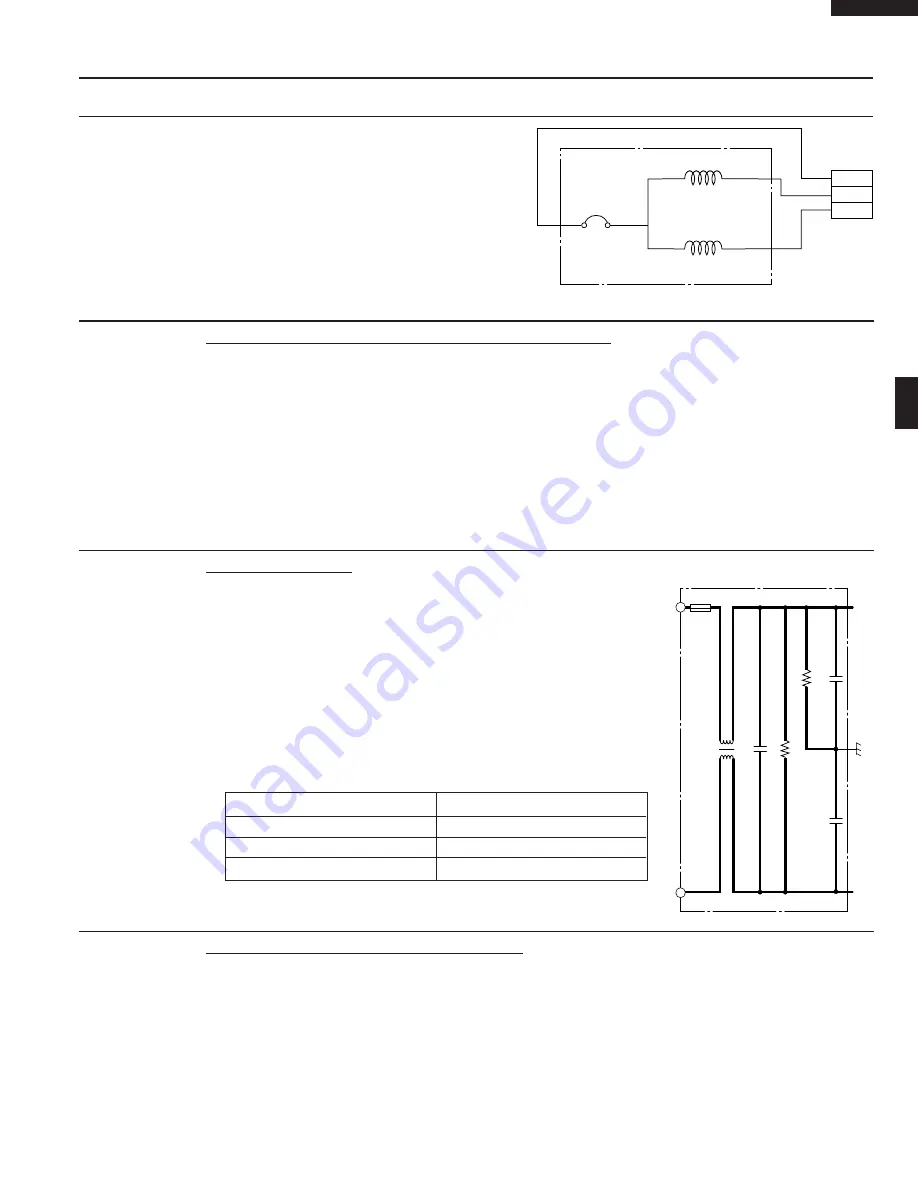
R-8000G
21
TEST PROCEDURES
PROCEDURE
LETTER
COMPONENT TEST
T
TOUCH CONTROL PANEL ASSEMBLY TEST
8. Reconnect all leads removed from components
during testing.
9. Reinstall the outer case (cabinet) and the back
plate.
10. Reconnect the power supply cord after the outer
case and the back plate are installed.
11. Run the oven and check all functions.
The following test procedure should be carried out with the microwave oven is a fully assembled
condition (outer case fitted).
It is difficult to measure the exact temperature in the convection oven. An accurate thermocouple type
temperature tester must be used. A low priced bi-metal type thermometer is not reliable or accurate.
The temperature should be checked with outer case cabinet installed, approx. 5 minutes after preheat
temperature is reached (audible signal sounds four times). The temperature experienced may be approx. 30˚F
more or less than indicated on the display, however, in most cases the food cooking results will be satisfactory.
Difference in power supply voltage will also affect the oven temperature. The Household power supply voltage
may sometimes become lower than the rated voltage (240 V) and cause under-cooking. If the power supply
voltage is 10% lower than the rated voltage, longer cooking time is required by 10% to 20%.
R
CHECKING TEMPERATURE IN THE CONVECTION MODE
The touch control panel consists of circuits including semiconductors such as LSI, ICs, etc. Therefore, unlike
conventional microwave ovens, proper maintenance cannot be performed with only a voltmeter and
ohmmeter.
In this service manual, troubleshooting by unit replacement is described according to the symptoms indicated.
Before testing,
1) Disconnect the power supply cord.
2) Remove the outer case cabinet, referring to "OUTER CASE CABINET REMOVAL".
3) Open the door and block it open.
4) Discharge high voltage capacitor.
5) Disconnect the leads to the primary of the power transformer.
6) Ensure that these leads remain isolated from other components and oven chassis by using insulation tape.
BLU
RED
WHT
Main Coil
3-pin
Connector
Sub Coil
Thermal
Cut-out
130˚C OFF
100˚C ON
100
Ω
110
Ω
JET MOTOR
1. Disconnect the power supply cord.
2. Remove the outer case cabinet, referring to "OUTER CASE CABINET
REMOVAL".
3. Open the door and block it open.
4. Discharge high voltage capacitor.
5. Disconnect the lead wires from the terminal the noise filter. Using an
ohmmeter, check between the terminals as described in the following
table. If incorrect reading are obtained, replace the noise filter.
6. Reconnect all leads removed from components during testing.
7. Reinstall the outer case (cabinet).
8. Reconnect the power supply cord after the outer case is installed.
9. Run the oven and check all functions.
S
NOISE FILTER TEST
MEASURING POINT
INDICATION OF OHMMETER
Between L and L
Approx. 680 k
Ω
Between terminal L and RED
Short circuit.
Between terminal L and GRY
Short circuit.
NOISE SUPRESSION COIL
LINE CROSS CAPACITOR 1.0
µ
F 275V
RESISTO 680k
Ω
1/2W
RESISTO 10M
Ω
1/2W
LINE BYPASS CAPACITOR
0.0033
µ
F 250V
LINE BYPASS CAPACITOR
0.0033
µ
F 250V
MONITOR
FUSE
20A
BLK
WHT
GRY
RED
L
L