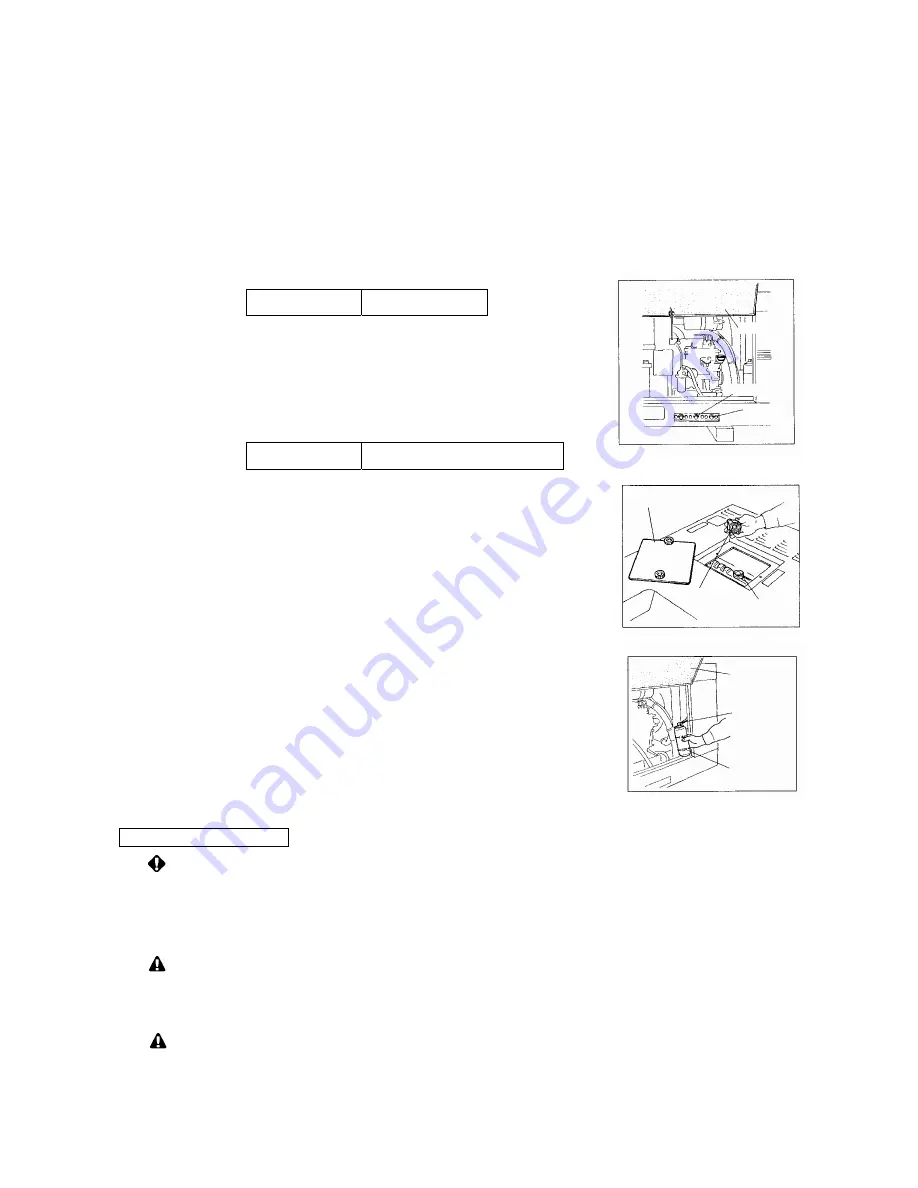
27
as well)
④
Reassemble it back.
<Caution>
z
Be sure to check for any contaminants on the packing, whenever reinstalling the cup.
z
Turn the fuel line valve lever
『
OPEN
』
after assembling, and check for any leak. Confirming
no leak, turn the fuel line valve
『
CLOSE
』
.
z
Fuel Element Part No.: 124550-55700 (Yanmar)
11.5 Draining Water from Fuel Tank
Drain Water
Every 200 hours
①
Unscrew the fuel drain plug.
②
Reinstall the drain plug, after draining the water entirdy.
11.6 Changing Coolant/Water
Replace
Every 1 year or 1000 hours
①
Remove the top plate.
②
Remove the radiator cap.
③
Loosen the water drain plug.
④
After draining all the water, reinstall the water drain plug.
⑤
Remove the reservoir tank and replace all the water.
⑥
Install the reservoir tank back, and fill the radiator with
coolant/water up to radiator filler neck. (Total cool-
ant/water Capacity is 3.1 liter.)
⑦
Reinstall the radiator cap.
⑧
Install the top plate back.
12. Long - Term Storage
Danger : Electric Shock
z
Before performing any equipment check or maintenance, stop the engine, and remove the
engine key. A person performing the maintenance should always keep the key.
Caution: Injuries
z
Before performing any equipment check or maintenance, stop the engine, and remove the
engine key. A person performing the maintenance should always keep the key.
Caution : Fire
・
Burns
z
When checking engine, always stop the engine, and keep away from fire.
z
Temperature around muffler and exhaust can get extremely high. Wait until the engine cools
down, before performing any checks.
SIDE DOOR
FUEL DRAIN
PLUG
WATER DRAIN
PLUG
TOP PLATE
RADIATOR CAP
WATER FILLER
SIDE DOOR
CAP
RESERVOIR TANK
Summary of Contents for DGW311DM
Page 31: ...30 14 Engine Wiring Diagram DGW311DM DGW311L...
Page 32: ...31 220V 60Hz 15 Generator Wiring Diagram...
Page 33: ...32 DGW311L W 220B 220V 60Hz...
Page 34: ...33 DGW311L W 380A 380V 50Hz...
Page 35: ...34 DGW311L W 400A 400V 50Hz...
Page 36: ...35 DGW311L W 415A 415V 50Hz...
Page 37: ...Head Office Telephone 81 82 849 2220 FAX 81 82 849 2481 71902 94012...