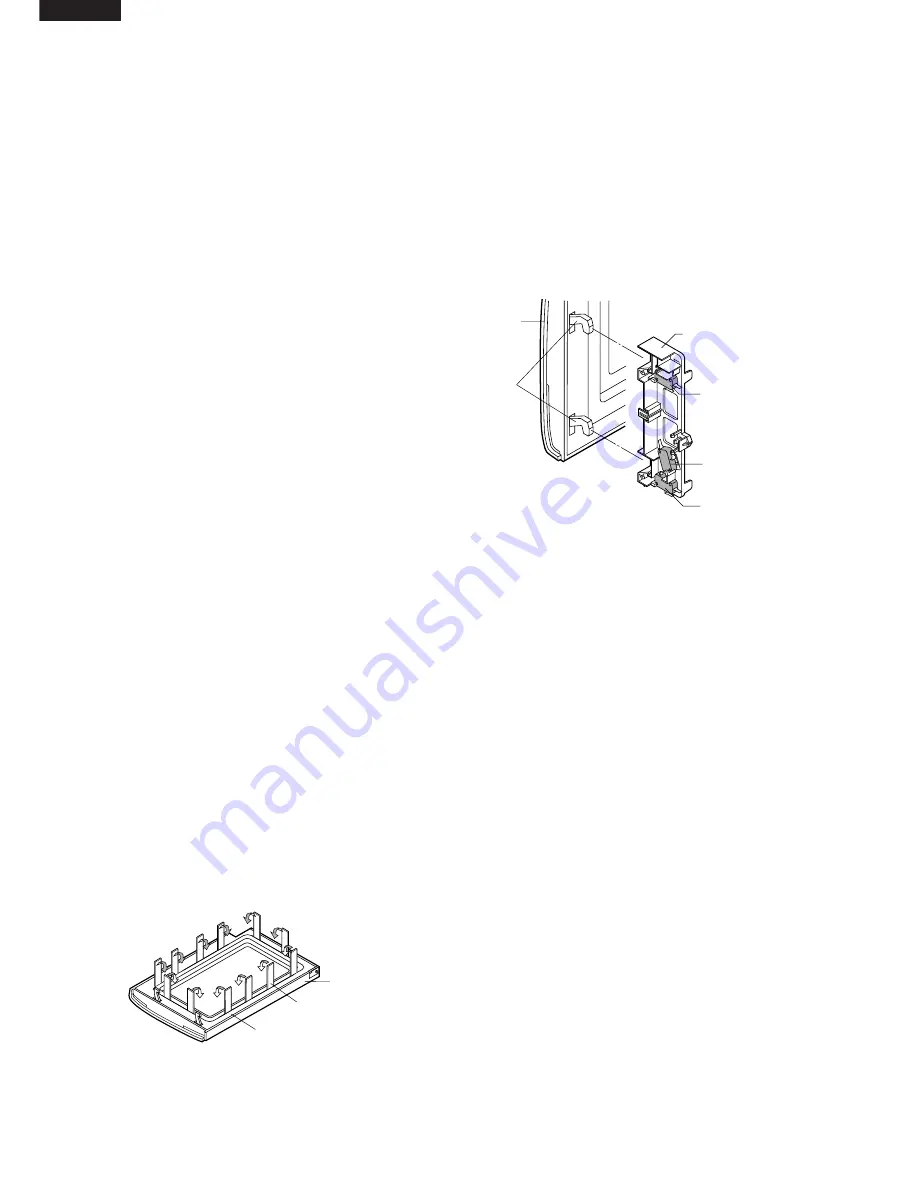
R-350F
22
Choke Cover
Door Frame
Putty Knife
Latch Hook
2nd. Interlock
Reley Control
Switch
Latch
Heads
Door
Monitor Switch
1st. Latch
Switch
1ST. LATCH SWITCH, 2ND. INTERLOCK RELAY CONTROL SWITCH AND MONITOR
SWITCH ADJUSTMENT
If the 1st. latch switch, 2nd. latch switch, stop switch and
monitor switch do not operate properly due to a
misadjustment, the following adjustment should be made.
1. Loosen the two (2) screws holding latch hook to the
oven cavity front flange.
2. With door closed, adjust latch hook by moving it back
and forth, and up and down. In and out play of the door
allowed by the upper and lower position of the latch
hook should be less than 0.5mm. The vertical position
of the latch hook should be adjusted so that the 1st.
latch switch and stop switch are activated with the door
closed. The horizontal position of the latch hook should
be adjusted so that the plunger of the monitor switch
and 2nd. latch switch are pressed with the door closed.
3. Secure the screws with washers firmly.
4. Check all switches operation. If each switch has not
activated with the door closed, loosen screw and adjust
the latch hook position.
After adjustment, check the following.
1. In and out play of door remains less than 0.5mm when
in the latched position. First check upper position of
latch hook, pushing and pulling upper portion of door
toward the oven face. Then check lower portion of the
latch hook, pushing and pulling lower portion of the
door toward the oven face. Both results (play in the
door) should be less than 0.5mm.
2. The contacts of the 1st. latch switch and stop switch
open within 0.9mm gap between right side of cavity
face plate and door when the door is open.
3. Monitor switch contacts close when door is opened.
4. The 2nd. latch switch contacts open when the door is
opened.
5. Re-install outer case and check for microwave leakage
around door with an approved microwave survey meter.
(Refer to Microwave Measurement Procedure.)
Figure C-5. Latch Switch Adjustments
REMOVAL
1. Disconnect the power supply cord.
2. Open button and open the door slightly.
3. Insert a putty knife (thickness of about 0.5mm) into the
gap between the choke cover and door frame as shown
in Figure C-6 to free engaging parts.
4. Pry the choke cover by inserting a putty knife as shown
Figure C-6.
5. Release choke cover from door panel.
6. Now choke cover is free.
7. Release two (2) pins of door panel from two (2) holes
of upper and lower oven hinges by lifting up.
8. Now, door panel with door frame is free from oven
cavity.
NOTE: When carrying out any repair to the door, do
not bend or warp the slit choke (tabs on the
door panel assembly) to prevent microwave
leakage.
Figure C-6. Door Disassembly
9. Remove the four (4) screws holding the door panel to
the door frame.
DOOR REPLACEMENT
10.Release door panel from eight (8) tabs of door frame.
11.Now, door panel with sealer film is free.
12.Tear sealer film from door panel.
13.Now, door panel is free.
14.Slide latch head upward and remove it from door frame
with releasing latch spring from door frame and latch
head.
15.Now, latch head and latch spring are free.
16.Remove the door screen from the door frame.
17.Now, door screen is free.
RE-INSTALL
1. Re-install door screen to door frame.
2. Re-install the latch spring to the latch head. Re-install
the latch spring to the door frame. Re-install latch head
to door frame.
3. Re-install door panel to door frame by fitting eight (8)
tabs of door frame to eight (8) holes of door panel.
4. Hold the door panel to the door frame with the four (4)
screws.
5. Put sealer film on door panel. Refer to “Sealer Film”
about how to handle new one.
6. Catch two (2) pins of door panel on two (2) hole of upper
and lower oven hinges.
7. Re-install choke cover to door panel by pushing.
Note: After any service to the door;
(A) Make sure that 1st. latch switch, 2nd. interlock
relay control switch and monitor switch are
operating properly. (Refer to chapter “Test
Procedures”.).
(B) An approved microwave survey meter should be
used to assure compliance with proper microwave
Summary of Contents for Carousel R-350F
Page 2: ...R 350F 36 ...