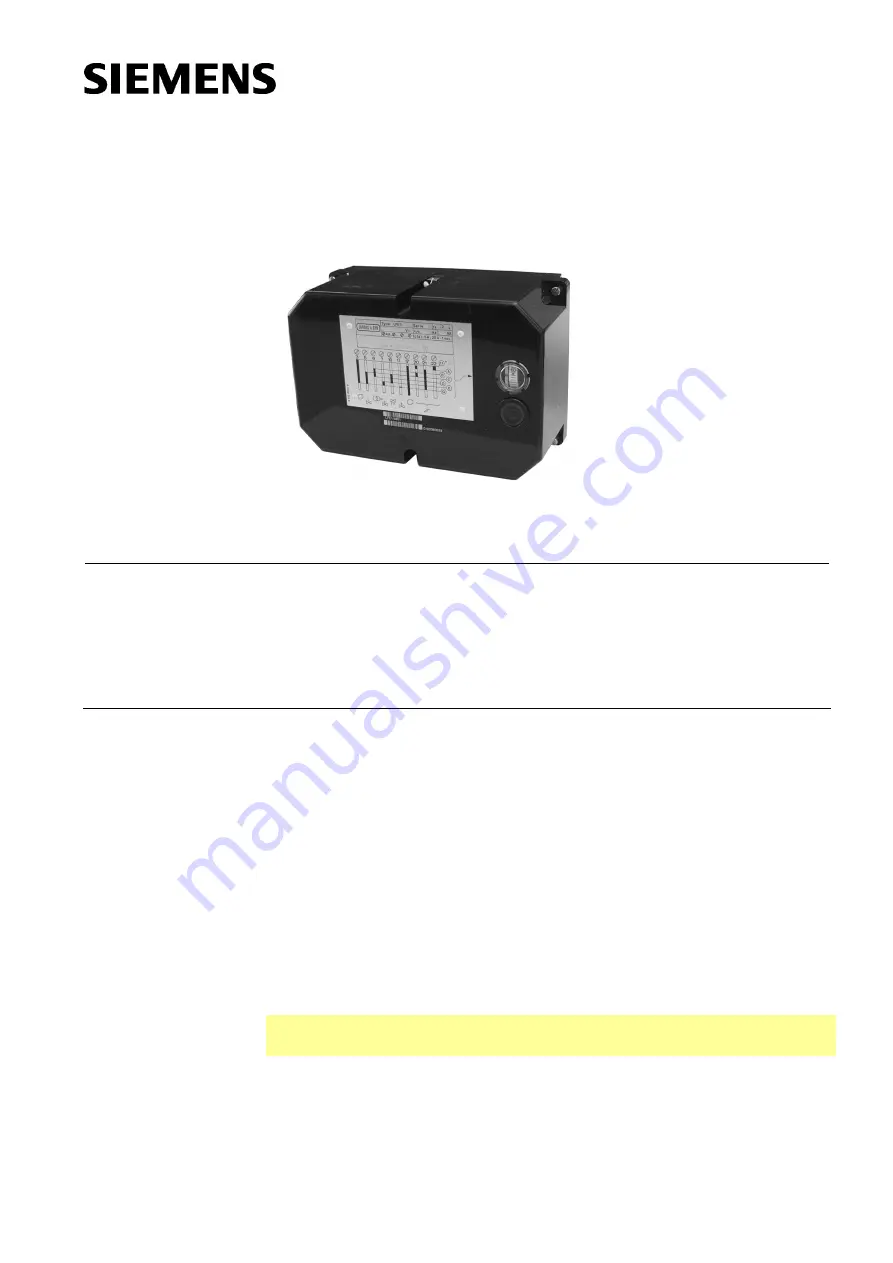
CC1N7461en
21.08.2018
Building Technologies
7
461
Burner Controls
LFE1...
The LFE1... burner control is designed for use with forced draft gas and dual-fuel
burners of any capacity, in intermittent operation.
The LFE1... and this Data Sheet are intended for use by OEMs which integrate the
burner controls in their products.
Use
The LFE1... is designed for the fully automatic control and supervision of single-stage,
multi-stage or modulating gas or dual-fuel burners. It is suited for use with expanding
flame and interrupted pilot type gas burners. Flame supervision is ensured by means of
an ionization probe or a QRA... UV flame detector. Ignition spark proving with a UV
flame detector is also possible. When used in connection with a gas valve proving
system LDU11... (refer to Data Sheet N7696), the control sequence of the LFE1… can
be extended to include automatic gas valve proving. All types of burner controls comply
with the relevant European standards for gas and oil burners of any capacity.
The LFE1... can control the following burner plant components:
fan motor, flue gas fan, air damper, ignition transformer, 1 to 3 fuel valves, load
controller and an external lockout warning device.
·
Applications in accordance with EN 676: Automatic forced draft burners for liquid
fuels
·
Type-tested in accordance with EN 298: 2004
C
Note!
Do not use for new designs.