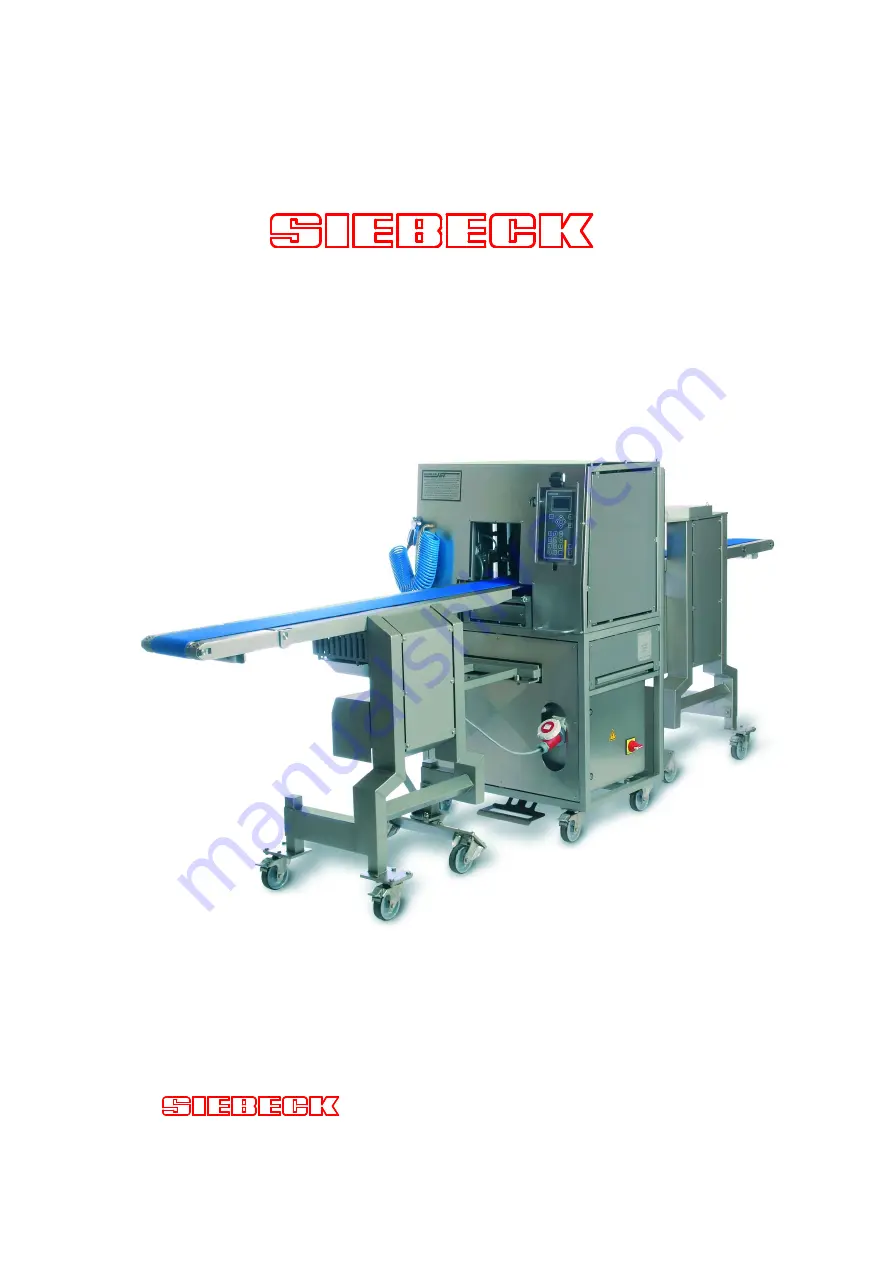
Translation of the original operating manual
No. 0411 FRT-A-MKIIIbed
JET 2000 tying machine
MK III series
FRT-A-SB and FRT-AS-SB model series
GMBH
Tel49 (0)6271 9208 0
e-mail : [email protected]
69412 EBERBACH, GERMANY
Fax +49 (0)6271 9208 88
Internet : www.siebeck.de