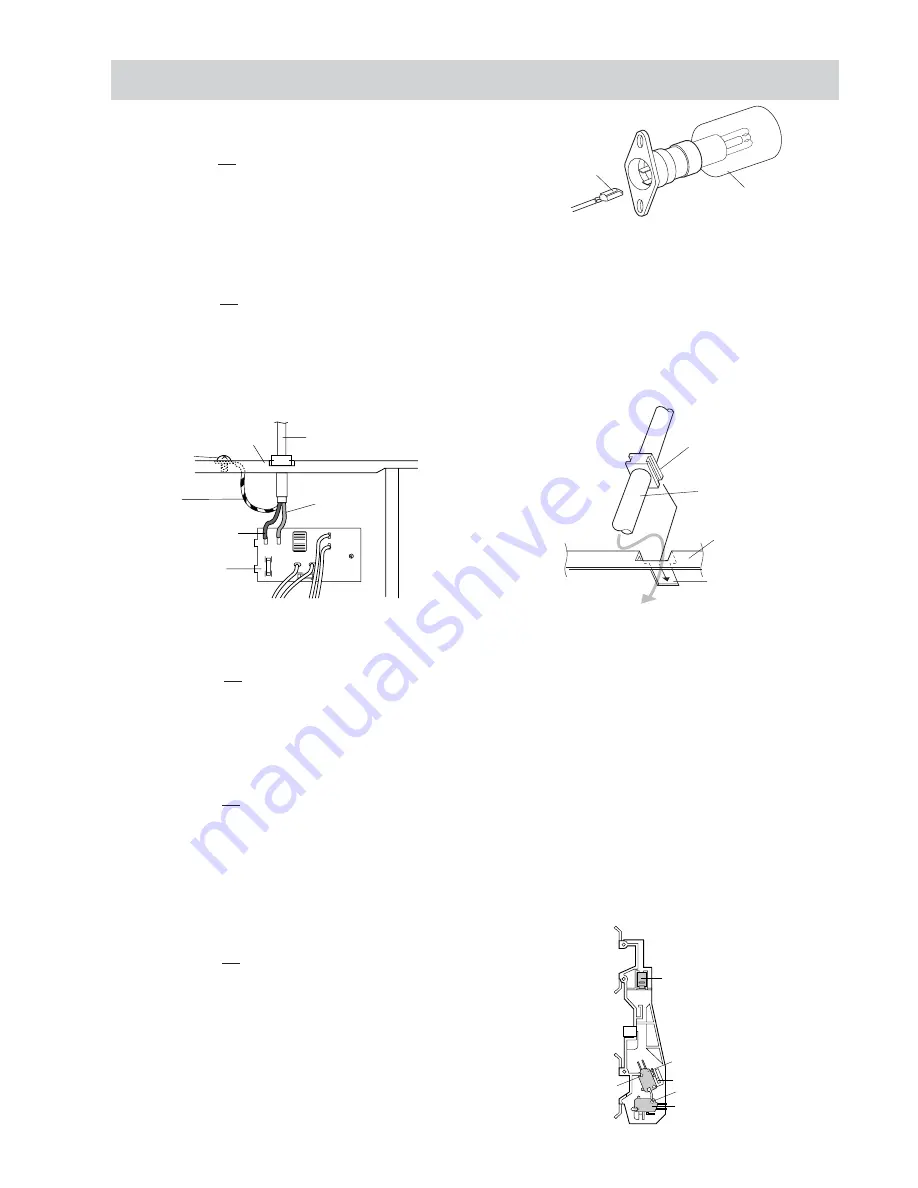
R-895M - 27
Power supply cord
Green/ Yellow
wire
Brown wire
Oven cavity back plate
Blue wire
Noise filter
Screw
L
TP
F 8 A
TL
RED
20 A
WHT
N
POWER
SUPPLY CORD
MOULDING
CORD STOPPER
OVEN CAVITY
BACK PLATE
SQUARE HOLE
1. CARRY OUT 3D CHECKS.
2. Remove the two(2)wires leads as Positive lock
®
connector removal above.
3. Lift up the oven lamp from its retaining clips.
4. Now, the oven lamp is free.
Figure C-3. Oven lamp
Removal
1. CARRY OUT 3D CHECKS.
2. Remove the one (1) screw holding the green/yellow
wire to the cavity back plate.
3. Disconnect the leads of the power supply cord from the
noise filter, referring to the Figure C-4(a).
4. Release the power supply cord from the rear cabinet.
5. Now, the power supply cord is free.
Re-install
1. Insert the moulding cord stopper of power supply cord
into the square hole of the cavity backplate, referring to
the Figure C-4(b).
2. Install the earth wire lead of power supply cord to the
oven cavity with one (1) screw and tight the screw.
3. Connect the brown and blue wire leads of power supply
cord to the noise filter correctly, referring to the Pictorial
Diagram.
POWER SUPPLY CORD REPLACEMENT
OVEN LAMP SOCKET REMOVAL
BULB
LOCK
TOP HEATING ELEMENT REMOVAL
1. CARRY OUT 3D CHECKS.
2. Remove the two (2) screws holding the two (2) termi-
nals of the main wire harness to the top heating
element.
3. Remove the two (2) screws holding the two (2) grill
heater angles to the top of the oven cavity.
4. Remove the two (2) grill heater angles from the oven
cavity.
5. Remove the top heating element from the top of the
oven cavity.
6. Now the top heating element is free.
Figure C-4 (a) Replacement of Power Supply Cord
Figure C-4(b). Power Supply Cord Replacement
BOTTOM HEATING ELEMENT REMOVAL
MONITORED LATCH SWITCH, MONITOR SWITCH AND STOP SWITCH REMOVAL
1. CARRY OUT 3D CHECKS.
2. Remove the control panel assembly referring to "CON-
TROL PANEL ASSEMBLY REMOVAL".
3. Disconnect the leads from all switches.
4. Remove the two (2) screws holding the latch hook to
the oven cavity.
5. Remove the latch hook.
6. Remove the switch(es) from the latch hook by pushing
the retaining tab backwards slightly and turning the
switch(es) on the post.
7. Now the switch(es) is free.
SW2: Stop switch
SW3: Monitor switch
SW1: Monitored
latch switch
Tab
Post
Post
Figure C-5. Switches
COMPONENT REPLACEMENT AND ADJUSTMENT PROCEDURE
1. CARRY OUT 3D CHECKS.
2. Remove the turntable motor cover from the base plate,
referring to "TURNTABLE MOTOR REPLACEMENT".
3. Disconnect the wire leads from the bottom heating
element.
4. Remove the two (2) nuts holding the heater cover and
heater packing to the bottom heater.
5. Remove the heater cover and the heater packing from
the bottom heating element.
6. Re-move the two(2) nuts holding the bottom heating
element to the oven cavity.
7. Remove the bottom heating element from the oven
cavity .