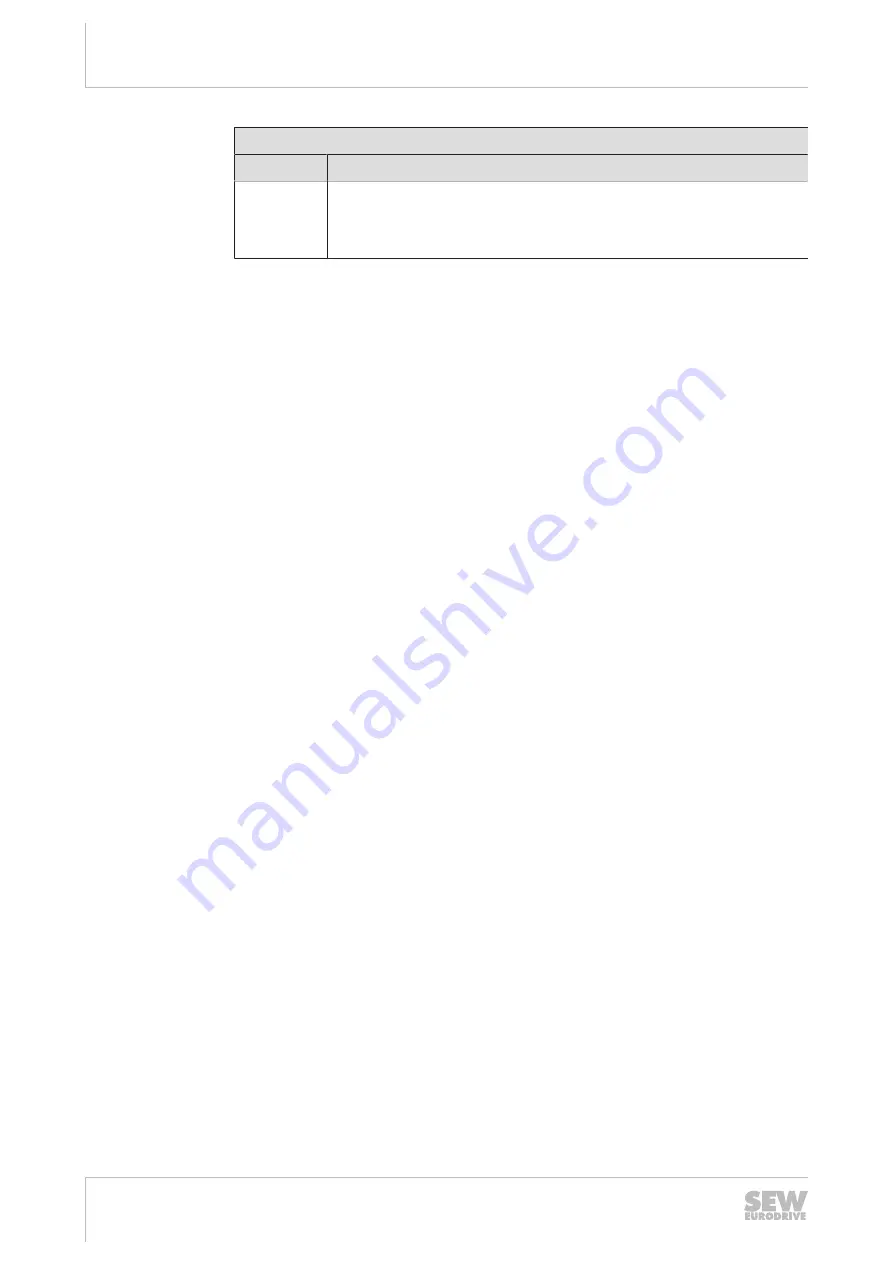
6
Electrical installation
Connection of MOVI-SWITCH drive
Operating Instructions – Explosion-Protected MOVI-SWITCH
®
Drives
32
Description of the control signals
Terminal
Function
OK
Ready signal, DC 24 V
0: Overtemperature or no DC 24 V supply
1: DC 24 V supply is connected and no overtemperature is present
25988670/EN – 04/2020