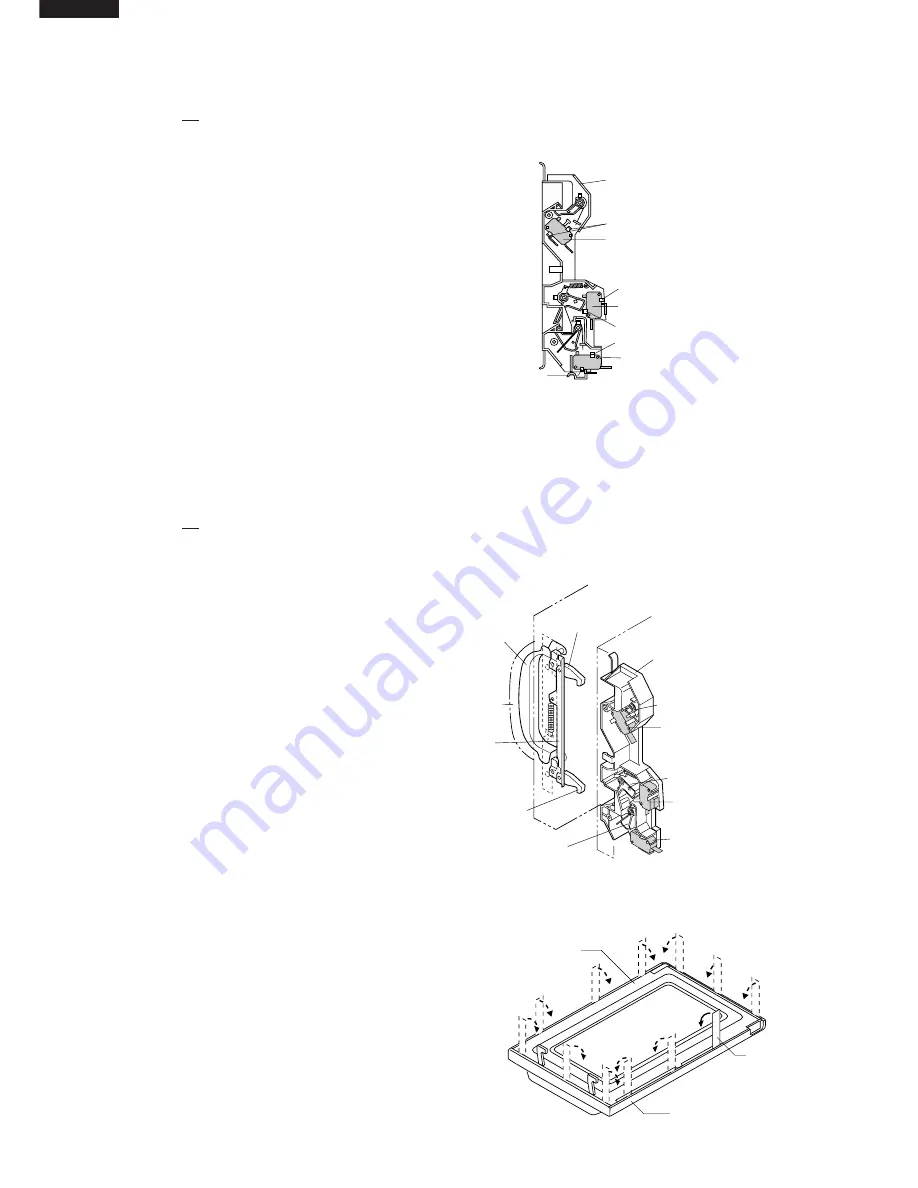
26
R-15AT
1. CARRY OUT 3D CHECKS.
2. Remove the control panel assembly referring to "CON-
TROL PANEL ASSEMBLY REMOVAL".
3. Disconnect the leads from all switches.
4. Remove the two (2) screws holding the latch hook to the
oven cavity.
5. Remove the latch hook.
6. Push the retaining tab outward slightly and remove the
switch.
Reinstall
1. Reinstall each switch in its place. The primary interlock
relay control switch is in the lower position and the 2nd.
interlock switch is in the upper position. The monitor
switch is in the middle position.
2. Reconnect wire leads to each switch.
Refer to pictorial diagram.
3. Secure latch hook (with two (2) mounting screws) to oven
flange.
PRIMARY INTERLOCK RELAY CONTROL SWITCH, 2ND. INTERLOCK SWITCH AND
MONITOR SWITCH REMOVAL
Figure C-4. Switches
DOOR PARTS REPLACEMENT
If the primary interlock relay control switch, 2nd. interlock
switch and monitor switch do not operate properly due to a
mis-adjustment, the following adjustment should be made.
1. CARRY OUT 3D CHECKS.
2. Loosen the two (2) screws holding the latch hook to the
oven cavity front flange.
3. With door closed, adjust latch hook by moving it back and
forth, and up and down. In and out play of the door allowed
by the upper and lower position of the latch hook should
be less than 0.5mm. The vertical position of the latch hook
should be adjusted so that the primary interlock relay
control switch and 2nd. interlock switch are activated with
the door closed. The horizontal position of the latch hook
should be adjusted so that the plunger of the monitor
switch is pressed with the door closed.
4. Secure the screws with washers firmly.
5. Check the operation of all switches. If each switch has not
activated with the door closed, loosen screw and adjust
the latch hook position.
After adjustment, check the following.
1. In and out play of door remains less than 0.5mm when in the
latched position. First check upper position of latch hook,
pushing and pulling upper portion of door toward the oven
face. Then check lower portion of the latch hook, pushing
and pulling lower portion of the door toward the oven face.
Both results (play in the door) should be less than 0.5mm.
PRIMARY INTERLOCK RELAY CONTROL SWITCH, 2ND. INTERLOCK SWITCH AND
MONITOR SWITCH ADJUSTMENT
2. The 1st. interlock switch, latch switch and 2nd. interlock
relay control switch interrupt the circuit before the door
can be opened.
3. Monitor switch contacts close when door is opened.
4. Reinstall outer case and check for microwave leakage
around door with an approved microwave survey meter.
(Refer to Microwave Measurement Procedure.)
Figure C-5. Latch Switch Adjustments
Putty Knife
Door Frame
Choke Cover
Latch Hook
Tabs
Tab
Tab
Tab
Tab
SW3: Monitor Switch
SW2:
2nd. Interlock Switch
SW1: Primary Interlock Relay
Control Switch
Latch Hook
Latch Switch
Lever A
Latch Switch
Lever B
Latch Switch
Lever C
Latch Head
Latch Head
Handle
Lever
Door
Handle
Latch
Lever
SW2: 2nd. Interlock Switch
SW3: Monitor Switch
SW1:
Primary Interlock Relay
Control Switch
4. Make sure that the monitor switch is operating properly
and check continuity of the monitor circuit. Refer to
chapter "Test Procedure" and Adjustment procedure.
CHOKE COVER
1. Disconnect the oven from the power supply.
2. Open the oven door and wedge it open.
3. Insert a putty knife (thickness of about 0.5mm) into the gap
between the choke cover and door frame as shown in
Figure C-6 to free engaging parts.
4. Pry the choke cover by inserting a putty knife as shown in
Figure C-6.
5. Release choke cover from door panel.
6. Now choke cover is free.
NOTE: When carrying out any repair to the door, do not
bend or warp the slit choke (tabs on the door
panel assembly) to prevent microwave leakage.
Figure C-6. Door Disassembly