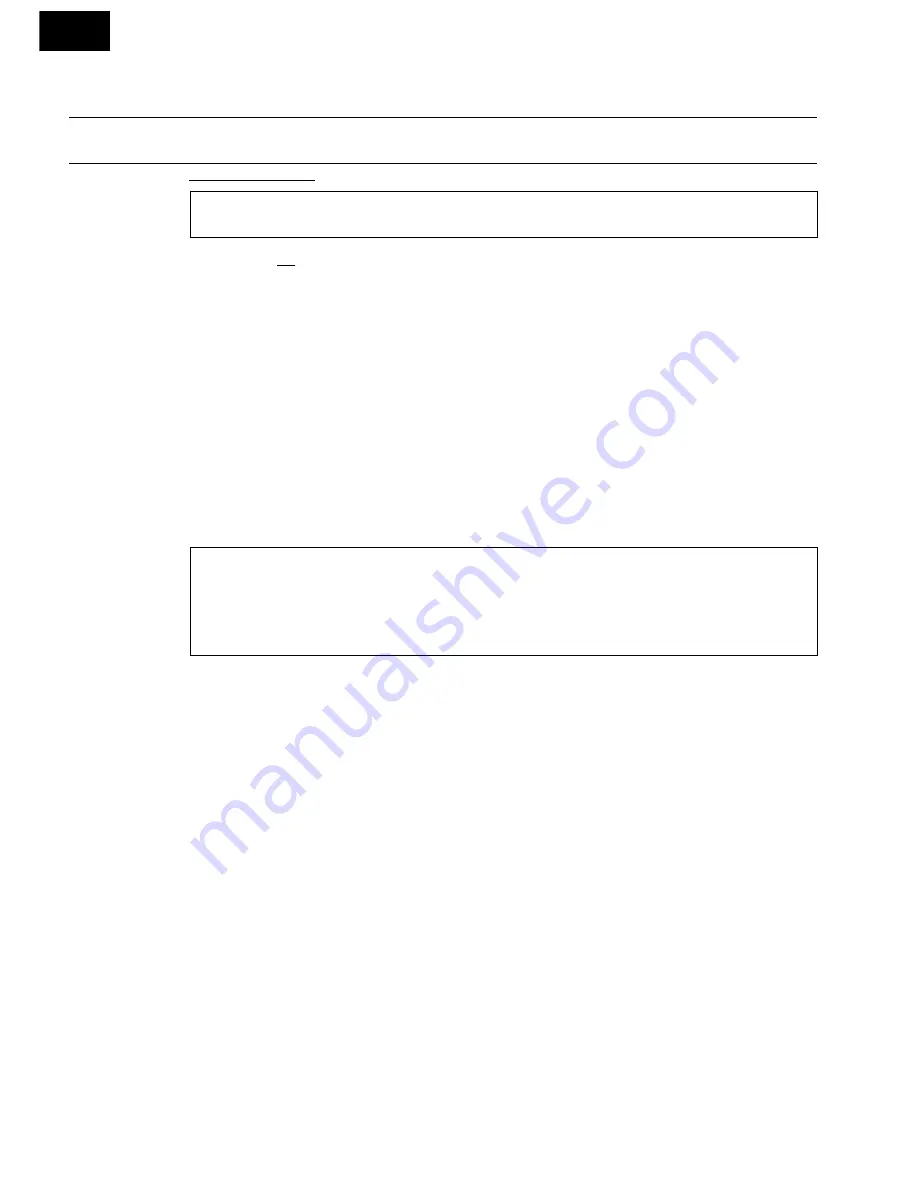
R-9H56
12
TEST PROCEDURES
PROCEDURE
LETTER
CARRY OUT 3D CHECK.
Isolate the magnetron from high voltage circuit by removing all leads connected to filament terminal.
To test for an open circuit filament use an ohmmeter to make a continuity test between the magnetron
filament terminals, the meter should show a reading of less than 1 ohm.
To test for short filament to anode condition, connect ohmmeter between one of the filament terminals
and the case of the magnetron (ground). This test should be indicated an infinite resistance. If a low or
zero resistance reading is obtained then the magnetron should be replaced.
MICROWAVE OUTPUT POWER (1 Litre water load)
The following test procedure should be carried out with the microwave oven in a fully assembled
condition (outer case fitted). Microwave output power from the magnetron can be measured by way of
IEC 705, i.e. it can be measured by using water load how much it can be absorbed by the water load.
To measure the microwave output power in the microwave oven, the relation of calorie and watt is used.
When P(W) heating works for t(second), approximately P x t/4.187 calorie is generated. On the other
hand, if the temperature of the water with V(ml) rises
∆
T (
°
C) during this microwave heating period, the
calorie of the water is V x
∆
T.
NEVER TOUCH ANY PART IN THE CIRCUIT WITH YOUR HAND OR AN INSULATED TOOL
WHILE THE OVEN IS IN OPERATION.
A
MAGNETRON TEST
The formula is as follows;
P x t / 4.187 = V x
∆
T
P (W) = 4.187 x V x
∆
T / t
Our condition for water load is as follows:
Room temperature..............around 20
°
C
Power supply Voltage.........Rated voltage
Water load.........1000 g Initial temperature...........10
±
2
°
C Heating time.........49 sec.
P = 85 x
∆
T
COMPONENT TEST
Measuring condition:
1. Container
The water container must be a cylindrical borosilicate glass vessel having a maximum material
thickness of 3 mm and an outside diameter of approximately 190 mm.
2. Temperature of the oven and vessel
The oven and the empty vessel are at ambient temperature prior to the start the test.
3. Temperature of the water
The initial temperature of the water is (10
±
2)
°
C.
4. Select the initial and final water temperature so that the maximum difference between the final water
temperature and the ambient temperature is 5
°
C.
5. Select stirring devices and measuring instruments in order to minimize addition or removal of heat.
6. The graduation of the thermometer must be scaled by 0.1
°
C at minimum and accurate thermometer.
7. The water load must be (1000
±
5) g.
8. “t” is measured while the microwave generator is operating at full power. Magnetron filament heat-
up time is not included.
NOTE: The operation time of the microwave oven is “t + 2” sec. 2 sec. is magnetron filament heat-up time.
Measuring method:
1. Measure the initial temperature of the water before the water is added to the vessel.
(Example: The initial temperature T1 = 11
°
C)
2. Add the 1 litre water to the vessel.
3. Place the load on the centre of the shelf.
4. Operate the microwave oven at HIGH for the temperature of the water rises by a value
∆
T of
(10
±
2)
°
C.
5. Stir the water to equalize temperature throughout the vessel.
Summary of Contents for R-9H56
Page 2: ...R 9H56 ...
Page 47: ...R 9H56 45 ...
Page 48: ...R 9H56 46 94SHARP CORP 11K0 620E Printed in Australia ...