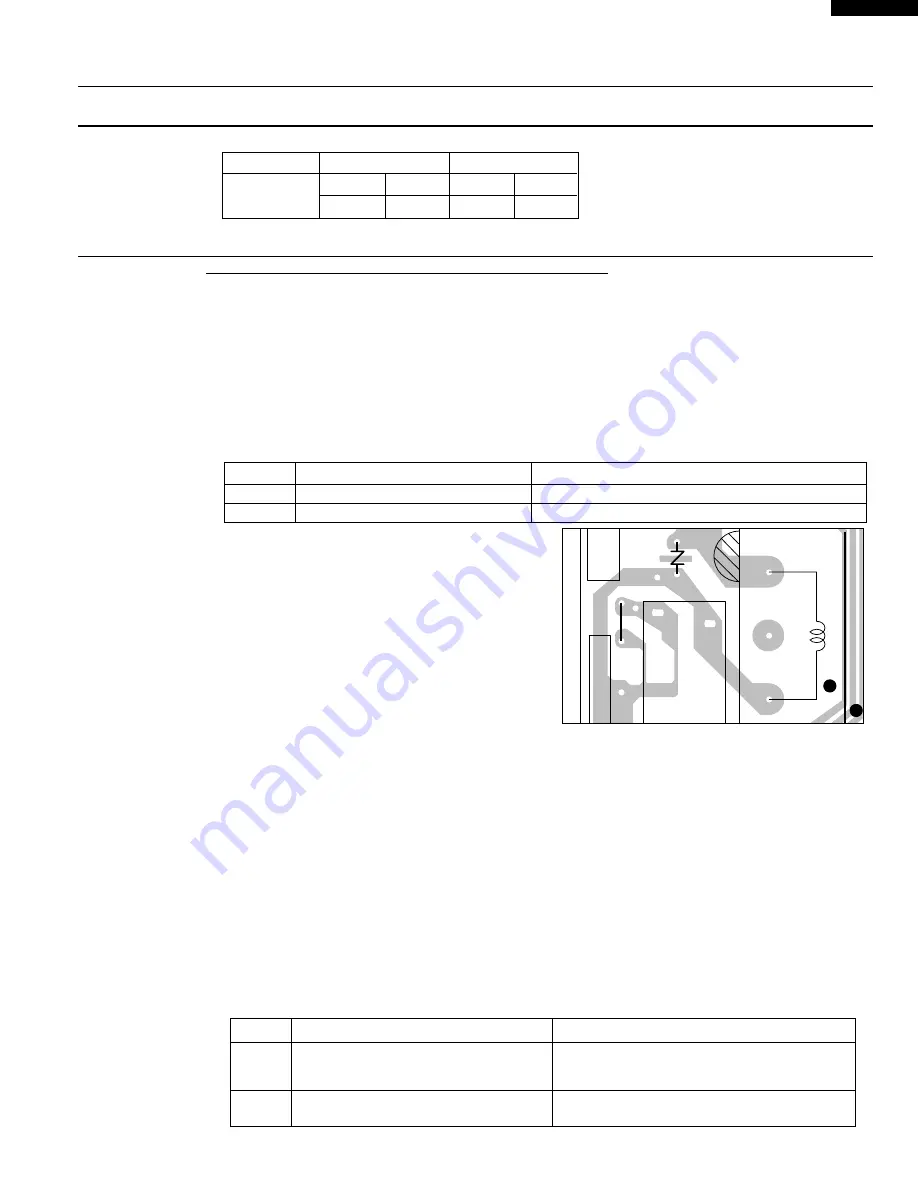
11
R-1512
R-1511
TEST PROCEDURES
PROCEDURE
LETTER
COMPONENT TEST
(8) The oven will operate as follows.
Menu
1ST STAGE
2ND STAGE
Steaks/Chops
LEVEL
TIME
LEVEL
TIME
0.5lbs
60%
57sec.
40%
17sec.
(9) If improper operation is indicated, the control unit is probably defective and should be checked.
To protect the electronic circuits, this model is provided with a fine foil pattern added to the primary on
the PWB, this foil pattern acts as a fuse.
1. Foil pattern check and repairs.
1) Disconnect the power supply cord.
2) Open the door and block it open.
3) To discharge high voltage capacitor, wait for 60 seconds.
4) Remove the control unit, referring to the procedure of “ CONTROL PANEL ASSEMBLY,
CONTROL UNIT AND KEY UNIT REMOVAL ”.
5) Follow the troubleshooting guide given below for repair.
STEPS
OCCURRENCE
CAUSE OR CORRECTION
1
Only pattern at “a” is broken.
*Insert jumper wire J1 and solder.
2
Pattern at “a” and “b” are broken.
*Insert the coil RCILF2003YAZZ between “c” and “d”.
6) Make a visual inspection of the varistor.
Check for burned damage and examine the
transformer with a tester for the presence of
layer short-circuit (check the primary coil
resistance which is approximately 780
.
±
10%). If any abnormal condition is detected,
replace the defective parts.
7) Reconnect all leads removed from
components during testing.
8) Re-install the control unit to the control panel
and re-install the control panel to the oven.
9) Reconnect the power supply cord.
10) Run the oven and check all functions.
2. Follow the troubleshooting guide given below, if indicator does not light up after above check and
repairs are finished.
1) Disconnect the power supply cord, and then remove outer case. Refer to procedure of “ HOOD
EXHAUST LOUVER REMOVAL ”, “ REMOVAL OF OVEN FROM WALL ” and “ OUTER CASE
REMOVAL ”.
2) Open the door and block it open.
3) To discharge high voltage capacitor, wait for 60 seconds.
4) Remove the hood intake duct R.
5) Disconnect the leads to the primary of the power transformer.
6) Ensure that these leads remain isolated from other components and oven chassis by using
insulation tape.
7) After that procedure, re-connect the power supply cord.
8) Follow the troubleshooting guide given below for repair.
STEPS
OCCURRENCE
CAUSE OR CORRECTION
The rated AC voltage is not present between
Check supply voltage and oven power cord.
1
the normal open terminal of the relay RY2 and
the normal open terminal of the relay RY1.
2
The rated AC voltage is present at primary
Low voltage transformer or secondary circuit defective.
side of low voltage transformer.
Check and repair.
P
FOIL PATTERN ON THE PRINTED WIRING BOARD TEST
QKITPB035
VRS1
a
c
d
b
S
13
P
J1
RY2
T1