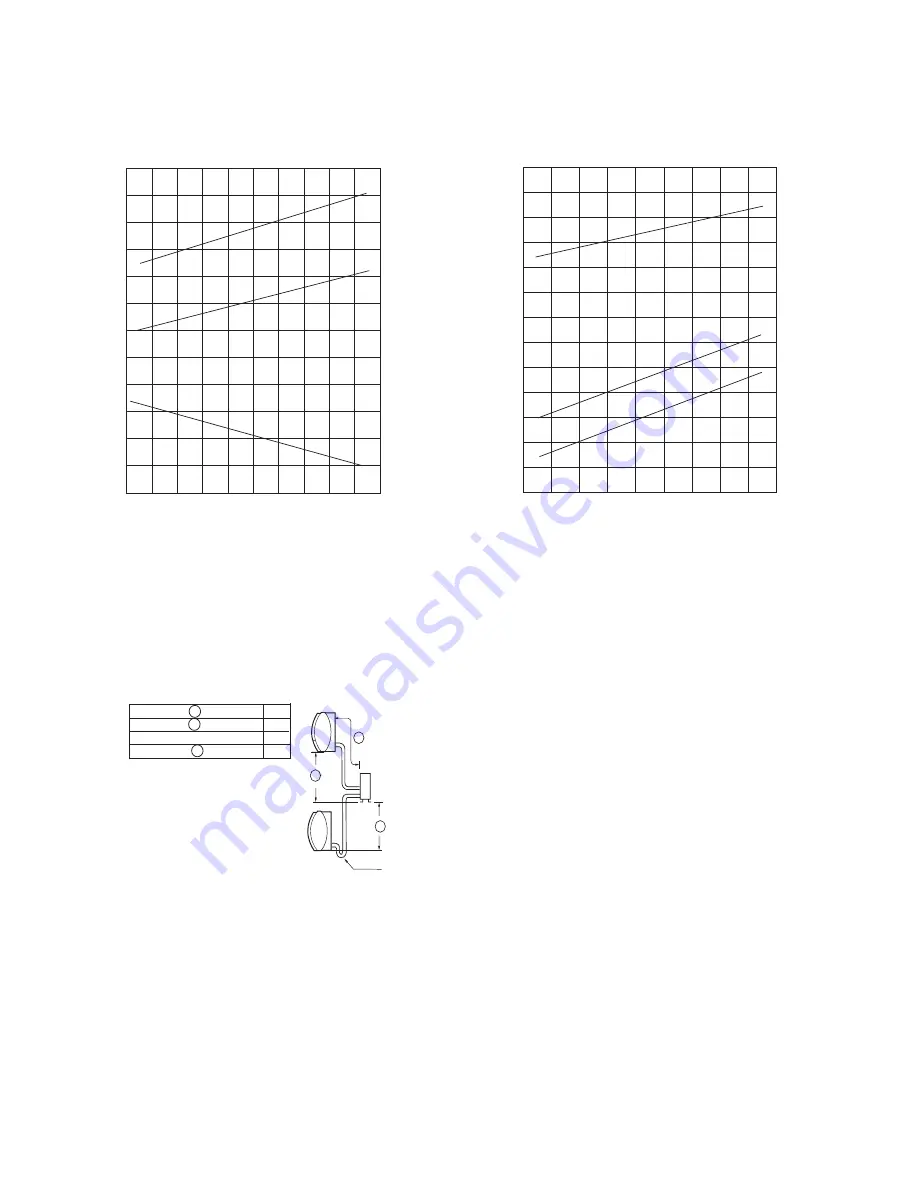
AEXM24HR
4 – 3
3. PERFORMANCE CURVES
[2] PERFORMANCE CURVES
1. Piping
2. Air-removing
Use an adapter for preventing vacuum pump oil from flowing back to
the gauge manifold hose. ON/OFF operation of the vacuum pump
should be made by the adapter switch.
(1) Remove both valve shaft caps of the stop valves.
(2) Remove the service port cap of the stop valve (gas side).
(3) Connect the gauge manifold hose to the service port and the
vacuum pump. Be sure that the hose end to be connected to the
service port has a valve core pusher.
(4) Open the gauge manifold valve and operate the vacuum pump for
10-15 minutes. Make sure the com pound gauge reads -0.1MPa
(-76cmHg).
(5) Close the gauge manifold valve.
(6) Turn off the vacuum pump.
(7) Fully open the stop valve (liquid side) with hexagon socket screw
key. Turn all the way up to contact.
(8) Fully open the stop valve (gas side) with hexagon socket screw
key. Turn all the way up to contact.
9) Disconnect the gauge manifold hose from the service port.
(10) Replace the service port cap and both valve shaft caps tightly.
Turn until thetorque suddenly increases.
Now tighten a 1/6-turn more.
NOTE: *Use a gauge manifold and hoses exclusive for R410A.
*After air removal,check the tubeconnections for gas..
leak using a leakage detector or soapy water.Regarding
leakage detector,use high-sensitivity type designed
specially for R410A.
F ig.
A t C ooling for A Y -X P M7F R (for A E -X M24HR )
F ig. A t Heating for A Y -X P M7F R (for A E -X M24HR )
44
42
40
38
36
34
32
30
28
26
24
6.0
6.5
7.0
7.5
13
14
15
16
17
2000
1800
2200
2400
2600
C
o
o
lin
g
c
a
p
a
c
it
y
(k
W
)
Outside air temp.
In
p
u
t(
W
)
Outlet
air
temp.
NOT E : T otal cooling capacity and total input with 4 units running.
(R unning frequency: HZ)
-4
-2
0
2
4
6
8
10
12
-6
5.0
6.0
7.0
8.0
36
34
32
30
28
1800
1600
2000
2200
2400
He
at
in
g
c
ap
ac
it
y
(k
W
)
Outside air temp.
In
p
u
t(
W
)
Outlet
air
temp.
(R unning frequency: HZ)
(
͠
)
(
͠
)
(
͠
)
(
͠
)
B
B
TRAP
OUTDOOR
UNIT
INDOOR UNIT
A
b. When the outdoor unit is placed at a higher
level than the indoor units, provide a trap
near the hose
̉
s lead-in port.
Max. piping length A
Max. total piping length of all unit
20m
50m
3m
Max.level difference B
10m
a. If total piping iength exceeds
40m, add20g of refrigerant per 1m.
Max. piping length A
Summary of Contents for AE-XM24HR
Page 5: ...AEXM24HR 1 4 5 WIRING DIAGRAMS 1 FOR MODEL AEXM24HR CC373 ...
Page 39: ...AEXM24HR 5 5 ...
Page 40: ...AEXM24HR 5 6 ...