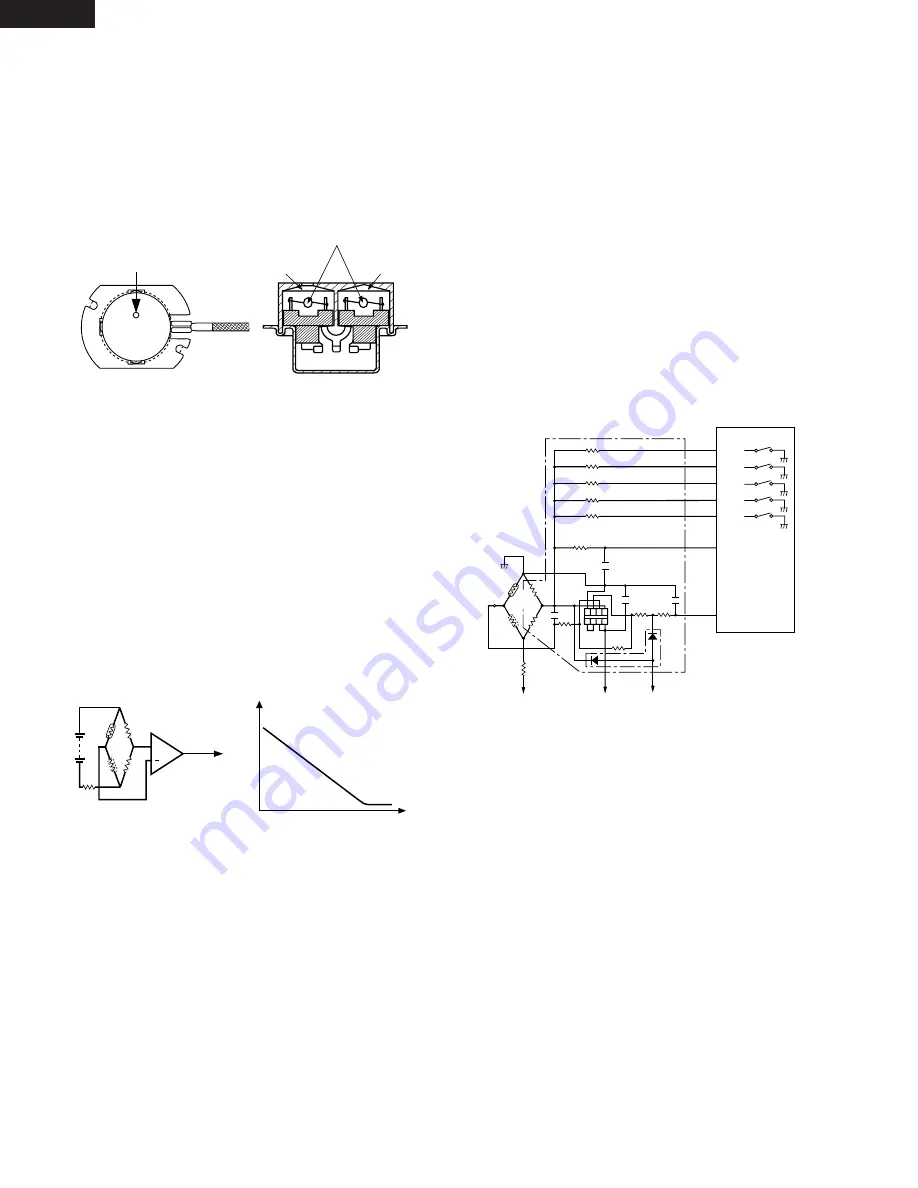
26
R-2110JK
R-2110JW
R-2120JK
R-2120JW
(1) Structure of Humidity Sensor
The humidity sensor includes two thermistors as shown
in the illustration. One thermistor is housed in the closed
vessel filled with dry air while another in the open vessel.
Each sensor is provided with the protective cover made
of metal mesh to be protected from the external airflow.
(2) Operational Principle of Humidity Sensor
The figure below shows the basic structure of a humidity
sensor. A bridge circuit is formed by two thermistors and
two resistors (R1 and R2).
The output of the bridge circuit is to be amplified by the
operational amplifier.
Each thermistor is supplied with a current to keep it
heated at about 150˚C (302˚F), the resultant heat is
dissipated in the air and if the two thermistors are placed
in different humidity conditions they show different
degrees of heat conductivity leading to a potential
difference between them causing an output voltage
from the bridge circuit, the intensity of which is increased
as the absolute humidity of the air increases. Since the
output is very minute, it is amplified by the operational
amplifier.
(3) Detector Circuit of Humidity Sensor Circuit
This detector circuit is used to detect the output voltage
of the humidity circuit to allow the LSI to control sensor
cooking of the unit. When the unit is set in the sensor
cooking mode, 16 seconds clearing cycle occurs than
the detector circuit starts to function and the LSI observes
the initial voltage available at its AN1 terminal.
With this voltage given, the switches SW1 to SW5 in the
LSI are turned on in such a way as to change the
resistance values in parallel with R98 ~ R102. Changing
the resistance values results in that there is the same
potential at both F-3 terminal of the humidity sensor and
AN0 terminal of the LSI. The voltage of AN1 terminal will
indicate about -2.5V. This initial balancing is set up
about 16 seconds after the unit is put in the Sensor
Cooking mode.
HUMIDITY SENSOR CIRCUIT
As the sensor cooking proceeds, the food is heated to
generate moisture by which the resistance balance of
the bridge circuit is deviated to increase the voltage
available at AN1 terminal of the LSI.
Then the LSI observes that voltage at AN1 terminal and
compares it with its initial value, and when the comparison
rate reaches the preset value (fixed for each menu to be
cooked), the LSI causes the unit to stop sensor cooking;
thereafter, the unit goes in the next operation
automatically.
When the LSI starts to detect the initial voltage at AN1
terminal 16 seconds after the unit has been put in the
Sensor Cooking mode, if it is not possible to balance the
bridge circuit due to disconnection of the humidity
sensor, ERROR will appear on the display and the
cooking is stopped.
1) Humidity sensor circuit
ventilation opening for sensing
Sensing part
(Open vessel)
Sensing part
(Closed vessel)
Thermistors
C
S
R3
R1
R2
+
Operational
amplifier
Output
voltage
S : Thermistor
open vessel
C : Thermistor
closed vessel
2
Absolute humidity (g/m )
Output voltage
Absolute humidity vs,
output voltage characteristic
SW1
SW2
SW3
SW4
SW5
P50
P51
P52
P53
P54
LSI
(IC1)
AN0
AN1
620k
300k
150k
75k
37.4k
18
15
14
10
9
16
17
47k
47k
15k
1 2 3 4
8 7 6 5
0.01uF
0.1uF
0.01uF
VA : -15V
VA : -15V
R90
C90
C91
C93
C92
S
F-2
1.8k
IC2
F-1
F-3
C
3.57k
3.32k
VC : -5V
0.1 uF
C. Thermistor in
closed vessel
S. Thermistor in
open vessel
R98
R99
R96
R91
360k
R93
R92
R94
R95
D90
R100
R101
R102
R97