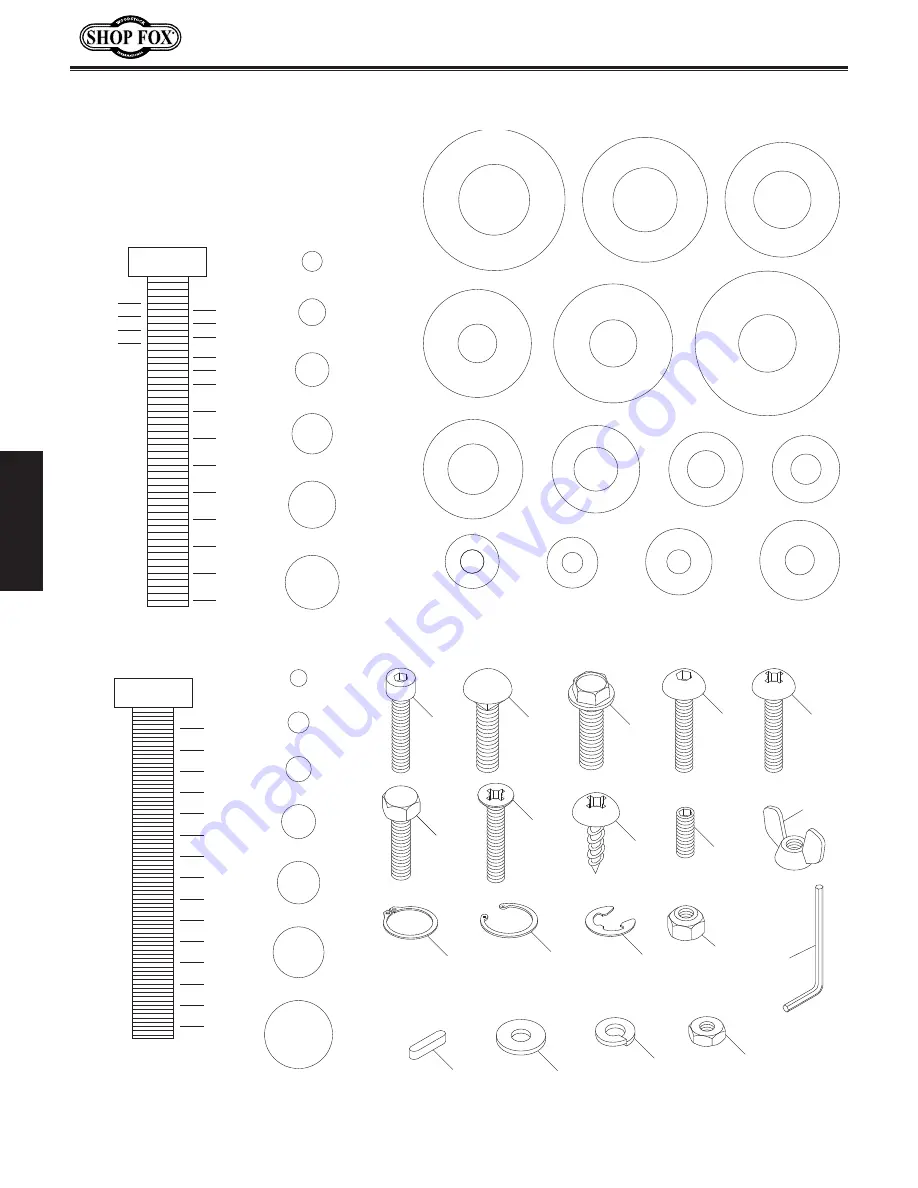
-14-
Model W1701 (Mfd. Since 12/21)
SE
TU
P
Hex
Wrench
16mm
MEASURE BOL
T DIAMETER BY
PLACING INSIDE CIRCLE
7
⁄
16
"
3
⁄
8
"
1
⁄
4
"
5
⁄
16
"
#10
1
⁄
2
"
W
ASHERS
ARE MEASURED BY
THE INSIDE DIAMETER
USE THIS CHART TO IDENTIFY
HARDWARE DURING THE
INVENTORY/ASSEMBLY
PROCESS.
Flat Washer
Lock
Washer
Hex
Nut
Wing
Nut
Set
Screw
Cap
Screw
Carriage
Bolt
Hex
Bolt
Button
Head
Screw
Flange
Bolt
LINES
AR
E
1
⁄
16
"
INCH AP
AR
T
1
⁄
4
"
3
⁄
8
"
1
⁄
2
"
5
⁄
8
"
5
⁄
16
"
7
⁄
16
"
9
⁄
16
"
3
⁄
4
"
7
⁄
8
"
3
2
1
⁄
4
"
2
1
⁄
2
"
2
3
⁄
4
"
2
1
3
⁄
4
"
1
1
⁄
2
"
1
1
⁄
4
"
1
LINES
ARE
1MM AP
AR
T
5mm
10mm
20mm
15mm
25mm
40mm
30mm
35mm
45mm
50mm
60mm
55mm
70mm
65mm
75mm
W
A
S
H
ER
D
IAM
ET
ER
5
⁄
8
"
W
A
S
H
E
R
DI
A
M
E
T
ER
9
⁄
16
"
1
⁄
2
"
W
A
SH
E
R
D
I
A
M
ET
E
R
W
A
S
HE
R
DIAM
E
T
ER
12mm
W
A
S
H
E
R DIAM
E
T
ER
10mm
7
⁄
16
"
W
A
SH
ER DIAM
E
T
ER
WA
SH
ER
DIAM
E
T
ER
8mm
3
⁄
8
"
W
A
S
H
E
R D
IAM
E
T
E
R
5
⁄
16
"
W
A
S
H
ER
DIA
M
E
T
E
R
1
⁄
4
"
W
A
S
H
ER
D I A M
E
T
ER
#10
W
A
S
H
E R
D I A
M
E
T
ER
W
A
S
H
E
R D I A M
E
T
ER
4mm
WA
S
H
ER
D I A M
E
T
ER
6mm
WA
S
H
E R
D I A
M
E
T
ER
5mm
4mm
6mm
5mm
8mm
10mm
12mm
Tap
Screw
Phillips
Head
Screw
Flat
Head
Screw
E-Clip
External
Retaining
Ring
Internal
Retaining
Ring
Key
Lock
Nut
Hardware Recognition Chart