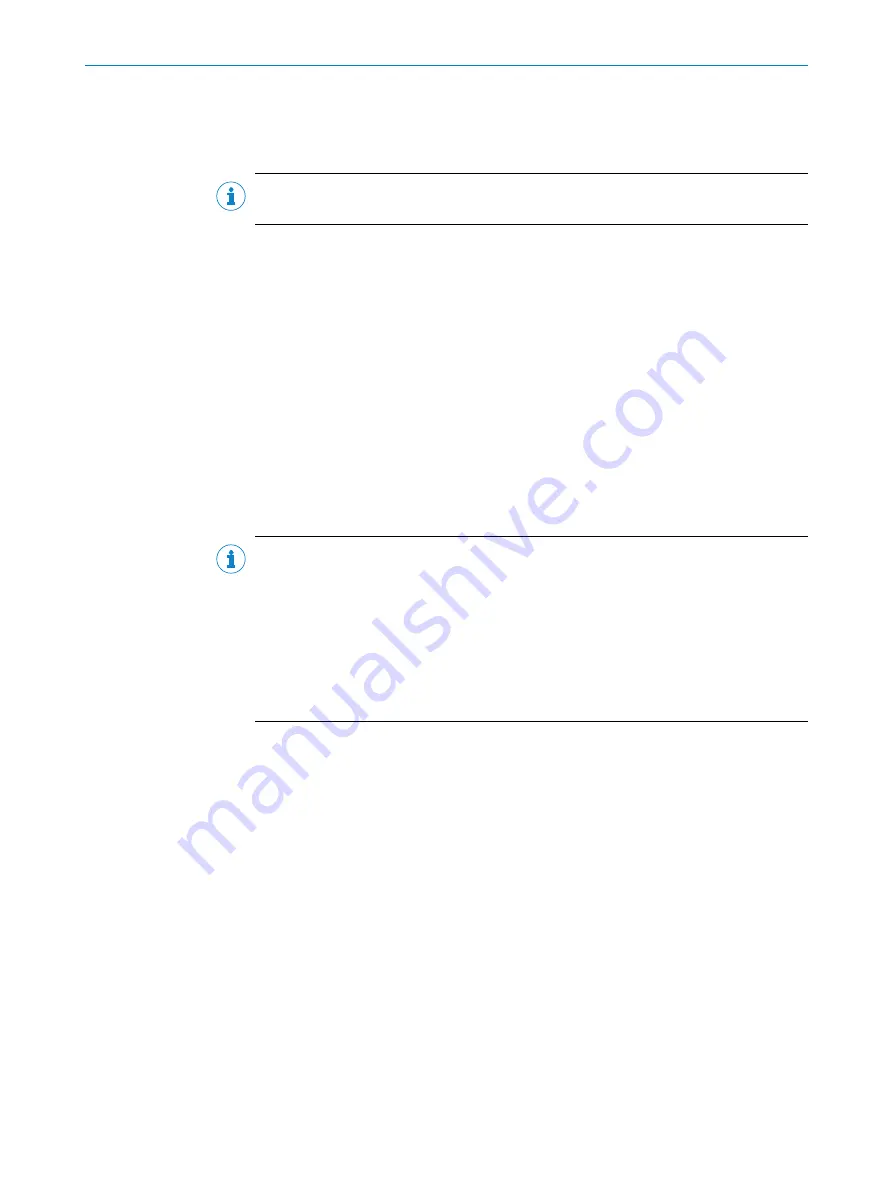
6
Electrical installation
6.1
Electrical installation of the components
NOTE
Information is included in the operating instructions for the components.
6.2
General requirements
The manufacturer must take measures against failures resulting from the same cause.
The manufacturer must document this appropriately in SISTEMA. During the electrical
installation, the following, for example, must be taken into consideration:
•
Protection against overvoltage, overcurrent, etc. per the manufacturer instructions
for the individual components
•
Mechanical fastening of the wiring of the pushbutton for the hold to run device,
e.g. with cable ties
•
Measures for controlling the consequences of voltage failure, voltage fluctuations,
overcurrent and undercurrent in the voltage supply of the robot controller
6.3
Safety controller pin assignment
Important information
NOTE
The gateway and safety laser scanner have 2 switched connections each. These allow
for several connections, also with additional switches.
•
Gateway > safety laser scanner > robot controller
•
Gateway > robot controller
Gateway > safety laser scanner
•
Gateway > switch
Safety laser scanner > switch
Robot controller > switch
ELECTRICAL INSTALLATION
6
8024758/2020-02-20 | SICK
O P E R A T I N G I N S T R U C T I O N S | sBot Speed CIP – KU
35
Subject to change without notice