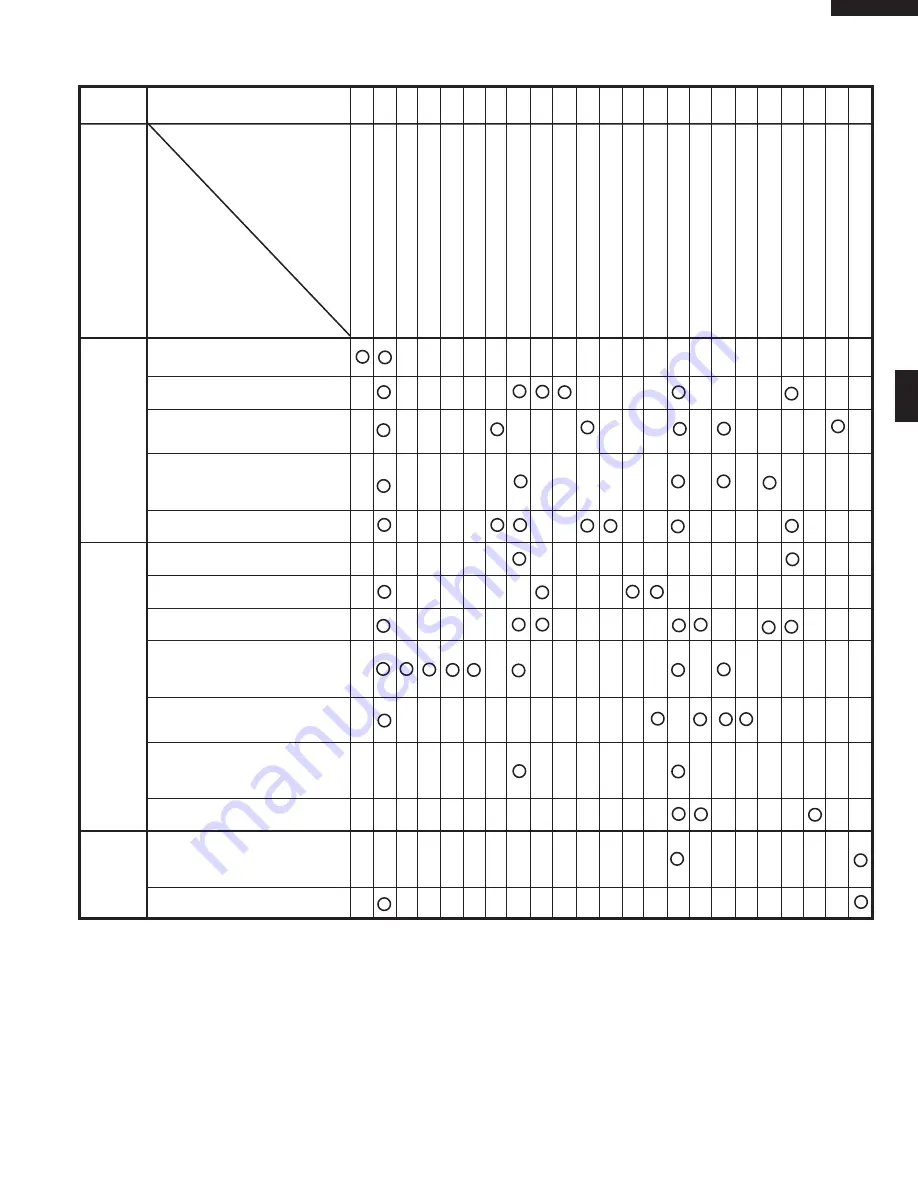
11
R-320HK
R-320HQ
R-320HW
Home fuse or circuit breaker blows
when power cord is plugged into wall
receptacle
C/T fuse blows when power cord is
plugged into wall receptacle.
All letters and indicators do not ap-
pear in display when power cord is
first plugged into wall outlet.
Display does not operate properly
when STOP/CLEAR key is touched.
(Buzzer should sound and ":" or time
of day should appear in display.)
Oven lamp does not light when door
is opened.
Oven lamp does not go out when
door is closed.
Oven lamp lights but fan motor and
turntable motor do not operate.
Oven does not go into cook cycle
when START pad is touched
Oven seems to be operating but little
or no heat is produced in oven load.
(Food incompletely cooked or not
cooked at all at end of cook cycle.)
Oven goes into a cook cycle but
extremely uneven heating is pro-
duced in oven load (food).
Oven does not cook properly when
programmed for Cooking Power P-
50 mode. (Operates properly on
Cooking Power P-HI (HIGH) mode.)
Oven goes into DEFROST CENTER
but food is not defrosted well.
AH sensor does not end during Sen-
sor cooking condition. (Oven does
not shut off after a cup of water is
boiling by sensor cooking.)
Oven stops at 16 sec. after starting.
OFF
CONDITION
PROBLEM
CONDITION
SHORT IN POWER CORD
SHORT OR OPENED WIRING
MAGNETRON
POWER TRANSFORMER
H.V. RECTIFIER ASSEMBLY
HIGH VOLTAGE CAPACITOR
TEMPERATURE FUSE (OVEN)
PRIMARY INTERLOCK SYSTEM
SECONDARY INTERLOCK SWITCH
MONITOR SWITCH
C/T FUSE
OVEN LAMP
COOLING FAN MOTOR
TURNTABLE MOTOR
TOUCH CONTROL PANEL
WRONG OPERATION
LOW VOLTAGE
DIRTY OVEN CAVITY
KEY UNIT (MEMBRANE SWITCH)
RELAY (RY1)
DEFROST CENTER
FOIL PATTERN ON PWB.
AH SENSOR
POSSIBLE CAUSE
AND
DEFECTIVE PARTS
TEST PROCEDURE
RE RE A B C D E F F G H RE RE CK I CK CK CK J
K L M
N
COOKING
CONDITION
CK = Check / RE = Replace
SENSOR
COOKING
CONDITION