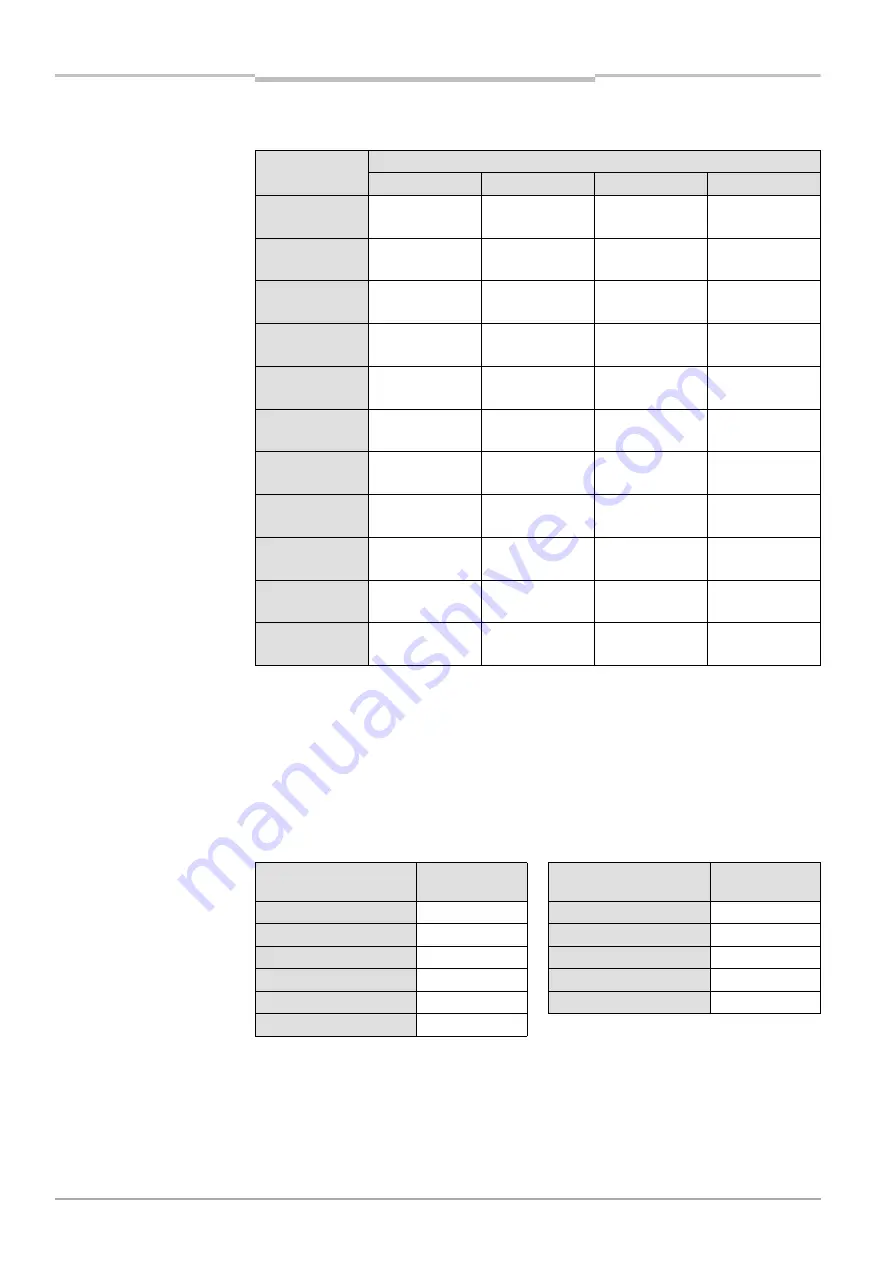
Operating Instructions
Chapter
11
C 4000
56
©
SICK AG • Safety Systems • Germany • All rights reserved
8 009 221/16-11-00
Ordering information
11.3.2
Cascadable system with function package B
11.4 Additional front screen (welding spark guard)
Notes
·
One additional front screen (welding spark guard) supplied for each part number.
·
The additional front screen fits both on the sender and on the receiver.
·
The additional front screen may be used only if the curved enclosure side is accessible.
·
An additional front screen reduces the scanning range of the system by 8%. If sender and
receiver each use an additional front screen, the scanning range will be reduced by 16%.
Protective field
height [mm]
Part numbers for resolution
14 mm
20 mm
30 mm
40 mm
300
I
1 018 690
H
1 018 827
I
1 018 710
H
1 018 838
I
1 018 733
H
1 018 849
I
1 018 755
H
1 018 860
450
I
1 018 349
H
1 018 828
I
1 018 712
H
1 018 839
I
1 018 735
H
1 018 850
I
1 018 757
H
1 018 861
600
I
1 018 692
H
1 018 829
I
1 018 714
H
1 018 840
I
1 018 737
H
1 018 851
I
1 018 759
H
1 018 862
750
I
1 018 694
H
1 018 830
I
1 018 716
H
1 018 841
I
1 018 739
H
1 018 852
I
1 018 762
H
1 018 863
900
I
1 018 696
H
1 018 831
I
1 018 718
H
1 018 842
I
1 018 741
H
1 018 853
I
1 018 765
H
1 018 864
1050
I
1 018 698
H
1 018 832
I
1 018 720
H
1 018 843
I
1 018 743
H
1 018 854
I
1 018 767
H
1 018 865
1200
I
1 018 700
H
1 018 833
I
1 018 722
H
1 018 844
I
1 018 745
H
1 018 855
I
1 018 769
H
1 018 866
1350
I
1 018 702
H
1 018 834
I
1 018 724
H
1 018 845
I
1 018 747
H
1 018 856
I
1 018 771
H
1 018 867
1500
I
1 018 704
H
1 018 835
I
1 018 726
H
1 018 846
I
1 018 749
H
1 018 857
I
1 018 773
H
1 018 868
1650
I
1 018 706
H
1 018 836
I
1 018 728
H
1 018 847
I
1 018 751
H
1 018 858
I
1 018 775
H
1 018 869
1800
I
1 018 708
H
1 018 837
I
1 018 730
H
1 018 848
I
1 018 753
H
1 018 859
I
1 018 777
H
1 018 870
Tab. 26: Part numbers,
cascadable system with
function package B
Protective
field height [mm]
Part number
Protective
field height [mm]
Part number
300
2 022 412
1200
2 022 418
450
2 022 413
1350
2 022 419
600
2 022 414
1500
2 022 420
750
2 022 415
1650
2 022 421
900
2 022 416
1800
2 022 422
1050
2 022 417
Tab. 27: Part numbers,
additional front screen
(welding spark guard)