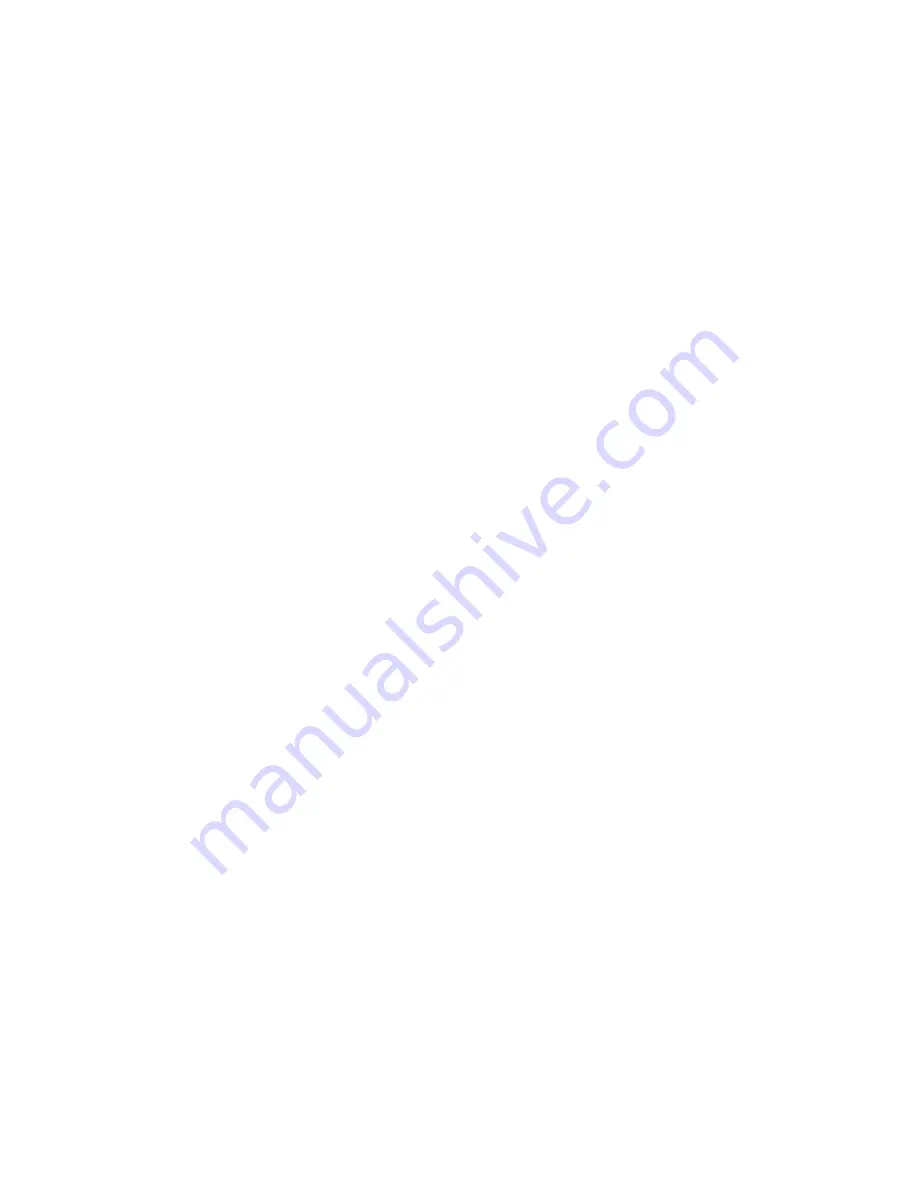
CONTENTS
PRECAUTIONS TO BE OBSERVED BEFORE AND
DURING SERVICING TO AVOID POSSIBLE EXPO-
SURE TO EXCESSIVE MICROWAVE ENERGY
CHAPTER 1. WARNING TO SERVICE PERSONNEL
[1] Before
Servicing .........................................1-1
[2] When the testing is completed, ..................1-1
[3] After
repairing .............................................1-1
CHAPTER 2. MICROWAVE MEASUREMENT PRO-
CEDURE
[1] Requirements: ............................................2-1
[2] Preparation
for
testing: ...............................2-1
[3] Leakage
test: ..............................................2-1
CHAPTER 3. FOREWORD AND WARNING
[1] FOREWORD ..............................................3-1
[2] WARNING ..................................................3-1
[3] DANGER ....................................................3-1
CHAPTER 4. PRODUCT DESCRIPTION
[1] SPECIFICATIONS ......................................4-1
CHAPTER 5. GENERAL INFORMATION
[1] GROUNDING
INSTRUCTIONS .................5-1
[2] OVEN
DIAGRAM........................................5-1
CHAPTER 6. OPERATION
[1] DESCRIPTION OF OPERATING SE-
QUENCE ...................................................6-1
[2] OVEN
SCHEMATIC ...................................6-2
[3] DESCRIPTION AND FUNCTION OF
COMPONENTS..........................................6-3
CHAPTER 7. TROUBLESHOOTING GUIDE
[1] TROUBLESHOOTING
CHART
.................7-1
CHAPTER 8. TEST PROCEDURES
[1] Procedure A: MAGNETRON ASSEMBLY
TEST ..........................................................8-1
[2] Procedure
B:
POWER TRANSFORMER
TEST ..........................................................8-1
[3] Procedure C: HIGH VOLTAGE RECTIFI-
ER TEST ....................................................8-1
[4] Procedure D: HIGH VOLTAGE CAPACI-
TOR TEST ..................................................8-2
[5] Procedure E: TEMPERATURE FUSE OR
THERMAL CUT-OUT TEST .......................8-2
[6] Procedure F: PRIMARY INTERLOCK
SWITCH TEST ...........................................8-2
[7] Procedure F: SECONDARY INTERLOCK
SYSTEM TEST...........................................8-3
[8] Procedure G: MONITOR SWITCH TEST.....8-3
[9] Procedure H: BLOWN MONITOR FUSE
TEST ..........................................................8-4
[10] Procedure I: NOISE FILTER TEST............. 8-4
[11] Procedure J: TOUCH CONTROL PANEL
ASSEMBLY TEST....................................... 8-4
[12] Procedure K: KEY UNIT TEST ................... 8-5
[13] Procedure L: RELAY TEST......................... 8-5
[14] Procedure M: DEFROST TEST.................. 8-6
[15] Procedure N: FOIL PATTERN ON THE
PRINTED WIRING BOARD TEST.............. 8-6
CHAPTER 9. TOUCH CONTROL PANEL ASSEM-
BLY
[1] OUTLINE OF TOUCH CONTROL PANEL
..... 9-1
[2] DESCRIPTION
OF
LSI ............................... 9-1
[3] SERVICING FOR TOUCH CONTROL
PANEL ........................................................ 9-4
CHAPTER 10. PRECAUTIONS FOR USING LEAD-
FREE SOLDER
[1] Employing
lead-free
solder ....................... 10-1
[2] Using lead-free wire solder ....................... 10-1
[3] Soldering................................................... 10-1
CHAPTER 11. COMPONENT REPLACEMENT AND
ADJUSTMENT PROCEDURE
[1] WARNINGS ...............................................11-1
[2] OUTER CASE REMOVAL .........................11-2
[3] POWER
TRANSFORMER
REMOVAL ......11-2
[4] HIGH VOLTAGE RECTIFIER AND HIGH
VOLTAGE CAPACITOR REMOVAL ..........11-2
[5] MAGNETRON
REMOVAL .........................11-2
[6] OVEN LAMP REMOVAL............................11-3
[7] POSITIVE LOCK CONNECTOR (NO-
CASE TYPE) REMOVAL ...........................11-3
[8] CONTROL PANEL ASSEMBLY REMOV-
AL ..............................................................11-3
[9] GRAPHIC SHEET AND MEMBRANE
SWITCH REPLACEMENT.........................11-3
[10] TURNTABLE MOTOR REMOVAL .............11-4
[11] COOLING FAN MOTOR REMOVAL..........11-4
[12] DOOR SENSING SWITCH/PRIMARY IN-
TERLOCK SWITCH AND MONITOR
SWITCH REMOVAL ..................................11-5
[13] DOOR SENSING SWITCH/PRIMARY IN-
TERLOCK SWITCH AND MONITOR
SWITCH ADJUSTMENT ...........................11-5
[14] DOOR REPLACEMENT ............................11-5
CHAPTER 12. CIRCUIT DIAGRAMS
[1] Pictorial
Diagram
(Figure S-1) .................. 12-1
[2] Control Panel Circuit (Figure S-2)............. 12-2
[3] Printed Wiring Board (Figure S-3) ............ 12-3
Parts List