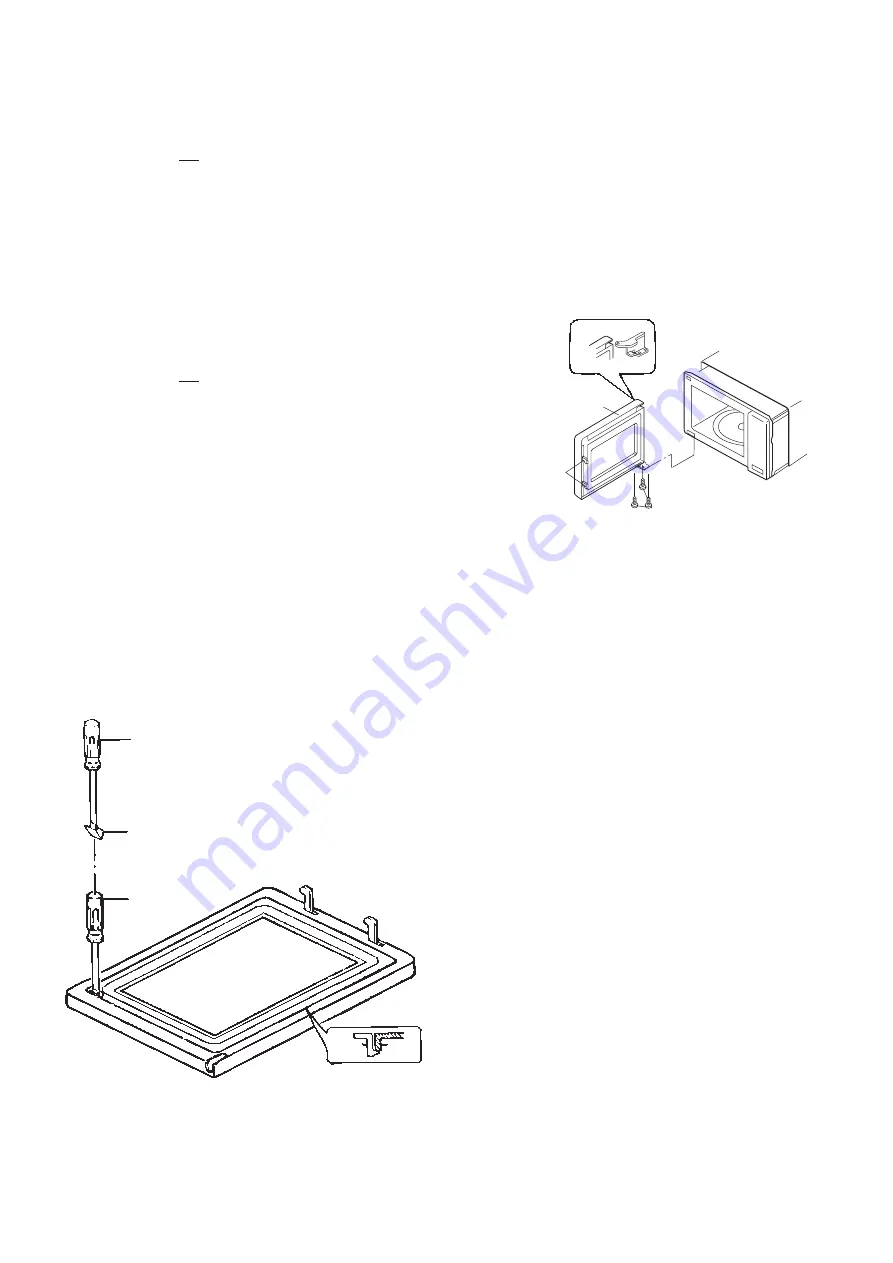
R-7N76(W)M
R-7N76(B)M
33
CHOKE COVER REMOVAL
1. Insert an iron plate (thickness of about 0.5mm) or flat type
screw driver to the gap between the choke cover and door
panel as shown figure to free the engaging part. The
protect sheet may be used not to damage the door panel.
2. Lift up the choke cover, now choke cove is free.
DOOR PARTS REMOVAL
DOOR FRAME AND GLASS REMOVAL
Remove the door assembly, referring to from item 1 through
item 4 of “DOOR REPLACEMENT”.
1. Place the door assembly on a soft cloth with facing up.
2. Remove the choke cover, referring to “CHOKE COVER
REMOVAL”.
3. Remove the four (4) screws holding the door frame to the
door panel assembly.
4. Release the glass stopper from the door frame.
5. Remove the door glass from the door frame.
6. Remove the door frame from the door panel by releasing
the three (3) tabs of door frame from door panel with flat
type screw driver
7. Lift up the door glass, now the door glass is free.
LATCH HEAD REMOVAL
1. Remove the door frame referring to "DOOR FRAME and
GLASS REMOVAL".
2. Release the latch spring from the tabs of the door panel.
3. Release the latch spring from the latch head.
4. Release the latch head from the door panel.
5. Now, the latch head is free.
DOOR REPLACEMENT AND ADJUSTMENT
REPLACEMENT
1. CARRY OUT 3D CHECKS
2. Remove three (3) screws holding the lower oven hinge to
the oven cavity.
3. Remove door assembly with lower oven hinge by pulling
it downward.
4. Separate the door assembly and lower oven hinge. Door
assembly is now free.
5. Re-install lower oven hinge to the new door assembly.
6. On re-installing new door assembly, secure the lower
oven hinge with the three (3) mounting screws to the oven
cavity. Make sure the door is parallel with bottom line of
the oven face plate and the latch head pass through the
latch holes correctly.
7. CARRY OUT 4R CHECKS
Note: After any service to the door, the approved microwave
survey meter should be used to assure in compliance
with proper microwave radiation standards. (Refer to
Microwave Measurement Procedure.)
ADJUSTMENT
When removing and/or loosening hinges such as in door
replacement, the following adjustment criteria are taken.
Door is adjusted to meet the following three conditions by
keeping screws of hinge loose.
1. Adjust door latch heads at a position where they smoothly
catch the latch hook through the latch holes. Refer to
latch switch adjustments.
2. Deviation of the door alignment from horizontal line of
cavity face plate is to be less than 1.0mm.
3. The door is positioned with its face depressed toward the
cavity face plate.
4. Reinstall outer case and check for microwave leakage
around the door with an approved microwave survey
meter. (Refer to Microwave Measurement Procedure.)
Figure C-6. Door Assembly Replacement and Adjustment
Figure C-8. Choke Cover Removal
FLAT TYPE
SCREW-DRIVER
PROTECT BY TAPE
FLAT TYPE
SCREW-DRIVER
CHOKE
COVER
DOOR
PANEL
OUTER CASE
CABINET
DOOR
ASSEMBLY
LATCH
HEADS
SCREWS
RE-INSTALL