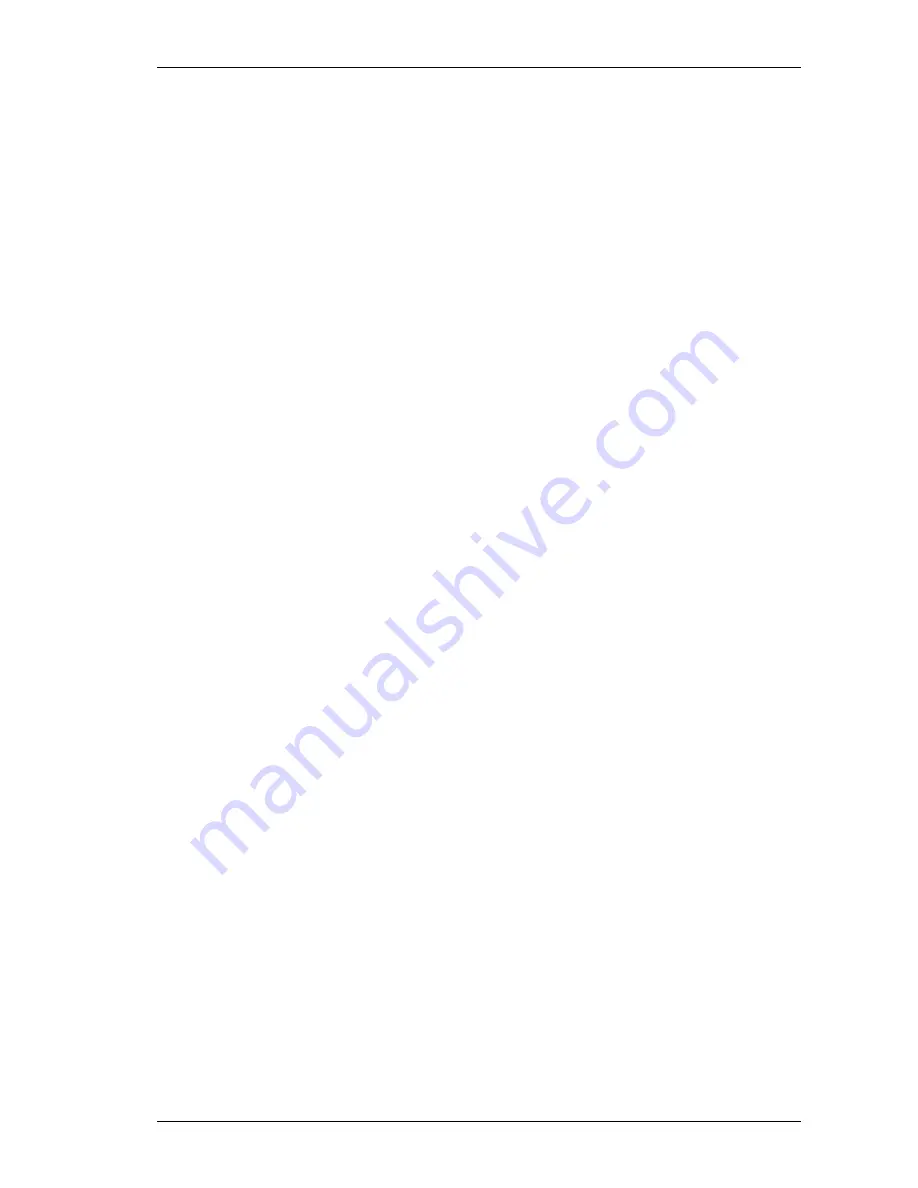
7SG15 MicroTAPP Description of Operation
©2013 Siemens Protection Devices Limited
Chapter 1 Page 24 of 38
Note that the password validation screen also displays a numerical code. If the password is lost or forgotten, this
code can be communicated to Siemens Protection Devices Ltd by authorised personnel, and the password can
be retrieved.
The relay is supplied with the password set to "NONE" which means the feature is de-activated.
8
User Interface
The user interface either via the LCD or a PC is designed to provide a user-friendly method of entering settings
and retrieving data from the relay.
8.1 General
Arrangement
The MicroTAPP relay fascia includes a 40 character by 8 line, back-lit, liquid crystal display, 5 light emitting
diodes and 5 push buttons. Appendix A shows the layout for the E8 case size.
Detailed drawings for both the E8 and E12 wiring connector blocks are available from the Siemens Protection
Devices Ltd website.
8.1.1 Liquid Crystal Display
The liquid crystal display is used to present settings, instruments and fault data in a textual format.
The display contrast is factory set. It can be adjusted if required as follows:-
1. Press and hold the right most button.
2. Press either the left most or second left buttons to increase or decrease the contrast.
8.1.2 LED Indications
8.1.2.1 MicroTAPP Healthy
A green LED labelled ‘Relay Healthy’ is provided.
When the relay is powered up and running normally the LED will be on permanently. If a permanent fault is
detected by the internal self-monitoring algorithms and watchdog the LED will flash continuously.
8.1.2.2 Voltage Normal
A green LED indicates that the measured voltage is normal.
8.1.2.3 Voltage High
A red LED indicates that the measured voltage is above the relay deadband setting. If the over-voltage monitor
has detected a failure the LED will flash.
8.1.2.4 Voltage Low
A red LED indicates that the measured voltage is below the relay deadband setting. If the under-voltage monitor
has detected a failure the LED will flash.
8.1.2.5 Tap in progress
An amber LED indicates that the tap change mechanism is in the operating state. If the tap change monitor has
detected a failure the LED will flash.
8.2 Keypad
and
Display
Five push buttons are used to control and set-up all aspects of the voltage control system. The use of each button
is indicated by a label above the button in the lower portion of the LCD.
When the voltage is ‘normal’ a graphical display showing the previous 15 minutes or one hour of voltage level is
displayed together with the measured system voltage and the tap position.