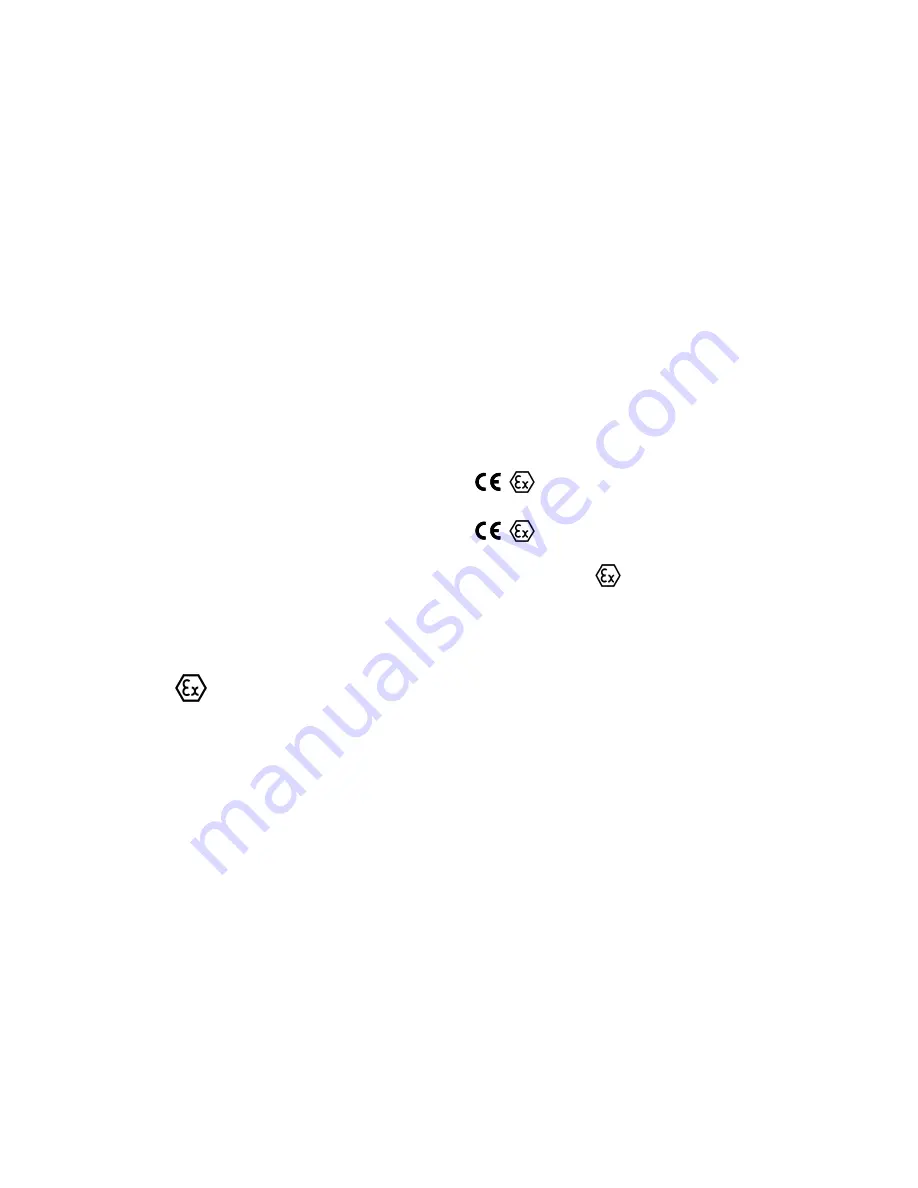
10 / 23
BA 3102 en 02/2016
The coupling must not be operated unless housed in a suitable enclosure in accordance with the standards
applying. This also applies to test runs and when checking the direction of rotation.
All work on the coupling must be carried out only when it is at a standstill. Secure the drive unit to prevent
unintentional switchon. A notice should be attached to the ON switch stating clearly that work is in
progress.
In addition to any generally prescribed personal safety equipment (such as safety shoes, safety clothing,
helmet)
suitable safety gloves
and
suitable safety glasses
must be worn when handling the coupling
or clutch!
Only spare parts made by the manufacturer Siemens must be used.
Any enquiries should be addressed to:
Siemens AG
Schlavenhorst 100
46395 Bocholt
Tel.:
+49 (0)2871 / 92-0
Fax:
+49 (0)2871 / 92-2596
2.2
Marking of the coupling parts for use in potentially explosive zones
Couplings which are ordered in Atex configuration, have the following marking on the outer circumference
of coupling part 10:
Siemens AG
II 2G T4 / T5 / T6 D120 °C
46393 Bocholt - Germany
(- 50 °C) - 30 °C ≤ T
a
≤ + 80 °C / + 50 °C / + 40 °C
FLENDER couplings N-EUPEX <year built>
I M2
Coupling part 2, couzpling part 4 or coupling part 9 bears the marking
.
The marking is in one or two lines.
If, in addition to the CE mark, the letter
"U"
together with the Siemens order number has been stamped
on, the coupling part has been delivered by Siemens un or prebored.
Siemens supplies unbored and prebored couplings with CE marking only under the
condition that the customer assumes the responsibility and liability for correct
refinishing in a declaration of exemption.
When using electrically insulating flexible elements, the marking of the explosion
group IIA, IIB is added.