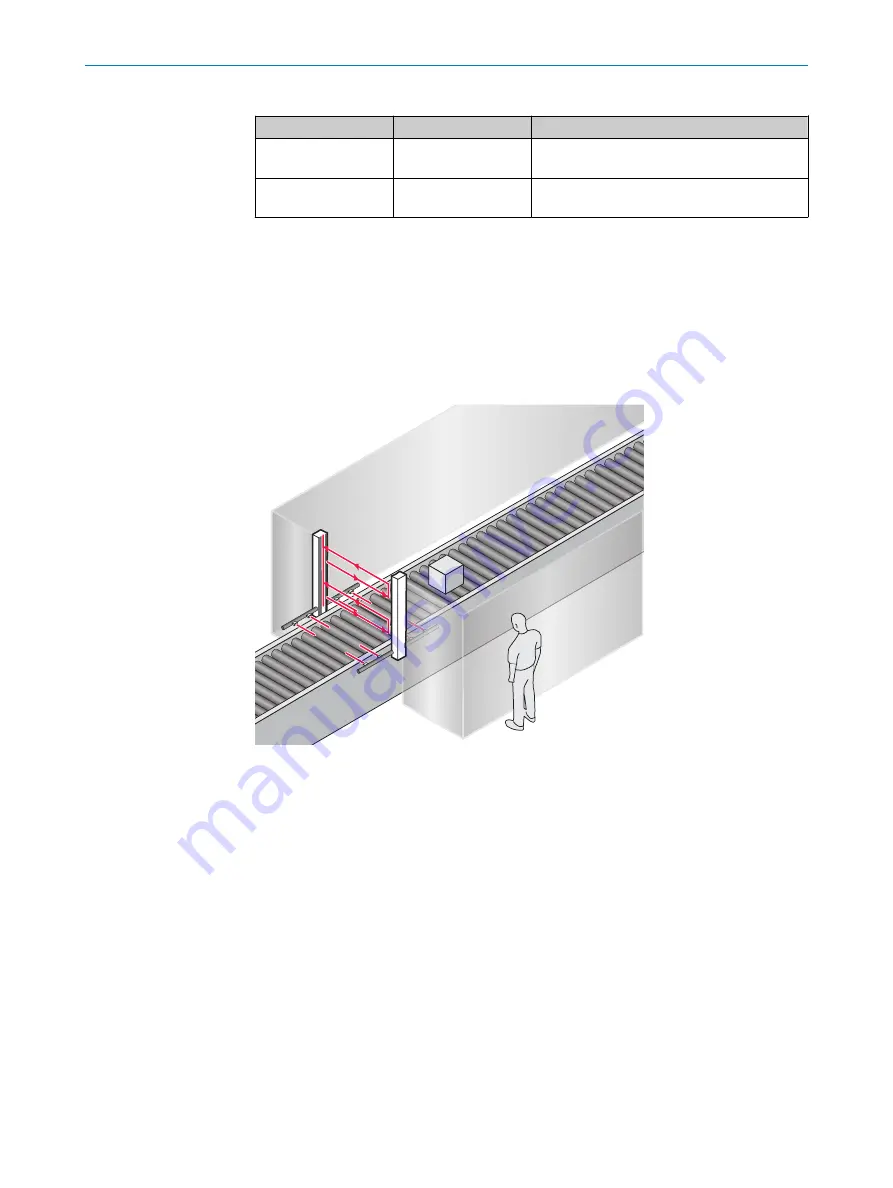
Table 6: Warnings
Diagnostics LED
Color
Meaning
1 ... 8
O
Yellow
A yellow illuminated diagnostic LED signals
which function is affected.
1 ... 8
Ö
Yellow
A yellow flashing diagnostic LED signals the
reason for the warning.
o
LED off.
Ö
LED flashes.
O
LED illuminates.
Example: If diagnostic LED 5 lights up yellow and diagnostic LED 3 flashes yellow, the
sensor gap monitoring was exceeded.
Further topics
•
3.3
Example applications
Figure 7: Access protection
PRODUCT DESCRIPTION
3
8024802/2020-07-17 | SICK
O P E R A T I N G I N S T R U C T I O N S | deTem4 LT Muting A/P
17
Subject to change without notice