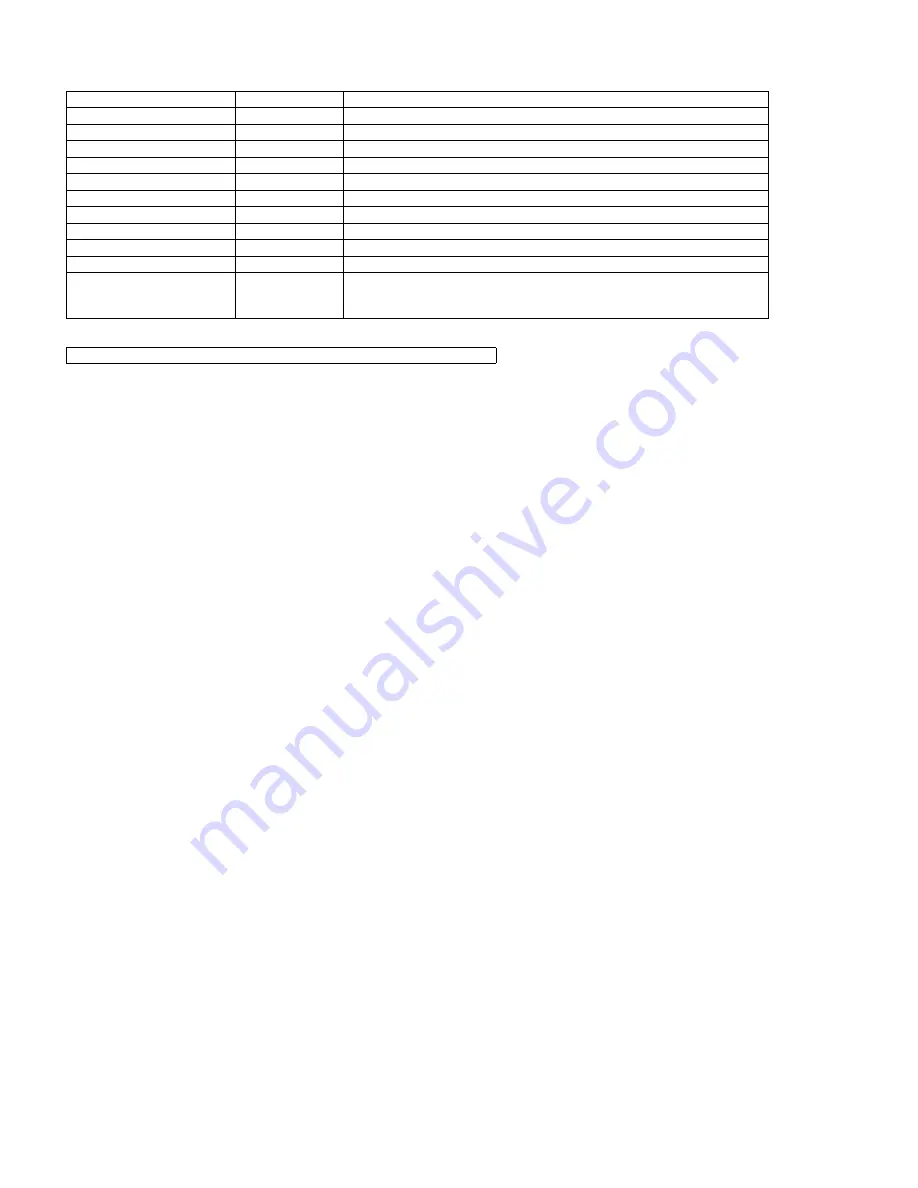
R939(W)
13 – 1
R939(W)
Service Manual
CHAPTER 13.
TEST DATA AT A GLANCE
PARTS
SYMBOL
VALUE / DATA
Fuse
F1
20A 250V
Fuse (Noise filter)
F2
F8A
Thermal cut-out
TC1
125
°
C Off
Thermal cut-out
TC2, TC3
170
°
C Off / 155
°
C On
Thermistor
Approx. 359.9 k
Ω
- 152 k
Ω
at 20
°
C - 30
°
C
Grill heating element
GH
Approx. 37.4
Ω
- 39.7
Ω
[(18.7
Ω
- 19.85
Ω
) x 2] / Insulation resistance > 10M
Ω
Convection heating element
CH
Approx. 34.09
Ω
- 36.72
Ω
/ Insulation resistance > 10M
Ω
Oven lamp
OL
240 - 250V 25W
High voltage capacitor
C
AC 2100V 1.16
μ
F
Magnetron
MG
Filament < 1
Ω
/ Filament - chassis
∞
ohm
High voltage transformer
T
Filament winding < 1
Ω
Secondary winding Approx. 123
Ω
Primary winding Approx. 1.9
Ω
WARNING: DISCONNECT THE PLUG WHEN MEASURING RESISTANCE
Summary of Contents for R-939(BK)
Page 6: ...R939 W 2 2 ...
Page 7: ...R939 W 2 3 ...