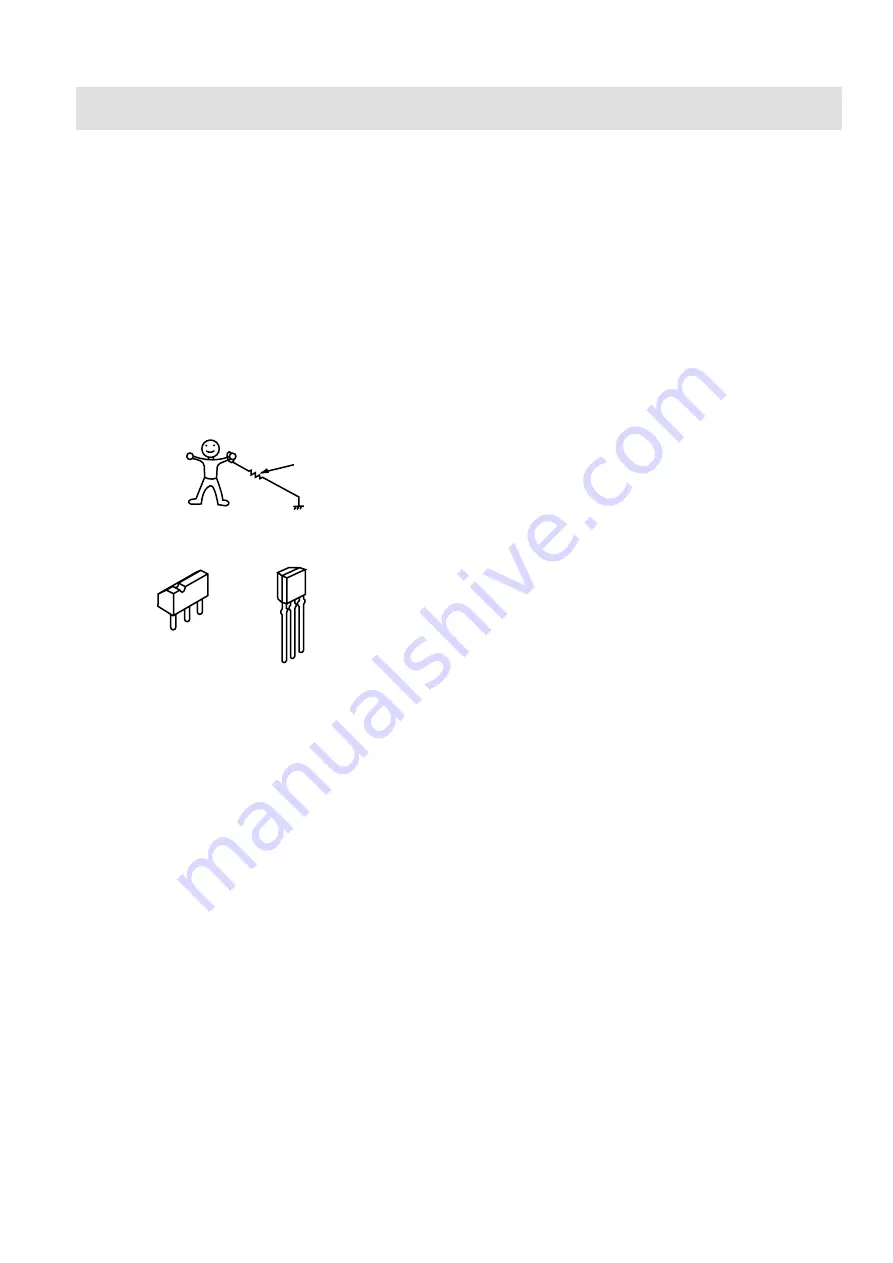
21
R-733 -
TOUCH CONTROL
E
C
B
Transistor
2SB1238
Transistor
DTA123ES
KRA223M
KRC243M
E
C B
1. Precautions for Handling Electronic Components
This unit uses CMOS LSI in the integral part of the
circuits. When handling these parts, the following
precautions should be strictly followed. CMOS LSI have
extremely high impedance at its input and output
terminals. For this reason, it is easily influenced by the
surrounding high voltage power source, static electricity
charge in clothes, etc., and sometimes it is not fully
protected by the built-in protection circuit.
In order to protect CMOS LSI.
1) When storing and transporting, thoroughly wrap them
in aluminium foil. Also wrap PW boards containing
them in aluminium foil.
2) When soldering, ground the technician as shown in
the figure and use grounded soldering iron and work
table.
approx. 1M ohm
2. Shapes of Electronic Components
3. Servicing of Touch Control Panel
We describe the procedures to permit servicing of the
touch control panel of the microwave oven and the
precautions you must take when doing so.
To perform the servicing, power to the touch control
panel is available either from the power line of the oven
itself or from an external power source.
(1) Servicing the touch control panel with power
supply of the oven :
CAUTION:
THE HIGH VOLTAGE TRANSFORMER OF THE
MICROWAVE OVEN IS STILL LIVE DURING SERV-
ICING AND PRESENTS A HAZARD .
Therefore, when checking the performance of the
touch control panel, put the outer cabinet on the oven
to avoid touching the high voltage transformer, or
unplug the primary terminal (connector) of the high
voltage transformer to turn it off; the end of such
connector must be insulated with an insulating tape.
After servicing, be sure to replace the leads to their
original locations.
A. On some models, the power supply cord between
the touch control panel and the oven itself is so
short that the two can't be separated.
For those models, check and repair all the controls
(sensor-related ones included) of the touch control
panel while keeping it connected to the oven.
B. On some models, the power supply cord between
the touch control panel and the oven proper is so
long enough that they may be separated from each
other. For those models, therefore, it is possible to
check and repair the controls of the touch control
panel while keeping it apart from the oven proper;
in this case you must short both ends of the door
sensing switch (on PWB) of the touch control panel
with a jumper, which brings about an operational
state that is equivalent to the oven door being
closed. As for the sensor-related controls of the
touch control panel, checking them is possible if
the dummy resistor(s) with resistance equal to that
of the controls are used.
(2) Servicing the touch control panel with power
supply from an external power source:
Disconnect the touch control panel completely from
the oven proper, and short both ends of the door
sensing switch (on PWB) of the touch control panel,
which brings about an operational state that is
equivalent to the oven door being closed. Connect an
external power source to the power input terminal of
the touch control panel, then it is possible to check and
repair the controls of the touch control panel; it is also
possible to check the sensor-related controls of the
touch control panel by using the dummy resistor(s).
4. Servicing Tools
Tools required to service the touch control panel assembly.
1) Soldering iron: 30W
(It is recommended to use a soldering iron with a
grounding terminal.)
2) Oscilloscope: Single beam, frequency range: DC -
10MHz type or more advanced model.
3) Others: Hand tools
5. Other Precautions
1) Before turning on the power source of the control unit,
remove the aluminium foil applied for preventing static
electricity.
2) Connect the connector of the key unit to the control unit
being sure that the lead wires are not twisted.
3) After aluminium foil is removed, be careful that abnormal
voltage due to static electricity etc. is not applied to the
input or output terminals.
4) Attach connectors, electrolytic capacitors, etc. to PWB,
making sure that all connections are tight.
5) Be sure to use specified components where high
precision is required.