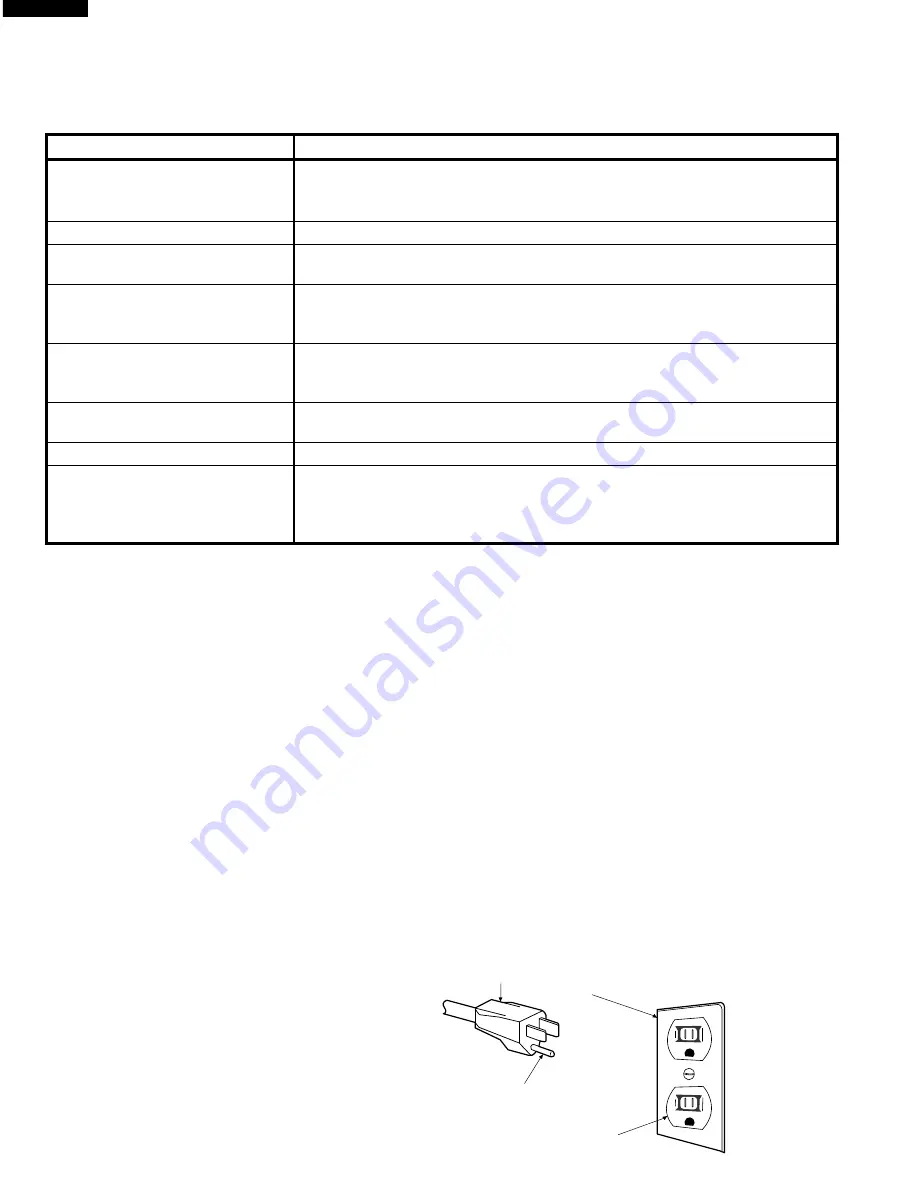
4
R-200BK
R-200BW
3-Pronged Plug
Grounded
Receptacle Box
Grounding Pin
3-Pronged Receptacle
GENERAL INFORMATION
GROUNDING INSTRUCTIONS
This oven is equipped with a three prong grounding plug. It must be plugged into a wall receptacle that is properly installed
and grounded in accordance with the National Electrical Code and local codes and ordinances.
In the event of an electrical short circuit, grounding reduces the risk of electric shock by providing an escape wire for the
electric current.
WARNING: Improper use of the grounding plug can result in a risk of electric shock.
Electrical Requirements
The electrical requirements are a 115 -120 volt 60 Hz, AC only,
15 or 20 amp. fused electrical supply. It is recommended that a separate circuit serving only this appliance be provided. When
installing this appliance, observe all applicable codes and ordinances.
A short power-supply cord is provided to reduce risks of becoming entangled in or tripping over a longer cord.
Where a two-pronged wall-receptacle is encountered, it is the personal responsibility and obligation of the customer to
contact a qualified electrician and have it replaced with a properly grounded three-pronged wall receptacle or have a
grounding adapter properly grounded and polarized. If the extension cord must be used, it should be a 3-wire, 15 amp. or
higher rated cord. Do not drape over a countertop or table where it can be pulled on by children or tripped over accidentally.
CAUTION: DO NOT UNDER ANY CIRCUMSTANCES CUT OR REMOVE THE ROUND GROUNDING PRONG FROM
THIS PLUG.
ITEM
DESCRIPTION
Power Requirements
120 Volts
60 Hertz
Single phase, 3 wire grounded
Power Consumption
1030W / Approx. 9.0 Amperes
Power Output
600 W nominal of RF microwave energy (IEC 705 Test procedure)
Operating frequency 2450 MHz
Case Dimensions
Width 18-1/8"
Height 11-3/8"
Depth 14-5/8"
Cooking Cavity Dimensions
Width 12-3/8"
(0.7 Cubic feet)
Height 7-7/8"
Depth 12-5/8"
Control Complement
Light up dial timer (15 minutes)
No cooking control
Oven Cavity Light
Yes
Safety Standard
UL Listed.
FCC Authorized
DHHS RUles, CFR, Title 21, Chapter 1, Subchapter J
PRODUCT DESCRIPTION
SPECIFICATIONS