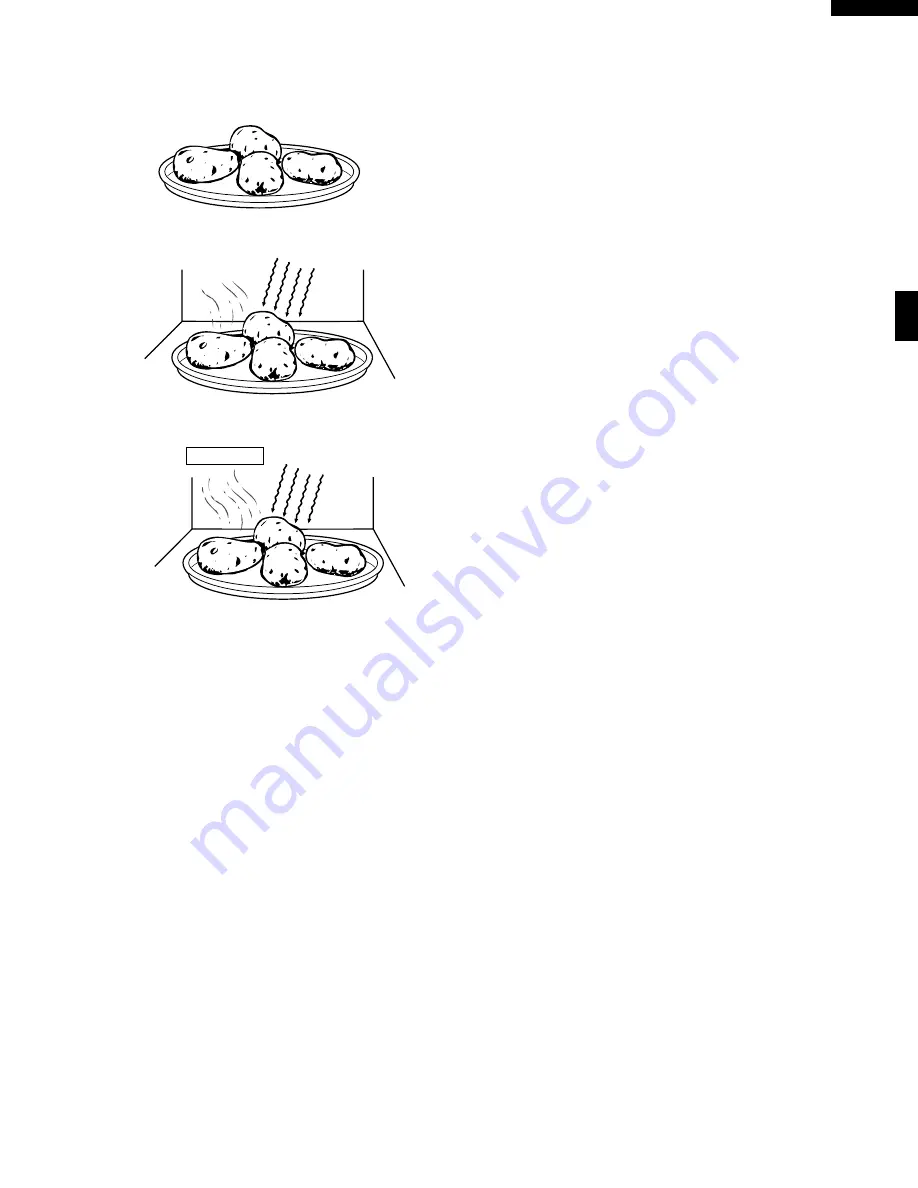
7
R -320FK
R-320FQ
R-320FW
tary cooking is determined by experiment with each food
category and inputted into the LSI.
An example of how sensor works: (POTATOES)
1. Potates at room temperature. Vapor is emitted very
slowly.
2. Heat Potates. Moisture and humidity is emitted rapidly.
You can smell the aroma as it cooks.
3. Sensor detects moisture and humidity and calculates
cooking time and variable power.
Cooking Sequence.
1. Operate the oven in sensor cooking mode by referring to
the operation manual.
NOTE: The oven should not be operated on SENSOR
immediately after plugging in the unit. Wait two
minutes before cooking on SENSOR.
2. The coil of shut-off relay (RY-1) is energized, the turntable
motor, oven lamp and cooling fan motor are turned on,
but the power transformer is not turned on.
3. After about 16 seconds, the cook relay (RY-2) is
energized. The power transformer is turned on,
microwave energy is produced and first stage is started.
The 16 seconds is the cooling time required to remove
any vapor from the oven cavity and sensor.
NOTE: During this first stage, do not open the door or touch
STOP/CLEAR pad.
4. When the sensor detects the vapor emitted from the
food, the display switches over to the remaining cooking
time and the timer counts down to zero.
At this time, the door may be opened to stir, turn, or
season food.
5. When the timer reaches zero, an audible signal sounds.
The shut-off relay and cook relay are de-energized and
the power transformer, oven lamp, etc. are turned off.
6. Opening the door or touching the STOP/CLEAR pad, the
time of day will reappear on the display and the oven will
revert to an OFF condition.
MICROWAVE
MICROWAVE
AH SENSOR