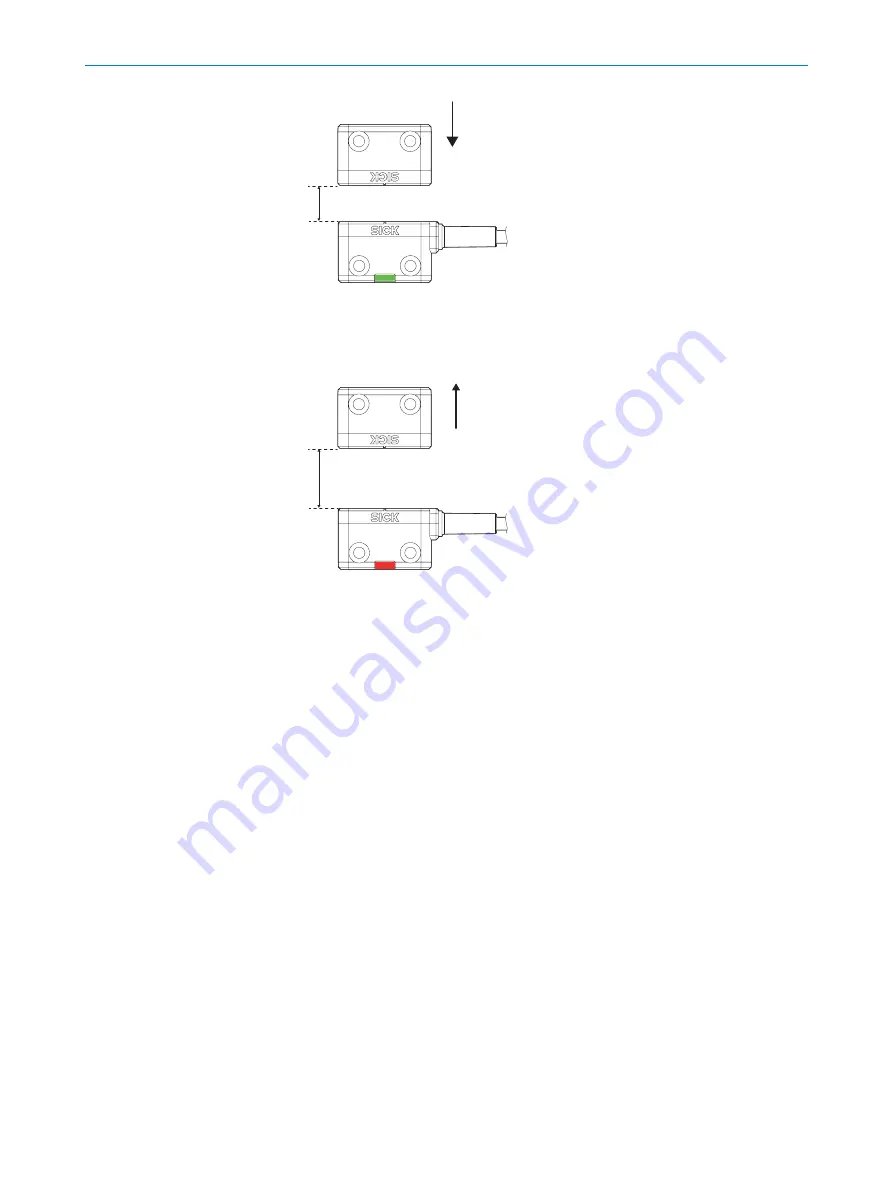
S
ao
Figure 1: Assured switch-on distance S
ao
•
Assured switch off distance S
ar
If the actuator is removed from the sensor and the assured switch-off distance is
reached, the OSSDs safely switch to the OFF state.
S
ar
Figure 2: Assured switch off distance S
ar
•
Typical switch-on distance
If the actuator approaches the sensor, the OSSDs typically switch to the ON state
before the actuator reaches assured switch-on distance S
ao
. The typical switch-on
distance depends on the ambient conditions.
The exact values of the sensing ranges depend on different factors.
Further topics
•
4.4
Integration into the electrical control
Switch-on commands that put the machine in a dangerous state may only be activated
when the protective device is closed. When the machine goes into a dangerous state, a
stop command must be triggered if the protective device is opened. Depending on the
safety concept, the signal is analyzed by safety relays or a safety controller, for example.
The control that is connected and all devices responsible for safety must comply with
the required performance level and the required category (for example, according to
ISO 13849-1).
4.4.1
Course of the OSSD test over time
The device tests the OSSDs for self-diagnosis at regular intervals. To do this, the device
switches each OSSD briefly to the OFF state and checks whether this channel is volt‐
age-free during this time.
Make sure that the machine’s control does not react to these test pulses and the
machine does not switch off.
PROJECT PLANNING
4
8018754/12IU/2020-01-30 | SICK
O P E R A T I N G I N S T R U C T I O N S | STR1
13
Subject to change without notice