
Technical specifications and availability subject to change without notice.