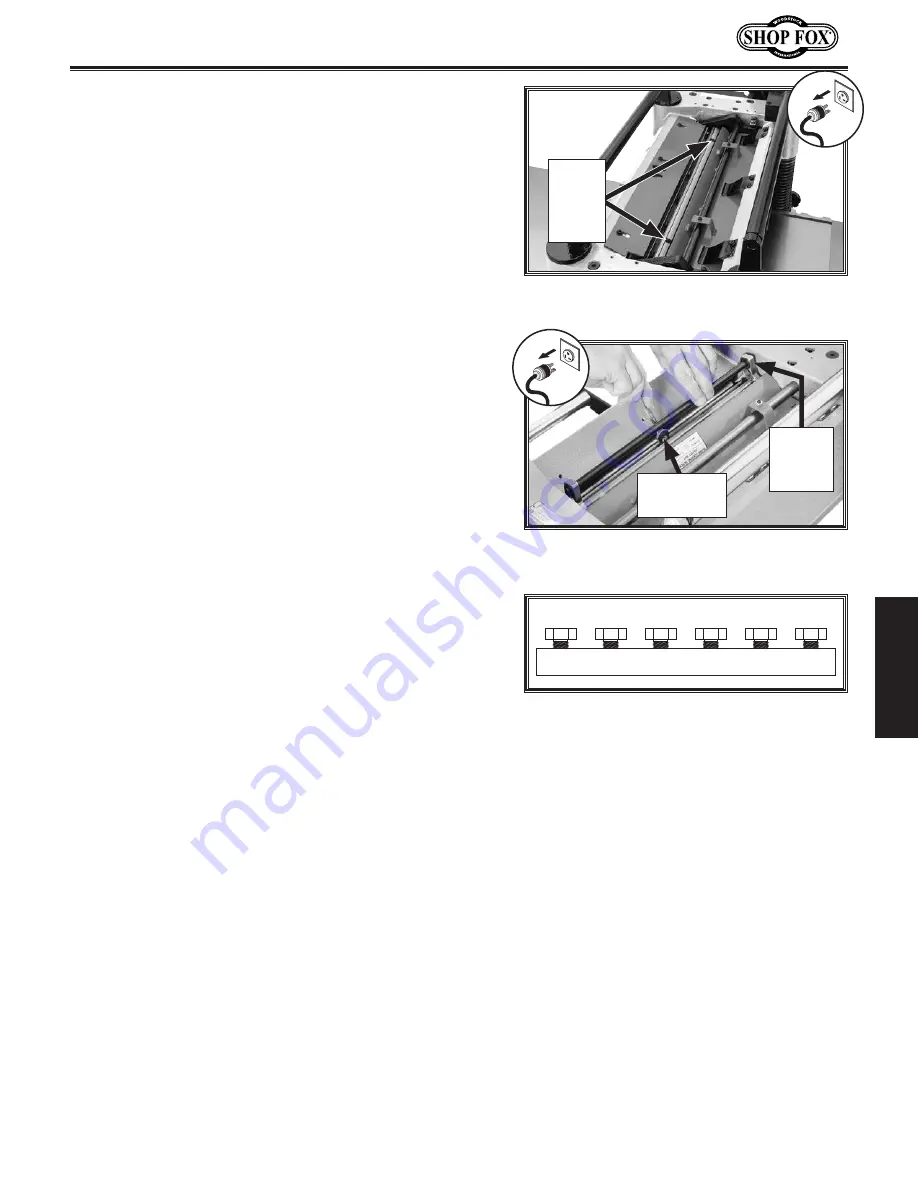
-33-
Model W1864/W1865 (For Machines Mfd. Since 02/19)
O
PE
R
ATIO
NS
7.. Jack.Screws:
Insert hex wrench into access holes in
cutterhead (see
Figure.25
), and rotate jack screws
to raise or lower knife until it barely touches center
pad of knife-setting jig with all legs of jig still firmly
on cutterhead, then snug gib bolts enough to hold
knife in place without fully tightening gib bolts (see
Figure.26
).
Springs:.
Insert hex wrench into access holes in
cutterhead (see
Figure.25
), and remove jack screws.
Push down on knife jig until all legs of jig are firmly
on cutterhead and knife just touches center pad
of jig, then tighten gib bolts enough to hold knife
in place without fully tightening gib bolts (see
Figure.26
).
2
1
3
5
4
6
Figure.27..
Gib bolt tightening sequence.
Figure.25.
Jack screw access holes in
cutterhead.
Figure.26.
Using knife-setting jig to set
knife height.
Tightening
Gib Bolt
Knife-
Setting
Jig
Jack
Screw
Access
Holes
9..
Repeat
Step.8
, snugging gib bolts a little more.
10.
Repeat
Step.8
, this time fully tightening all gib
bolts.
11..
Repeat
Steps.4–8
for remaining knives.
8..
Incrementally snug gib bolts in an even manner,
starting at middle and working your way to ends by
alternating left and right, as illustrated in
Figure.27
.
Summary of Contents for W1864
Page 73: ...Model W1864 W1865 For Machines Mfd Since 02 19...
Page 76: ......