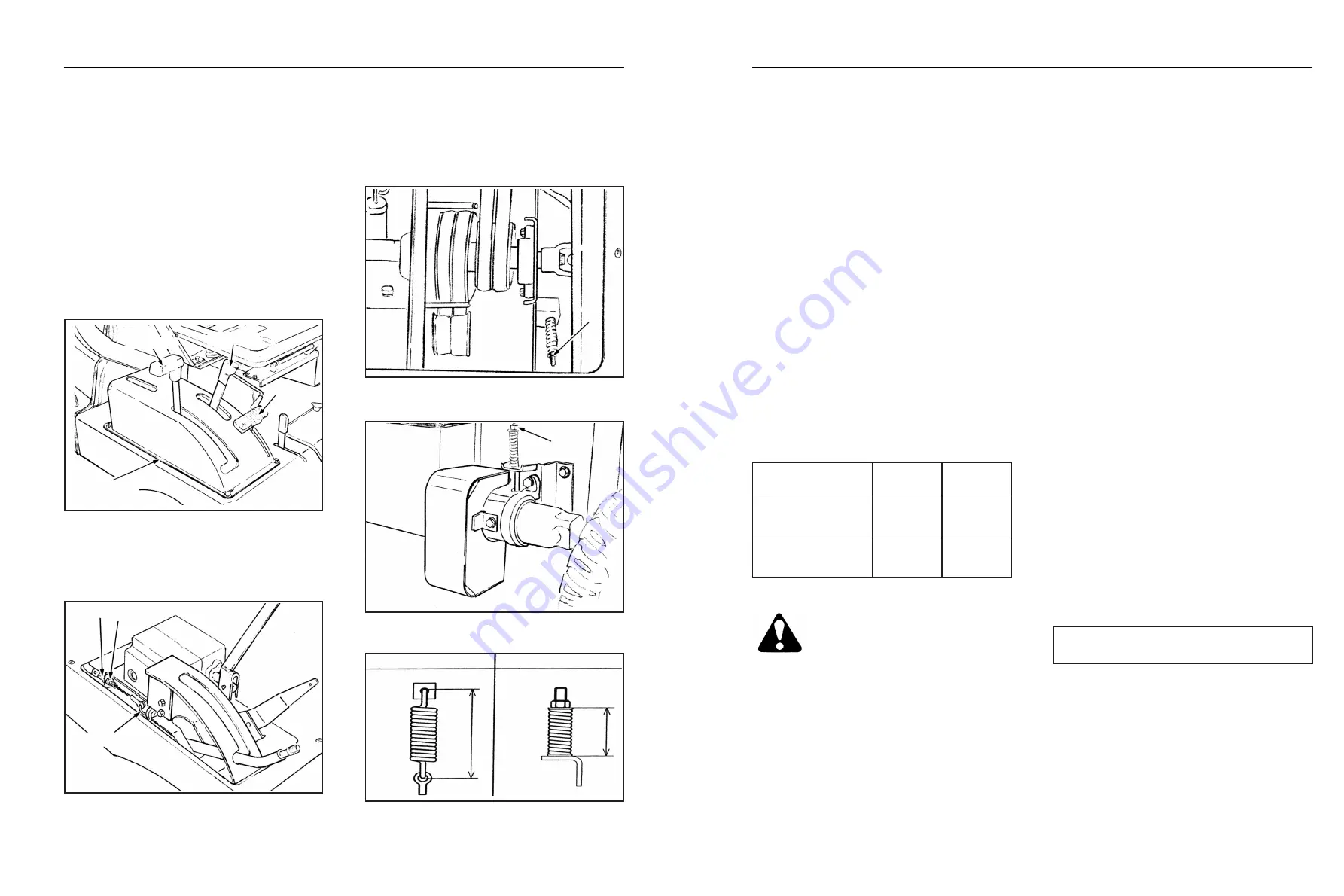
3-21
Adjust the PTO belt tension as follows.
Front-PTO Belt Tension.
1. Remove the grips on PTO control lever, accel
lever and HPL lever.
2. Remove the lever guide.
3. Place the PTO control lever at engaged
position.
4. Loosen the lock nut A at end of PTO wire
cable.
5. Adjust the spring length to 110
Ÿ
by turning
the adjuster nut
B
.
6. Tighten the lock nut
A
.
SIDE-PTO Belt Tension
1. Remove the under-seat cover.
2. Adjust the spring length to 57
Ÿ
by turning
the adjuster nut
A
.
3-20
TIRES
NOTE: Check tire pressure after every 50
hours of operation or weekly.
Tire inflation pressure affects the amount of
weight a tire can carry. Check the air pressure in
your Mower tires. If necessary, adjust the tire
pressure, being careful not to overinflate or
underinflate. Observe the following guidelines:
• Do not inflate a tire above the maximum
pressure shown on the tire. If the tire is not
marked, do not exceed the maximum
pressure shown in the Tire Inflation chart
found in this manual.
• Do not reinflate a tire that has been run flat or
seriously underinflated until the tire has been
inspected for damage by a qualified person.
• When checking tire pressure, inspect the tire
for damaged sidewalls and tread cuts.
Neglected damage leads to early tire failure.
WARNING: INFLATING OR SERVICING
TIRES CAN BE DANGEROUS. TRAINED
PERSONNEL SHOULD SERVICE AND/OR
MOUNT TIRES WHENEVER POSSIBLE.
If you must inflate or service tires, follow these
safety precautions to avoid injury or fatality.
• Make sure the rim is clean and free of rust.
• Lubricate both tire beads and rim flanges with
soap solution. Do not use oil or grease.
• Use a clip-on tire chuck with a remote hose
and gauge. This allows the operator to stand
clear of the tire while inflating.
• After seating the beads, adjust inflation
pressure to recommended operating
pressure.
• Do not inflate a tire unless the rim is mounted
on the Mower or is secured so that will not
move if the tire or rim should suddenly fail.
• Do not weld, braze, otherwise repair, or use a
damaged rim.
• Never attempt tire repairs on a public road or
highway.
• Use jack stands or other suitable blocking to
support the Mower while repairing tires.
• Ensure jack has adequate capacity to lift your
Mower.
• Place jack on a firm, level surface.
• Do not place any part of your body beneath
the Mower or start the engine while the
Mower is on the jack.
WHEEL BOLT TORQUE
Tighten the wheel bolts to the specified torque
anytime the wheel assembly is removed from
the mower or the wheel bolts are loosened.
Wheel Torque
74.5±9 N·m (760±90 kg-m)
NOTE: Torque for the wheels is the same for
front and rear axles.
Check wheel bolt torque daily until torque
stabilized.
LUBRICATION AND MAINTENANCE
Tire Size
20
×
10.00
−
8
−
4PR
16
×
10.00
−
8
−
4PR
Inflation
pressure
150 KPa
(1.5kgf/cm
2
)
190 KPs
(1.9kgf/cm
2
)
Max.
Load
5300 N
(540 kgf)
2750 N
(280 kgf)
LUBRICATION AND MAINTENANCE
PTO
CONTROL
HPL Lever
ACCEL
Lever
Lever Guide
LEVER GUIDE
A B
Spring
FRONT PTO BELT TENSION
1. Lock Nut
2. Adjuster Nut
A
SIDE-PTO BELT TENSION
1. Lock Nut
A
SIDE-PTO BELT TENSION
1. Lock Nut
FRONT-PTO
SIDE-PTO
110
57
TENSION SPRING LENGTH