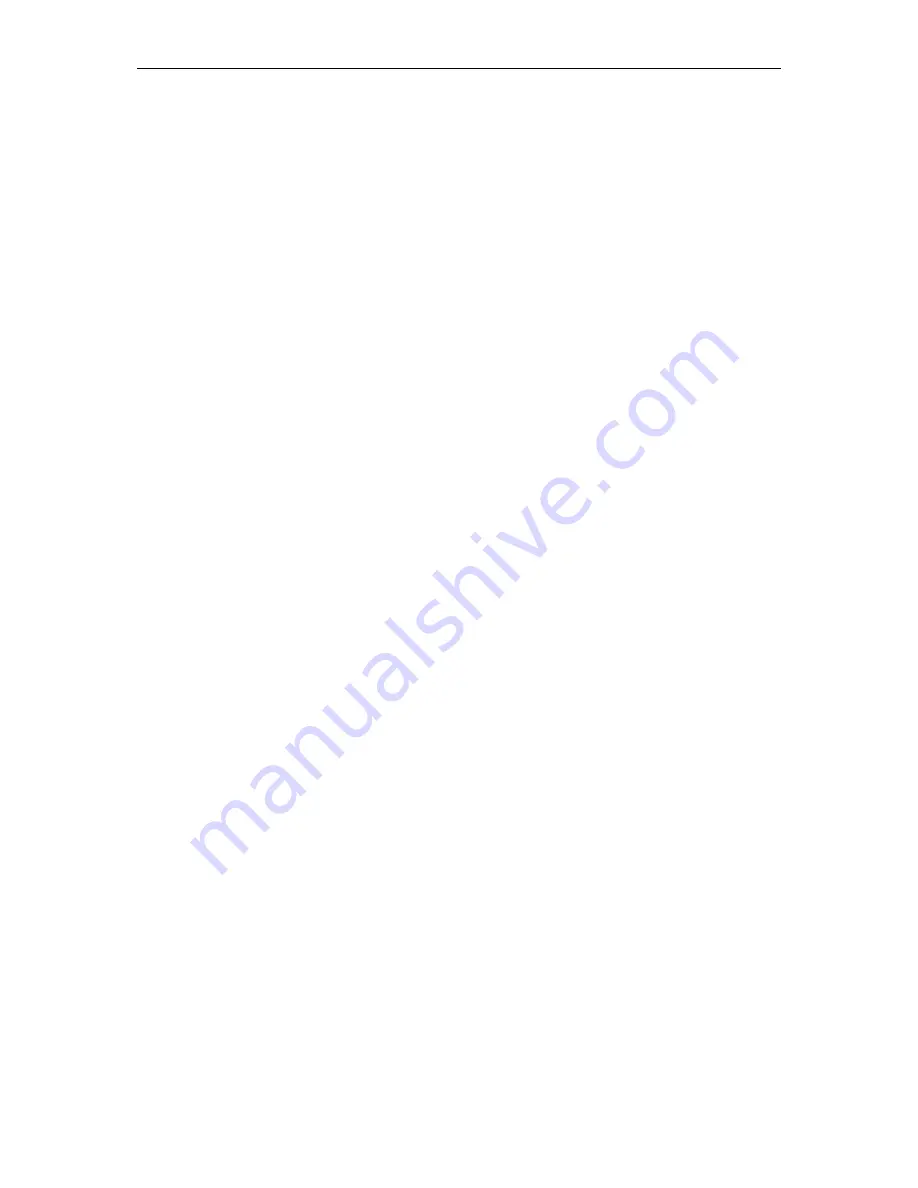
Network Topologies
3.1 Linear (bus) Topology
SIMATIC NET PROFIBUS, Optical Link Module
Operating Instructions, 07/2008, A2B00065774O, Edition V1.5
9
3.1.1
Linear (bus) topology with fiber-optic link monitoring and segmentation
Use this mode especially when you want a disrupted fiber-optic cable segment to
be separated from the rest of the network (see section 4.2.2.4). Only use this
mode, if you only connect PROFIBUS OLM V4.0 or V3/V4.0 with each other.
Monitoring mechanisms:
•
Send echo:
yes
•
Monitor echo:
yes
•
Suppress echo:
yes
•
Monitor:
yes
•
Segmentation:
yes
In this mode, the individual fiber-optic links are monitored by the two connected
modules.
If a module fails or a fiber-optic cable breaks or disturbances are detected on the
optical transmission line, the fiber-optic link between the two OLMs is interrupted
(segmented). The PROFIBUS network is separated into two (sub)networks each
remaining functional on its own. The problem is indicated by the channel LEDs
changing to red and by the signaling contacts of the two OLMs connected to the
disturbed fiber-optic link. The segmentation is canceled automatically as soon as
both modules recognize that the segmented fieldbus (sub)network is no longer
disrupted based on test frames that they send out automatically. Note that if a
problem occurs in networks with several active bus nodes, two logical token rings
are formed. As a result, temporary network disturbances may occur due to double
tokens or frame collisions when the full network is restored.
Note:
If modules with two optical channels are used at the end of a line, the unused
optical channel must be set to the mode
“
bus without fiber-optic link monitoring
”
,
so that it does not cause a broken fiber-optic cable signal (see section 4.2.3.4).
Remember that the optical channels that are not connected must be protected
against external light and pollution by protective caps.
3.1.2
Bus topology without fiber-optic link monitoring
Use this mode when you connect a PROFIBUS OLM with a different fiber-optic
component according to the PROFIBUS guideline (optical/electrical converter),
which does not send a frame echo and does not expect or tolerate a frame echo.
Monitoring mechanisms:
•
Send echo:
no
•
Monitor echo:
no
•
Suppress echo:
no
•
Monitor:
no
•
Segmentation:
no
In this mode, there is no monitoring of the individual fiber-optic links.