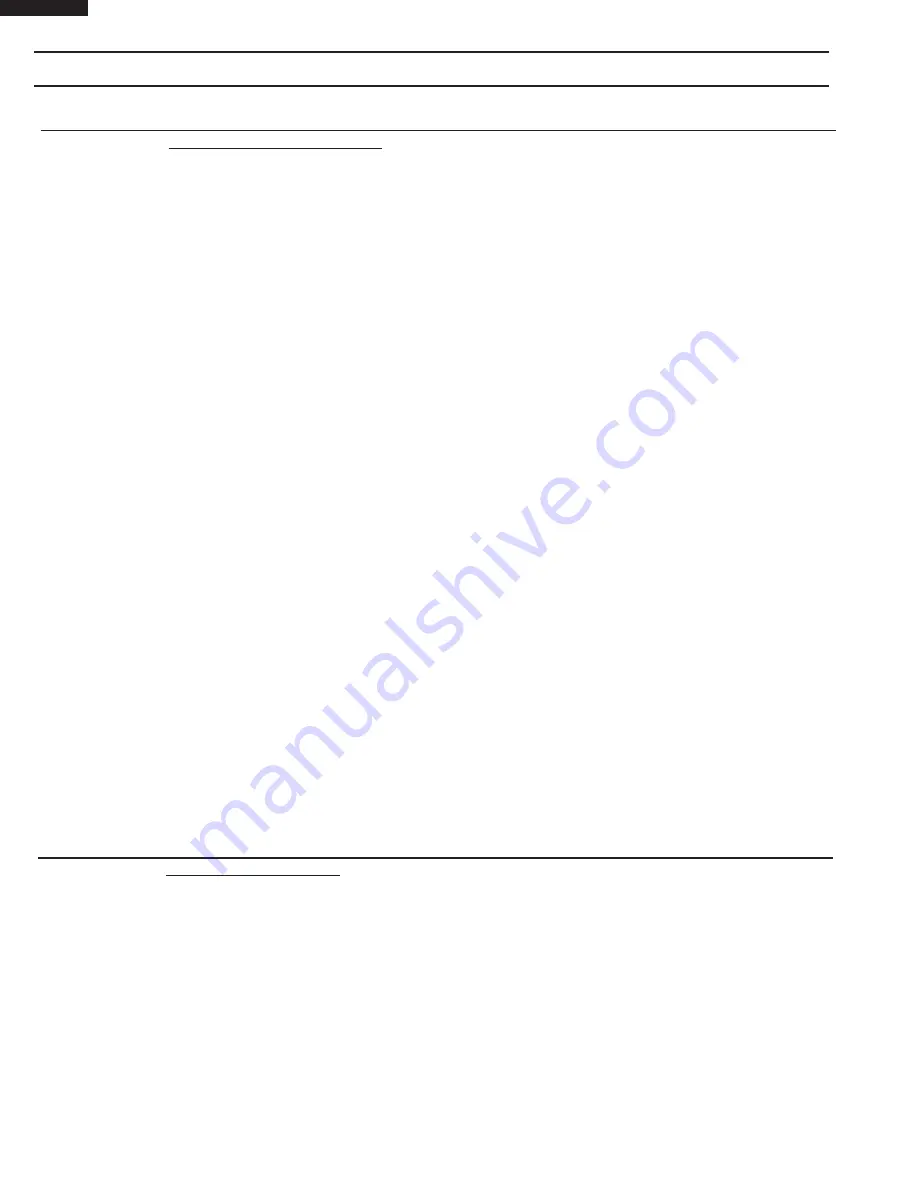
6
KB-6524PS
KB-6524PK
KB-6524PW
2. Open the drawer and keep it open.
3. To discharge high voltage capacitor, wait for 60 seconds.
4. To test for an open filament, isolate the magnetron from the high voltage circuit. A continuity check across
the magnetron filament leads should indicate less than ohm.
5. To test for a shorted magnetron, connect the ohmmeter leads between the magnetron filament leads
and chassis ground. This test should indicate an infinite resistance. If there is little or no resistance the
magnetron is grounded and must be replaced.
6. Reconnect all leads removed from components during testing.
7. Reassemble the unit.
8. Reconnect the power supply cord.
9. Run the oven and check all functions.
MICROWAVE OUTPUT POWER
The following test procedure should be carried out with the microwave oven in a fully assembled condition.
HIGH VOLTAGES ARE PRESENT DURING THE COOK CYCLE, SO EXTREME CAUTION SHOULD BE
OBSERVED.
Power output of the magnetron can be measured by performing a water temperature rise test. This test
should only be used if above tests do not indicate a faulty magnetron and there is no defect in the following
components or wiring: This test will require a 6 ounce (453cc) measuring cup and an accurate mercury
thermometer or thermocouple type temperature tester. For accurate results, the following procedure must
be followed carefully:
. Fill the measuring cup with 6 oz. (453cc) of tap water and measure the temperature of the water with
a thermometer or thermocouple temperature tester. Stir the thermometer or thermocouple through the
water until the temperature stabilizes. Record the temperature of the water.
2. Place the cup of water in the oven. Operate oven at POWER 0(HIGH) selecting more than 60 seconds
cook time. Allow the water to heat for 60 seconds, measuring with a stop watch, second hand of a watch
or the digital read-out countdown.
3. Remove the cup from the oven and again measure the temperature, making sure to stir the thermometer
or thermocouple through the water until the maximum temperature is recorded.
4. Subtract the cold water temperature from the hot water temperature. The normal result should be 28
ο
to
54
ο
F (6
ο
to 30
ο
C) rise in temperature. If the water temperatures are accurately measured and tested
for the required time period the test results will indicate if the magnetron tube has low power output (low
rise in water temperature) which would extend cooking time or high power output (high rise in water
temperature) which would reduce cooking time. Because cooking time can be adjusted to compensate
for power output, the magnetron tube assembly should be replaced only if the water temperature rise
test indicates a power output well beyond the normal limits. The test is only accurate if the power supply
line voltage is 20 volts and the oven cavity is clean.
G
MAGNETRON ASSEMBLY TEST
. Disconnect the power supply cord.
2.
Open the drawer and keep it open.
3. To discharge high voltage capacitor, wait for 60 seconds.
4. A continuity check across the thermal cut-out terminals should indicate a closed circuit unless the
temperature of the thermal cut-out reaches approximately 293
ο
F(45
ο
C).
An open thermal cut-out indicates overheating of the oven, exchange the oven thermal cut-out and
check inside of oven cavity and for improper setting of cooking time or operation of control unit.
Check for restricted air flow through the vent holes of the oven cavity, especially the cooling fan and
air guide.
5. Reconnect all leads removed from components during testing.
6.
Reassemble the unit.
7. Reconnect the power supply cord.
8. Run the unit and check all functions.
CAUTION: IF THE THERMAL CUT-OUT INDICATES AN OPEN CIRCUIT AT ROOM TEMPERATURE,
REPLACE THERMAL CUT-OUT.
H
THERMAL CUT-OUT TEST
. Disconnect the power supply cord.
Refer to the disassembly instructions found on Page 22.
TEST PROCEDURES
PROCEDURE
LETTER
COMPONENT TEST