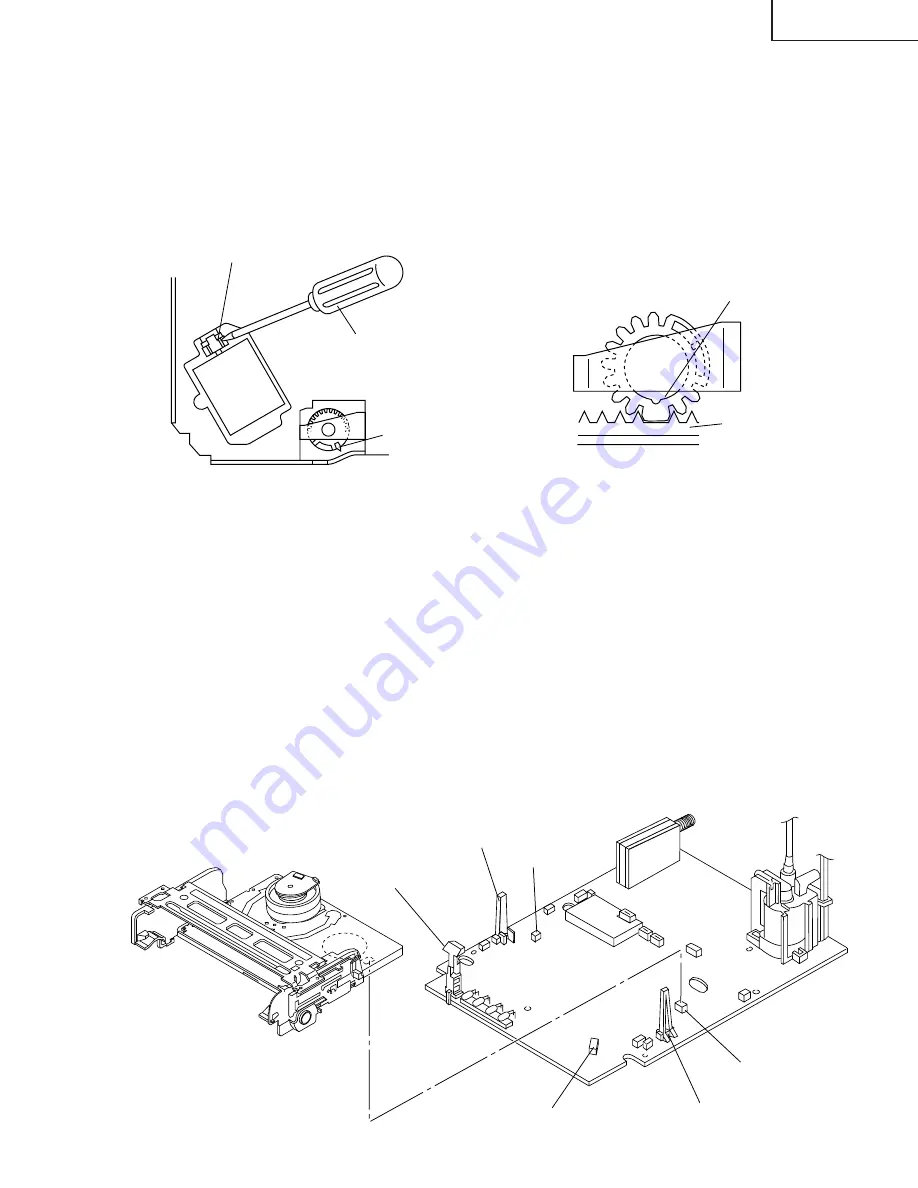
17
13VT-L200
PRECAUTIONS IN REASSEMBLING
MOUTING THE CASSETTE CONTROLLER
Initial setting is indispensable before placing the cassette controller in the mechanism. The initial setting is made in two
ways;electrical and mechanical.
Electrical setting:
Make a short-circuit between TP7701 and TP7702 and be sure that the mechanism is back to its initial setting position (*1).
Now place the cassette controller in position.(This method is used when the mechanism has been already set on its PWB.)
COUPLING THE MECHANISM TO THE PWB
Match the mechanism’s projections with the two symbols (round reference and oval sub-reference) on the main PWB. Place the
mechanism straight down in position with due care so that the mechanism chassis’s outer edges should not damage any parts
nearby.
Tighten up the two screws (one for fixing the mechanism and the head amplifier shield, the other on the main PWB’s soldering side
and located near the loading motor) to fix the mechanism and main PWB. Reconnect the FFC cables (MH and AA, ME and AD,
Drum Unit and AH) between the mechanism and main PWB.
Parts to pay attention to:
Start and end sensors
Q7703, Q7704
Record tip switch
S7701
Take special care of the connectors (board to board; AC, AE, AL) between the mechanism and main PWB.
Mechanical setting:
Turn the loading motor’s pulley feed gear using a
screwdriver and be sure that the mechanism is back
to its initial setting position (*1). Now place the
cassette controller in position.(This method is appli-
cable for the mechanism alone.)
Pulley feed gear
Screwdriver
Large tooth
Casecon
drive gear
Drive angle of
cassette control
END SENSOR
REC TIP SW
AL Connector
AE Connector
AC Connector
START SENSOR
Summary of Contents for 13VT-CL10
Page 7: ...7 13VT L200 Description Of Controls FRONT LOCATION OF USER S CONTROL REAR ...
Page 56: ...56 13VT L200 8 7 10 9 6 5 4 3 2 1 A B C D E F G H CHASSIS LAYOUT PWB B PWB D PWB C ...
Page 57: ...57 13VT L200 17 16 19 18 15 14 13 12 11 10 PWB A ...
Page 58: ...58 13VT L200 8 7 10 9 6 5 4 3 2 1 A B C D E F G H BLOCK DIAGRAM OF TV SECTION ...
Page 59: ...59 13VT L200 17 16 19 18 15 14 13 12 11 10 ...
Page 61: ...61 13VT L200 17 16 19 18 15 14 13 12 11 10 ...
Page 63: ...63 13VT L200 17 16 19 18 15 14 13 12 11 10 ...
Page 67: ...67 13VT L200 17 16 19 18 15 14 13 12 11 10 ...
Page 69: ...69 13VT L200 17 16 19 18 15 14 13 12 11 10 ...
Page 70: ...70 13VT L200 8 7 10 9 6 5 4 3 2 1 A B C D E F G H OVERALL SCHEMATIC DIAGRAM ...
Page 71: ...71 13VT L200 17 16 19 18 15 14 13 12 11 10 ...
Page 74: ...74 13VT L200 8 7 10 9 6 5 4 3 2 1 A B C D E F G H SCHEMATIC DIAGRAM MAIN 1 Unit TV Section ...
Page 75: ...75 13VT L200 17 16 19 18 15 14 13 12 11 10 ...
Page 76: ...76 13VT L200 8 7 10 9 6 5 4 3 2 1 A B C D E F G H SCHEMATIC DIAGRAM MAIN 2 Unit TV Section ...
Page 77: ...77 13VT L200 17 16 19 18 15 14 13 12 11 10 ...
Page 78: ...78 13VT L200 8 7 10 9 6 5 4 3 2 1 A B C D E F G H SCHEMATIC DIAGRAM POWER Unit TV Section ...
Page 79: ...79 13VT L200 17 16 19 18 15 14 13 12 11 10 ...
Page 80: ...80 13VT L200 8 7 10 9 6 5 4 3 2 1 A B C D E F G H SCHEMATIC DIAGRAM MAIN Unit VCR 1 Section ...
Page 81: ...81 13VT L200 17 16 19 18 15 14 13 12 11 10 ...
Page 82: ...82 13VT L200 8 7 10 9 6 5 4 3 2 1 A B C D E F G H SCHEMATIC DIAGRAM MAIN Unit VCR 2 Section ...