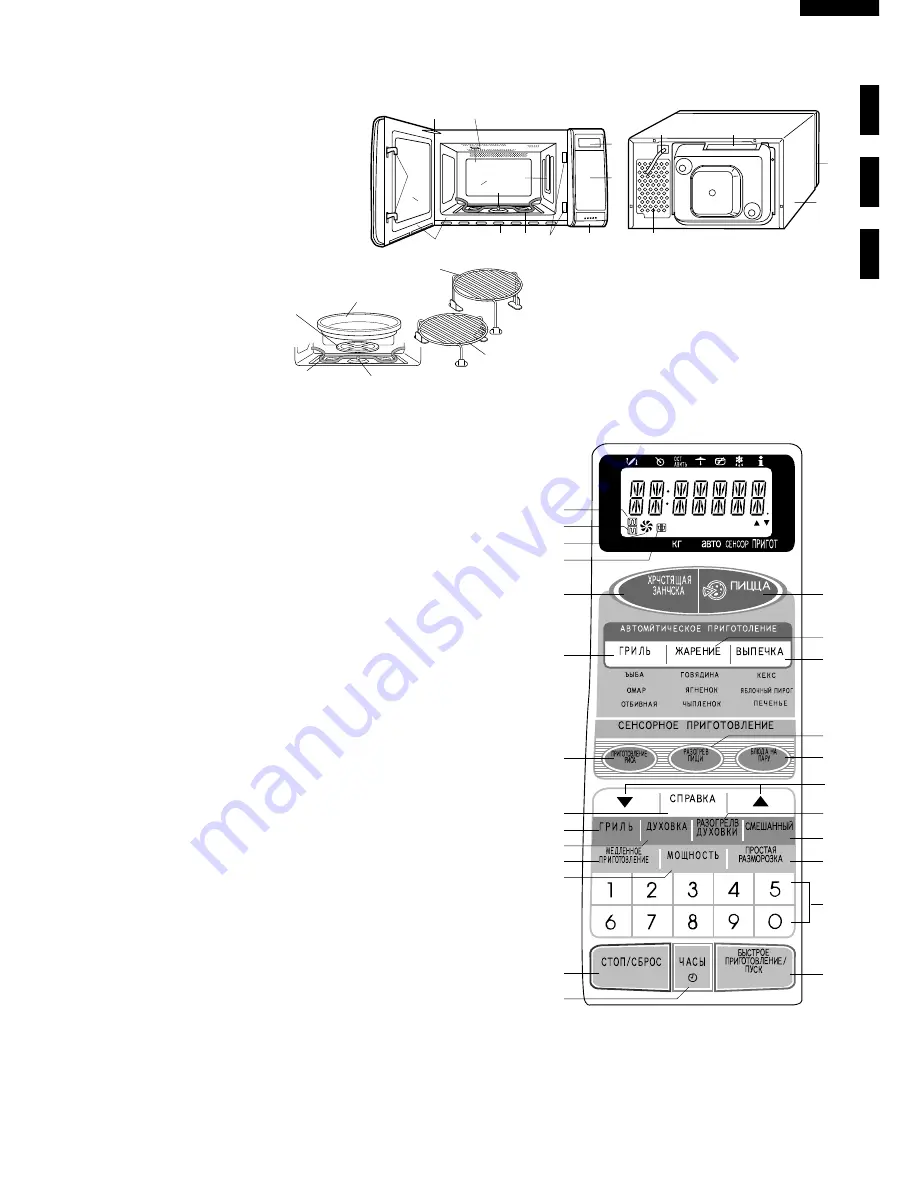
R-870B
3
TOUCH CONTROL PANEL
1
4
u
3
0
0
0
5
5
2
6
w
7
9
8
q
e
r
t
y
Turntable
Turntable
support
High rack
Low rack
Turntable
motor shaft
Bottom
heater
APPEARANCE VIEW
1. TOP HEATER SYMBOL
The symbol will light when the top heater is in use.
2. BOTTOM HEATER SYMBOL
The symbol will light when the bottom heater is in use.
3. CONVECTION SYMBOL
The symbol will light during convection cooking.
4. MICROWAVE SYMBOL
The symbol will light during microwave cooking.
A. CRYSPY SNACK PAD: Press to select 5 popular snack menus.
B. PIZZA PAD: Press to select 3 pizza menus.
C. AUTO GRILL PAD: Press to select 3 popular grill menus.
D. AUTO ROAST PAD: Press to select 3 popular roast menus.
E. AUTO BAKE PAD: Press to select 3 popular baking menus.
F. SENSOR RICE MENU PAD: Press to cook rice, congee or porridge.
G. SENSOR REHEAT DISH PAD: Press to reheat dish.
H. SENSOR STEAM MENU PAD
Press to steam fish, meat or dumpling.
I.
MORE (
'
) / LESS (
"
) pads
Press to adjust the doneness of food in one minute increments during
cooking or to increase/ decrease the time whilst programming the
automatic operations.
J. HELP PAD
Press to select auto start, child lock, language or demonstration modes.
Press to get cooking information.
K. GRILL PAD: Press to select grill cooking.
L. CONVEC PAD
Press to select convection cooking and convection temperature.
M. PREHEAT PAD
Press to preheat the oven prior to cooking.
N. MIX PAD: Press to select mix cooking.
O. SLOW COOK PAD: Press to cook slowly and longer time.
P. POWER LEVEL PAD
Press to select microwave power setting. If not pressed, HIGH power is
automatically selected.
Q. EASY DEFROST PAD
Press to defrost meat by entering weight.
R. NUMBER PADS
Press to enter cooking times, clock time, weight or quantity of food.
S. STOP/CLEAR PAD
Press to clear during programming. Press once to stop operation of oven
during cooking; Press twice to cancel cooking programme.
OVEN
1. Oven lamp
2. Top heaters (Grill heaters)
3. See through door
4. Door hinges
5. Door safety latches
6. Door seals and sealing surfaces
7. Bottom heater
8. Oven cavity
9. Turntable motor shaft
10.Ventilation openings
11.Waveguide cover
12.Door opening button
13.Control panel
14.Digital display
15.Power supply cord
16.Outer cabinet
17.Ventilation slit
NOTE:
1. Ensure that the bottom heater is in the lowest
position as shown the figure, as it is possible
to move it up and down to help with cleaning.
2. Place the turntable support over the turntable
motor shaft on the floor of the cavity.
3. Then place the turntable on to the turntable
support.
T. CLOCK PAD
Press to set clock time.
U. INSTANT COOK/START PAD
Press once to cook for 1 minute at 100% (HIGH
power) or increase by 1 minute multiples each
time this pad is pressed during cooking. Press
to start oven after setting programs.
CRISPY SNACK
PIZZA
AUTO COOK
GRILL
Grilled Fish
RICE MENU
GRILL
SLOW COOK
STOP/ CLEAR
INSTANT COOK/START
POWER LEVEL
EASY DEFROST
CONVEC
PREHEAT
MIX
REHEAT DISH
STEAM MENU
Grilled Lobster
Steak
Beef
Lamb
Chicken
Cake
Apple Pie
Cookies
SENSOR COOK
ROAST
BAKE
HELP
1
2
3
1
2
3
1
2
3
TURNOVER ADD STAND
KG
%
AUTO SENSOR COOK
COVER STIR DEFROST HELP
1
2
3
4
A
C
F
K
J
O
L
P
S
T
B
E
D
H
I
M
G
N
Q
U
R
Summary of Contents for R-870B
Page 2: ...R 870B ...