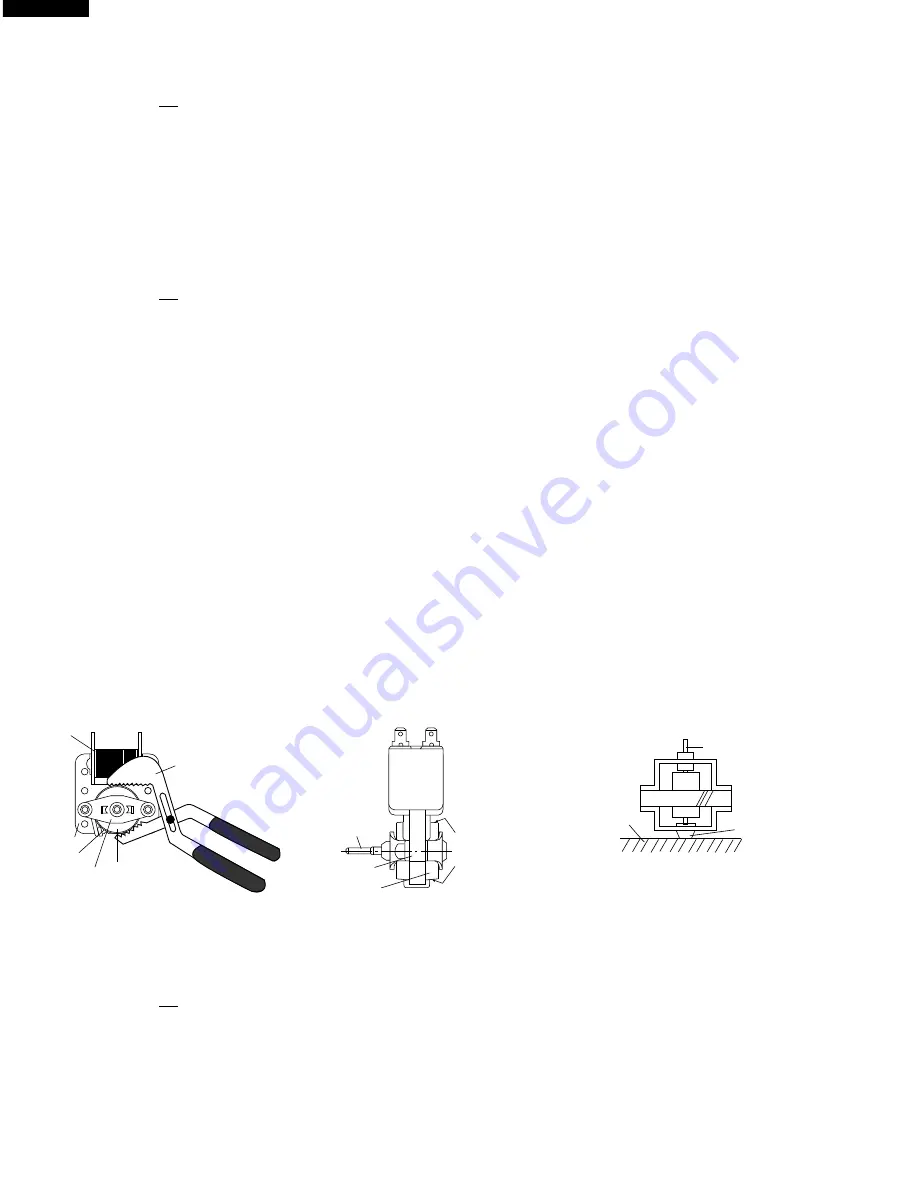
20
R-4A68
CONTROL PANEL ASSEMBLY REMOVAL
1. CARRY OUT 3D CHECKS.
2. Disconnect wire leads from panel components.
3. Release one (1) nail holding the control panel assembly
to the oven flange.
4. Remove control panel assembly and slide upward.
5. Now, the control panel assembly is free.
NOTE: 1. Before attaching a new key unit, wipe off remaining
adhesive on the control panel frame surfaces
completely with a soft cloth soaked in alcohol.
2. When attaching the key unit to the control panel
frame, adjust the upper edge and right edge of
the key unit to the correct position of control panel
frame.
3. Stick the key unit firmly to the control panel frame
by rubbing with soft cloth not to scratch.
COOLING FAN MOTOR REMOVAL
1. CARRY OUT 3D CHECKS.
2. Disconnect the wire leads from the fan motor.
3. Remove the fan duct from the oven cavity.
4. Remove two (2) screws holding the fan motor to the back
plate of the oven cavity.
5. Remove the fan blade from the fan motor shaft according
to the following procedure.
1) Hold the edge of the rotor of the fan motor by using a pair
of grove joint pliers.
CAUTION:
*
Make sure that any pieces do not enter the gap
between the rotor and the stator of the fan motor
because the rotor is easily shaven by pliers and
metal pieces may be produced.
*
Do not touch the pliers to the coil of the fan motor
because the coil may be cut or injured.
*
Do not disfigure the bracket by touching with the
pliers.
2) Remove the fan blade from the shaft of the fan motor by
pulling and rotating the fan blade with your hand.
3) Now, the fan blade will be free.
CAUTION:
*
Do not use this removed fan blade again because the
hole (for shaft) of it may become bigger than a
standard one.
6. Now, the fan motor is free.
INSTALLATION
1. Install the fan blade to the fan motor shaft according to
the following procedure.
1) Hold the center of the bracket which supports the shaft
of the fan motor on the flat table.
2) Apply the screw lock tight into the hole (for shaft) of the
fan blade.
3) Install the fan blade to the shaft of fan motor by pushing
the fan blade with a small, light weight, ball peen hammer
or rubber mallet.
CAUTION:
*
Do not hit the fan blade strongly when installed
because the bracket may be disfigured.
*
Make sure that the fan blade rotates smooth after
installation.
*
Make sure that the axis of the shaft is not slanted.
2. Install the fan motor to the back plate of the oven cavity
with the two (2) screws.
3. Re-install the fan duct to the oven cavity.
4. Connect the wire leads to the fan motor and magnetron,
referring to the pictorial diagram.
Shaft
Table
Center of
bracket
Coil
Gap
Rotor
Bracket
Stator
Groove joint pliers
Shaft
Axis
Stator
These are the position
where should be
pinched with pliers
Rotor
Side View
Rear View
Removal
1. CARRY OUT 3D CHECKS.
2. Remove the one (1) screw holding the green/yellow wire
to the charssis support.
3. Disconnect the brown wire lead of the power supply cord
from the fuse holder.
4. Cut away the connector.
5. Release the power supply cord from the rear cabinet.
6. Now, the power supply cord is free.
Re-install
1. Insert the moulding cord stopper of power supply cord
into the square hole of the rear cabinet.
2. Install the earth wire lead of power supply cord to the
charssis support with one (1) screw and tight the screw.
3. Connect the brown wire lead of power supply cord to the
fuse holder correctly, referring to the Pictorial Diagram.
POWER SUPPLY CORD REPLACEMENT
Summary of Contents for R-4A68
Page 2: ...R 4A68 ...
Page 36: ...34 R 4A68 96SHARP CORP 03U0 07E Printed in Japan ...