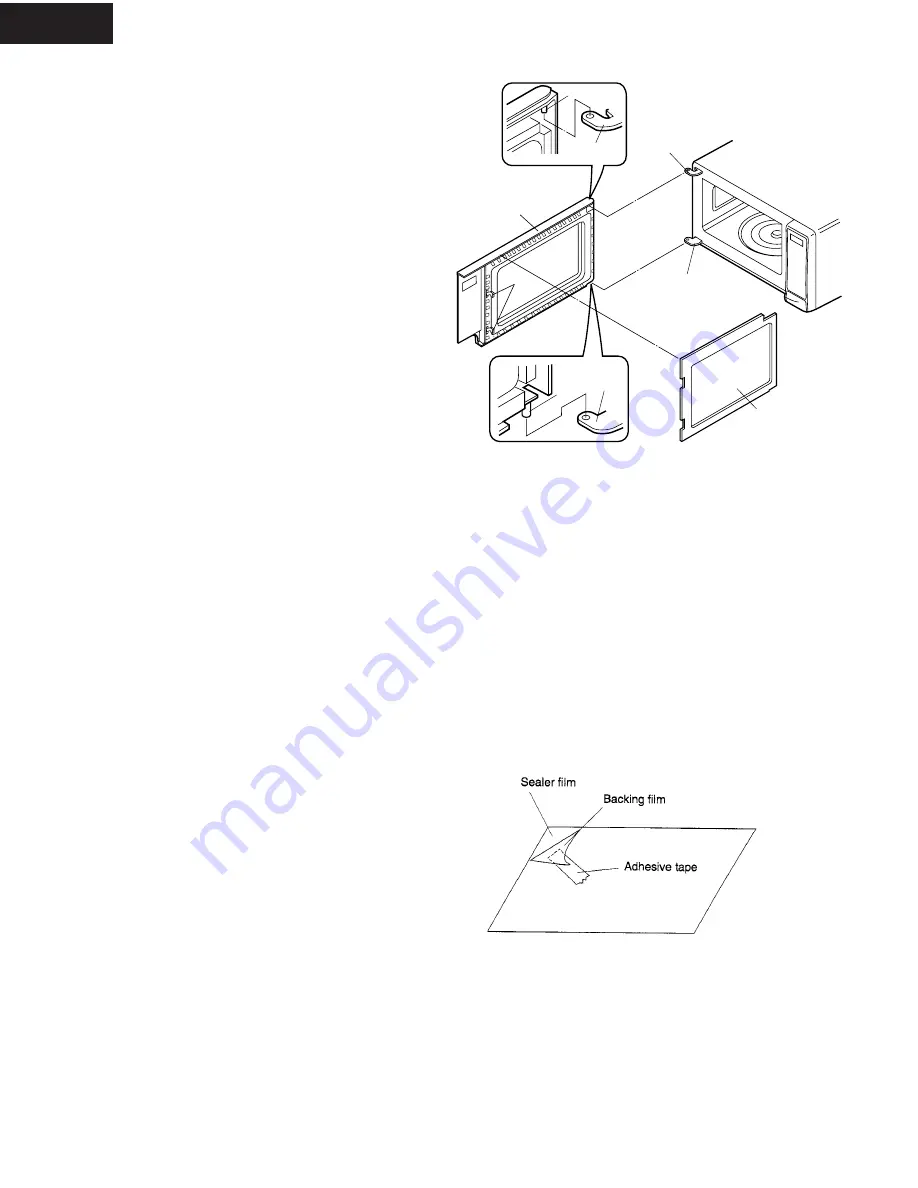
16
R-508HS
9. Release the door panel from twelve (12) tabs of door
frame.
10.Remove the door panel from the door frame.
11.Now, door panel with sealer film is free.
12.Tear sealer film from door panel.
13.Now, door panel is free.
14.Slide latch head upward and remove it from door frame
with releasing latch spring from door frame and latch head.
15.Now, latch head and latch spring are free.
16.Remove door screen from door frame
17.Now, door frame is free.
RE-INSTALL
1. Re-install door screen to door frame.
2. Re-install the latch spring to the latch head. Re-install the
latch spring to the door frame. Re-install latch head to door
frame.
3. Re-install door panel to door frame by fitting twelve (12)
tabs of door frame to twelve (12) holes of door panel.
4. Put sealer film on door panel. Refer to “Sealer Film” about
how to handle new one.
5. Catch two (2) pins of door panel on two (2) hole of upper
and lower oven hinges.
6. Re-install choke cover to door panel by pushing.
Note:
After any service to the door;
(A) Make sure that door sensing switch and primary
interlock switch are operating properly. (Refer to
chapter “Test Procedures”.).
(B) An approved microwave survey meter should be
used to assure compliance with proper microwave
radiation emission limitation standards.
After any service, make sure of the following :
1. Door latch heads smoothly catch latch hook through
latch holes and that latch head goes through center of
latch hole.
2. Deviation of door alignment from horizontal line of cavity
face plate is to be less than 1.0mm.
3. Door is positioned with its face pressed toward cavity face
plate.
4. Check for microwave leakage around door with an approved
microwave survey meter. (Refer to Microwave
Measurement Procedure.)
Note:
The door on a microwave oven is designed to act as
an electronic seal preventing the leakage of microwave
energy from oven cavity during cook cycle. This
function does not require that door be air-tight,
moisture (condensation)-tight or light-tight. Therefore,
occasional appearance of moisture, light or sensing
of gentle warm air movement around oven door is not
abnormal and do not of themselves indicate a leakage
of microwave energy from oven cavity.
SEALER FILM
Installation
1. Put the adhesive tape on the backing film of the sealer
film as shown in Fig. C-6.
2. Tear the backing film by pulling the adhesive tape.
3. Put the pasted side of the sealer film on the door panel
Figure C-6. Sealer film
Note:
When carring out any repair to the door, do not bend or
wrap the slit choke (tabs on the door panel assembly)
to prevent microwave leakage.
Pin
Pin
Upper
Oven Hinge
Upper Oven
Hinge
Lower Oven
Hinge
Lower
Oven Hinge
Choke Cover
Door assembly
Latch
heads