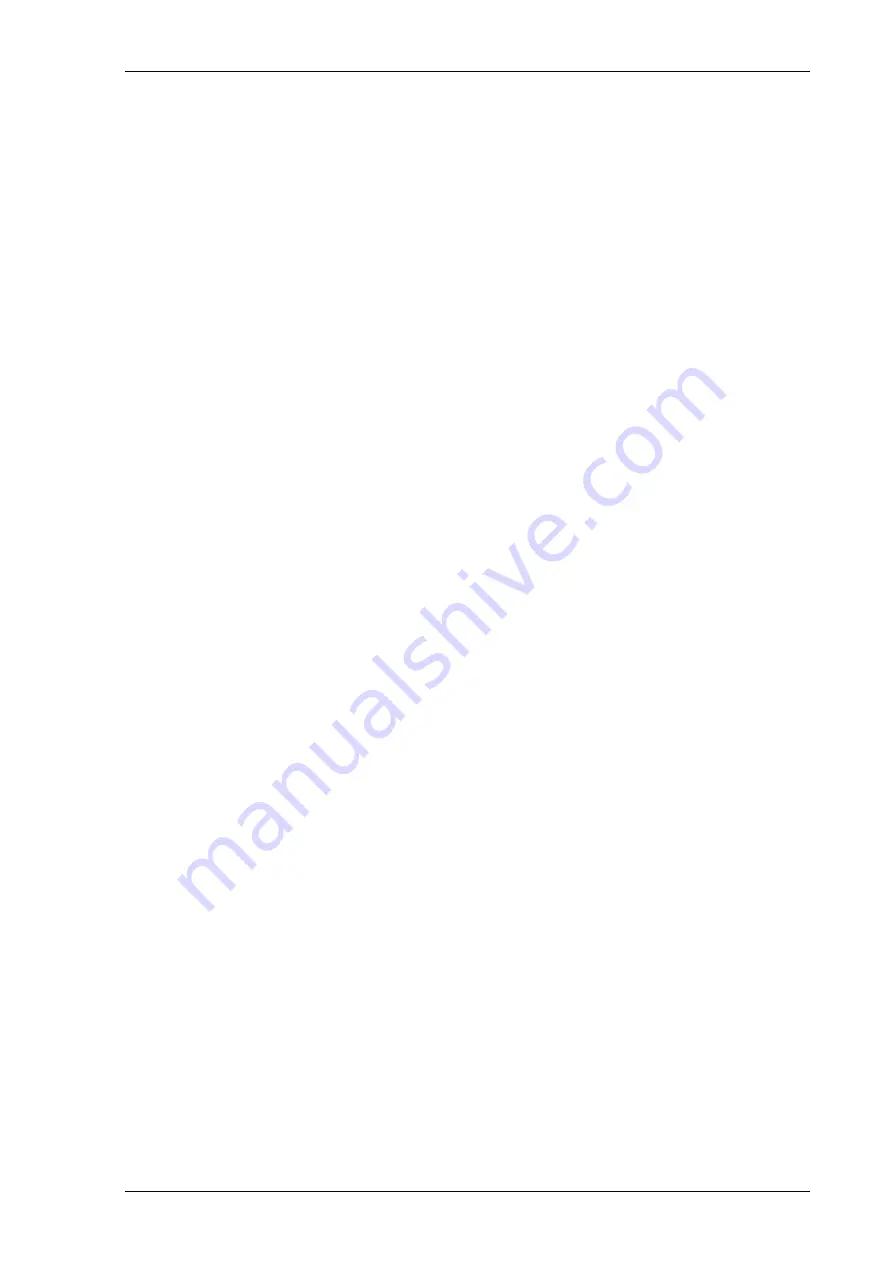
MSCDN – MP2A Description of Operation
1) Two Wide Bandwidth Analogue Input modules (4 x I per module)
2) One Controller CPU module
3) One Power Supply and Basic I/O module
4) One Output relay/Status Input Module
5) One Front Fascia
2.2 Analogue Inputs
Two analogue modules are used in the case style E16. Each module consists of up to 4 channels of
current.
In order to ensure high accuracy true RMS measurements over a wide bandwidth and accurate phase and
slip frequency calculations, the current signals are sampled at 32 samples per cycle.
2.3 Status Inputs
The relay may be fitted with up to 27 status inputs. The user can program the relay to use any status input
for any function. A timer is associated with each input and a pickup time setting may be applied to each
input. In addition each input may be logically inverted to allow easy integration of the relay within the user
scheme. Each input may be mapped to any front Fascia LED and/or to any Output Relay contact. This
allows the Relay to act as panel indication for alarms and scheme status without having to use additional
external flagging elements.
2.4 Output Relays
The relay is fitted with up to 29 output relays, all of which are capable of handling circuit breaker tripping
duty. All relays are fully user configurable and can be programmed to operate from any or all of the control
functions. There are three relays on the Power Supply/Basic I/O module that have C/O contacts and 2 with
N/O contacts. Additional modules are fitted with 8 N/O contacts although N/C contacts are available as an
option.
In their normal mode of operation output relays remain energised for a minimum of 100msec and a
maximum dependent on the energising condition duration. If required, however, outputs can be
programmed to operate as latching relays. These latched outputs can be reset by either pressing the
TEST/RESET button, or by sending an appropriate communications command.
The operation of the contacts can be simply checked by using the Protection Healthy setting on the Output
Relay Menu to energise each relay in turn. Do not forget to reset this setting back to its correct value.
The output relays can be used to operate the trip coils of the circuit breaker directly if the circuit breaker
auxiliary contacts are used to break the trip coil current and the contact rating of the relay output contacts
is not exceeded for 'make and carry' currents.
With a failed breaker condition the current 'break' may be transferred to the relay output contacts and
where this level is above the break rating of the contacts an auxiliary relay with heavy-duty contacts should
be utilised.
2.5 Fascia LEDS
In the E12 and E16 case there are 32 user programmable LED flag indicators. By opening the front panel it
is possible to insert a strip into a slip in pocket, which provides legend information about the meaning of
each LED. The legend may be specified when ordering the relay or alternatively the user can create a
customized legend. The user can customise which LED is used for which purpose as well as being able to
program each LED as being latching or self –resetting.
2.6 Self Monitoring
The relay incorporates a number of self-monitoring features. Each of these features can initiate a
controlled reset recovery sequence, which can be used to generate an alarm output. In addition, the
Protection Healthy LED will give visual indication.
A watchdog timer continuously monitors the microprocessor. If the software fails to service the watchdog
timer the watchdog will time out and cause a reset.
The Output Relay modules are blocked in hardware if the watchdog timer expires.
©2010 Siemens Protection Devices Limited
Chapter 1 Page 4 of 13