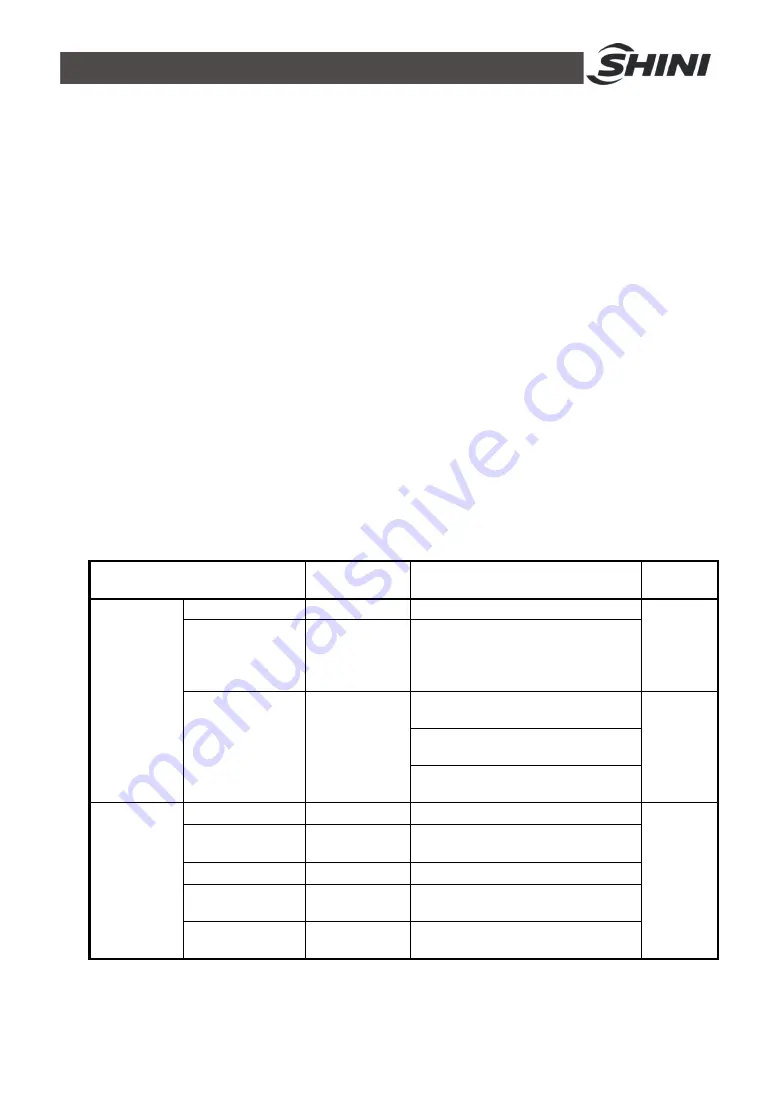
49(53)
2) When the machine stops due to faults, press down the main power switch first
(the alarming light goes out), then check the cause of the faults, the machine
should not be started forcibly before troubleshooting.
3) Do regular inspection inorder to prolong the lifespan of the system and avoid
the happening of accidents.
4) Because the high alkalescence will accelerate the rusting of copper pipe and
decrease the lifespan of the heat exchanger so it needs to do water quality
dispose for the system used water, the water PH value should be within the
range from 7.0 to 8.5.
5) Keep the machine room dry, clean and have good ventilation.
6) The daily operation, management and maintenance work should be carried
out by professionals. (Please notice that any disassembly or check during the
operation will be dangerous!)
7) In order to make sure the chiller is under good working performance, the user
should clean the condenser and evaporator timely to avoid furring
accumulation, and affect its heat exchange.
6.1
Maintenance Ltems
Maintenance item
Times
Qualification
standard(treatment)
Remark
Noise
Any time
Judge by listening
Vibration
Any time
Observe the tubing of the unit body
and parts to see if there is over
vibrating phenomenon
Stand 1
m ahead
of central
unit to
observe
Voltage when stops should be
±
10%
within rated voltage
Voltage when running should be
more than
±
10% of rated voltage
General
Power voltage
Any time
Voltage when starts should be more
than 85% of rated voltage
Clean
Any time
Keep clean at any time
Rust-cleaning
Any time
Clean the rust with iron brush
,
then
paint it with anti-rust paint
Balance
Any time
Lock up screws of every parts
Heat resistance
material scale off
Any time
Glue it with new adhesive
Out
appearance
of machine
Water leakage
1 time/month
Clean dew dish, do not let drainage
pipe be clogged