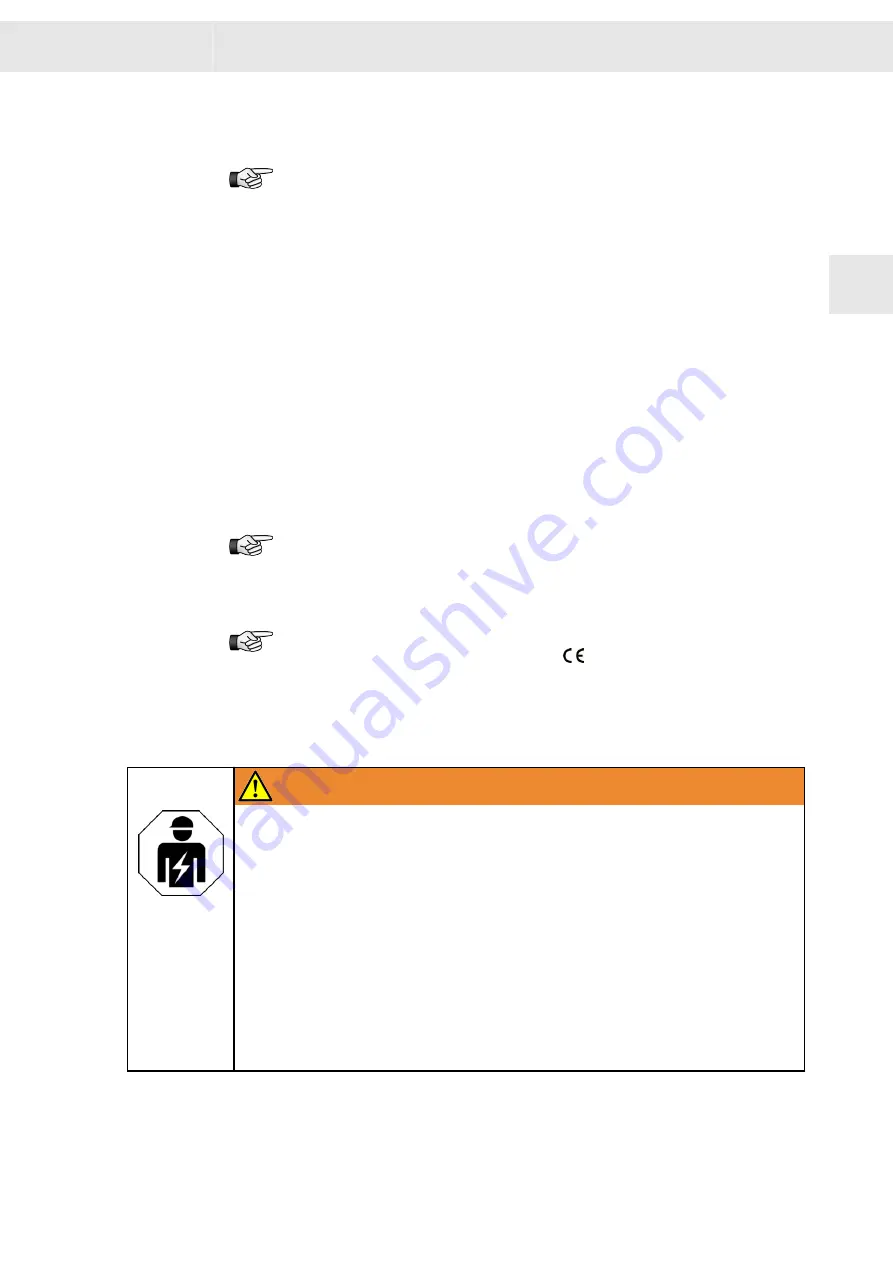
3
Safety Instructions
These safety instructions include important information regarding your safety
and must be observed during installation and operation of SIEB & MEYER
devices. Read them carefully and keep them for later use.
Also adhere to safety instructions in the product documentation and on the
device.
3.1
Standards and Regulations
SIEB & MEYER devices comply with the regulations of the following standards and
directives:
▶
Low-Voltage Directive 2014/35/EU:
EU declaration of conformity, DIN EN 61800-5-1
▶
EMC Directive 2014/30/EU:
EU manufacturer's certificate, DIN EN 61800-3
▶
Machinery Directive 2006/42/EC:
EU manufacturer's certificate, DIN EN 61800-5-2 (safety functions)
SIEB & MEYER products are no products according to the EU Machinery
Directive. The appropriate use of SIEB & MEYER devices in machines and
installations is prohibited until the manufacturer of the machine or installation
confirms the CE conformity of the complete machine or installation.
If the mechanics or the electronics of the device are modified, the conformity
with the EC/EEC directives and thus the
label will expire.
3.2
Working on the Device
WARNING
Trained staff only
To avoid risks of serious injuries and material damage any works regarding instal‐
lation, initial operation and maintenance must be carried out by trained staff only.
Furthermore, electricians who connect feed-in systems must be approved by the
local DSO (distribution system operator).
Trained staff, according to this fundamental safety instruction, are persons familiar
with the installation, mounting, initial and permanent operation of the product and
they are qualified appropriately for the work. The standards DIN VDE 0100 and
DIN VDE 0110 as well as the national accident prevention regulations shall be
considered!
When installing feed-in systems adhere to all applicable regulations, special safety
instructions and technical connection conditions of the local DSO.
W
Safety Instructions
Drive System SD2S - Hardware Description 0362X49xy / 0362129xy
17
3
Summary of Contents for SD2S 0362249xy
Page 4: ...Chapter Overview W 4 Drive System SD2S Hardware Description 0362X49xy 0362129xy...
Page 8: ...Content W 8 Drive System SD2S Hardware Description 0362X49xy 0362129xy...
Page 12: ...About this Manual W 12 Drive System SD2S Hardware Description 0362X49xy 0362129xy 1...
Page 16: ...General Information W 16 Drive System SD2S Hardware Description 0362X49xy 0362129xy 2...
Page 30: ...Drive Amplifier SD2S W 30 Drive System SD2S Hardware Description 0362X49xy 0362129xy 5...
Page 54: ...Connector Pin Assignment W 54 Drive System SD2S Hardware Description 0362X49xy 0362129xy 7...
Page 80: ...Setup W 80 Drive System SD2S Hardware Description 0362X49xy 0362129xy 9...