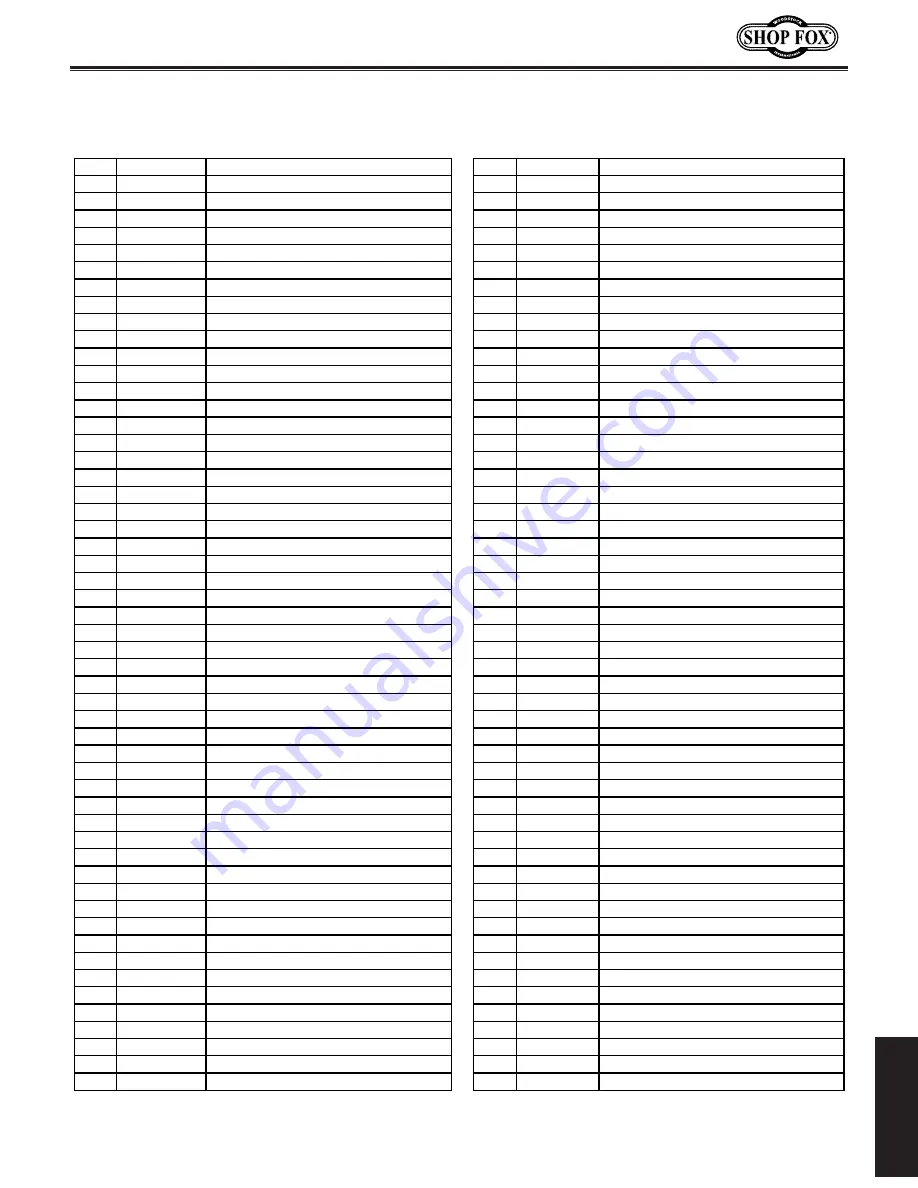
-29-
Model W1831 (For Machines Mfd. Since 6/15)
PA
RT
S
Main.Parts.List
REF PART #
DESCRIPTION
REF PART #
DESCRIPTION
1
X1831001
SPINDLE HEX NUT M10-1.5
38
XPHTEK31M TAP SCREW M4 X 14
2-1
X1831002-1
SPINDLE WASHER 5/8" OD
39
XPW05M
FLAT WASHER 4MM
2-2
X1831002-2
SPINDLE WASHER 7/8" OD
40
X1831040
TAP SCREW M4 X 110
2-3
X1831002-3
SPINDLE WASHER 1-3/4" OD
41
XPHTEK8M
TAP SCREW M4 X 20
3
X1831003
SANDING SLEEVE SET OF 6
42
X1831042
BEARING COVER
3-1
X1831003-1
SANDING SLEEVE 1/2"
43
X1831043
FELT WASHER
3-2
X1831003-2
SANDING SLEEVE 3/4"
44
X1831044
RUBBER WASHER
3-3
X1831003-3
SANDING SLEEVE 1"
45
XP6203ZZ
BALL BEARING 6203ZZ
3-4
X1831003-4
SANDING SLEEVE 1-1/2"
46
X1831046
UPPER BEARING SUPPORT
3-5
X1831003-5
SANDING SLEEVE 2"
47
XPHTEK6M TAP SCREW M4 X 16
3-6
X1831003-6
SANDING SLEEVE 3"
48
X1831048
BEARING SLEEVE
4-1
X1831004-1
SANDING DRUM 3/4"
49
X1831049
COMPRESSION SPRING
4-2
X1831004-2
SANDING DRUM 1"
50
XPR18M
EXT RETAINING RING 17MM
4-3
X1831004-3
SANDING DRUM 1-1/2"
51
X1831051
SPINDLE WASHER
4-4
X1831004-4
SANDING DRUM 2"
52
XPHTEK31M TAP SCREW M4 X 14
4-5
X1831004-5
SANDING DRUM 3"
53
X1831053
DRIVE GEAR PLATE
5-1
X1831005-1
TABLE INSERT 1/2" ID
54
X1831054
DRIVE GEAR
5-2
X1831005-2
TABLE INSERT 3/4" ID
55
X1831055
SPINDLE
5-3
X1831005-3
TABLE INSERT 1" ID
56
X1831056
WOODRUFF KEY
5-4
X1831005-4
TABLE INSERT 1-1/2" ID
57
X1831057
DIFFERENTIAL GEAR
5-5
X1831005-5
TABLE INSERT 2" ID
58
X1831058
BEARING SLEEVE
5-6
X1831005-6
TABLE INSERT 3" ID
59
X1831059
DIFFERENTIAL GEAR PLATE
6
X1831006
BASE WASHER 2-3/4" OD
60
XPHTEK31M TAP SCREW M4 X 14
7
X1831007
CAST IRON TABLE
61
XPHTEK31M TAP SCREW M4 X 14
8
X1831008
GASKET
62
X1831062
LOWER BEARING SUPPORT
9
X1831009
DUST COVER
63
XP6203ZZ
BALL BEARING 6203ZZ
10
XPW02M
FLAT WASHER 5MM
64
X1831064
RUBBER WASHER
11
XPLW01M
LOCK WASHER 5MM
65
X1831065
FELT WASHER
12
XPS08M
PHLP HD SCR M5-.8 X 12
66
X1831066
GEAR SUPPORT
13
X1831013
TIMING BELT 3/8" X 160XL
67
X1831067
WIRE ASSEMBLY 18G 1W 9"
14
X1831014
TIMING BELT 1/4" X 160XL
68
X1831067
WIRE ASSEMBLY 18G 1W 9"
15
X1831015
DRIVE PULLEY
69
X1831069
RECTIFIER
16
X1831016
TENSION ROLLER WASHER
70
XPHTEK8M
TAP SCREW M4 X 20
17
X1831017
TENSION ROLLER ASSEMBLY
71
X1831071
WIRE ASSEMBLY 18G 1W 6"
18
XPHTEK31M
TAP SCREW M4 X 14
72
X1831071
WIRE ASSEMBLY 18G 1W 6"
19
X1831019
ORIENTATION PLATE ASSEMBLY
73
X1831073
POWER CORD 18G 2W 6" 1-15
20
XPHTEK8M
TAP SCREW M4 X 20
74
X1831074
STRAIN RELIEF 6N-4
21
XPW03M
FLAT WASHER 6MM
75
X1831075
REAR SWITCH PLATE
22
XPLW03M
LOCK WASHER 6MM
76
X1831076
HOUSING BASE
23
XPS11M
PHLP HD SCR M6-1 X 16
77
X1831077
FRONT SWITCH PLATE
24
X1831024
CORD CLAMP
78
X1831078
SAFETY PADDLE SWITCH
25
XPHTEK6M
TAP SCREW M4 X 16
79
X1831079
SWITCH BRACKET
26
XP6001ZZ
BALL BEARING 6001ZZ
80
X1831080
SWITCH BRACKET COVER
27
XPR47M
EXT RETAINING RING 13MM
81
XPS56M
PHLP HD SCR M4-.7 X 16
28AV2 X1831028AV2 MOTOR ASSEMBLY V2.06.15
82
X1831082
POWER CORD HOLDER
28
X1831028
ARMATURE ASSEMBLY
83
XPHTEK6M
TAP SCREW M4 X 16
29
XP608ZZ
BALL BEARING 608ZZ
84
X1831084
CABLE HOLDER 18G
30
X1831030
CONNECTION PLATE
85
XPHTEK15M TAP SCREW M4 X 10
31
X1831031
FIELD ASSEMBLY
86
X1831086
RUBBER FOOT
32
X1831032
REAR COVER
87
XPW03M
FLAT WASHER 6MM
32-1
X1831032-1
VENTED MOTOR COVER
88
XPLW03M
LOCK WASHER 6MM
33A
X1831033A
MOTOR BRUSH ASSEMBLY 1 PAIR
89
XPS11M
PHLP HD SCR M6-1 X 16
36
X1831036
CORD CLAMP
90
X1831090
BOTTOM PLATE
37
XPTLW11M
INT TOOTH WASHER 4MM
91
XPHTEK31M TAP SCREW M4 X 14