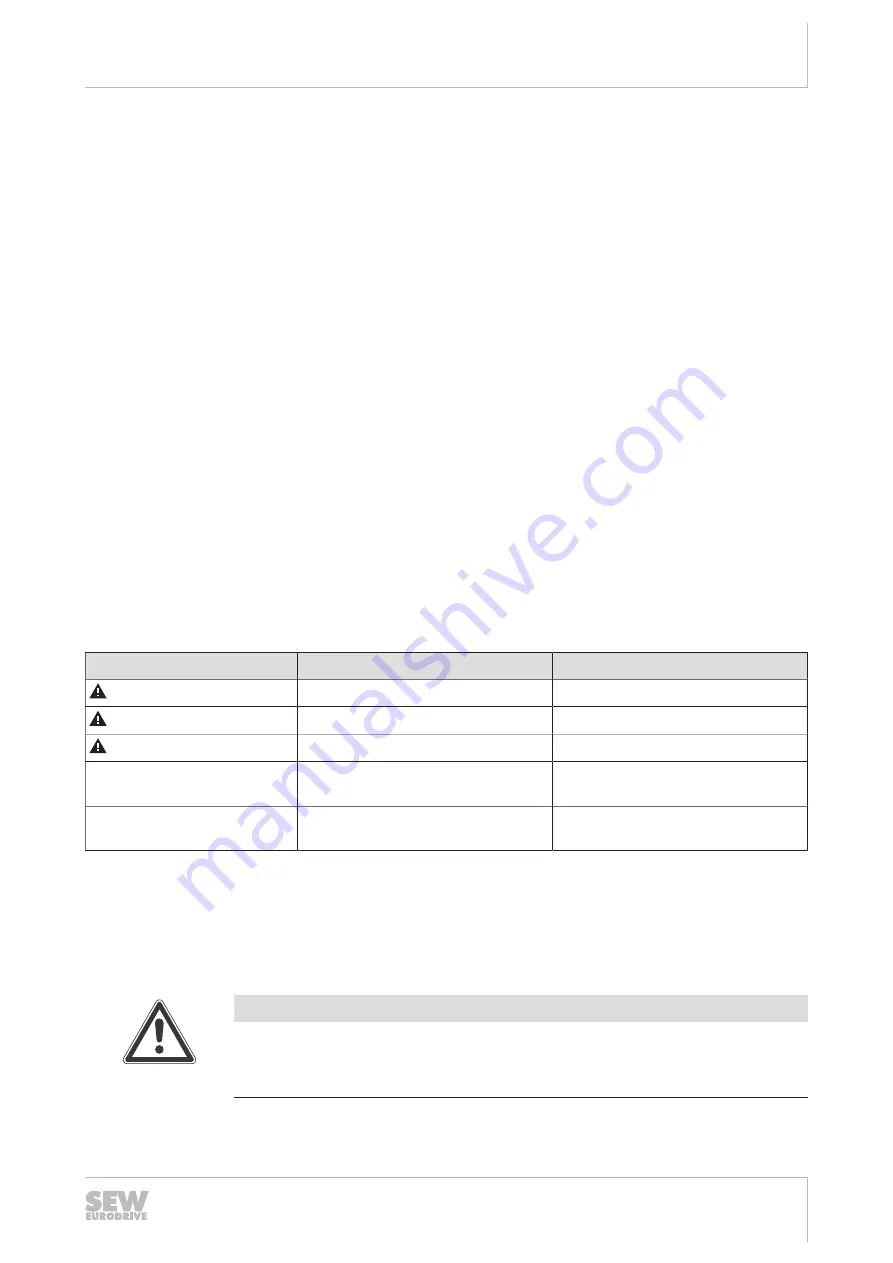
1
General information
About this documentation
Operating instructions – ECDriveS
®
5
1
General information
1.1
About this documentation
The current version of the documentation is the original.
This documentation is an integral part of the product. The documentation is intended
for all employees who perform work on the product.
Make sure this documentation is accessible and legible. Ensure that persons respons-
ible for the systems and their operation as well as persons who work on the product
independently have read through the documentation carefully and understood it. If you
are unclear about any of the information in this documentation, or if you require further
information, contact SEW‑EURODRIVE.
1.2
Information on this documentation
This documentation describes the ECDriveS
®
roller drive system.
This document shows how to install and connect the ECR roller drive/ECG roller gear-
motor and how to start up the roller drive system with the ECC-DBC binary control.
1.3
Structure of the safety notes
1.3.1
Meaning of signal words
The following table shows the grading and meaning of the signal words for safety
notes.
Signal word
Meaning
Consequences if disregarded
DANGER
Imminent hazard
Severe or fatal injuries
WARNING
Possible dangerous situation
Severe or fatal injuries
CAUTION
Possible dangerous situation
Minor injuries
NOTICE
Possible damage to property
Damage to the product or its envi-
ronment
INFORMATION
Useful information or tip: Simplifies
handling of the product.
1.3.2
Structure of section-related safety notes
Section-related safety notes do not apply to a specific action but to several actions
pertaining to one subject. The hazard symbols used either indicate a general hazard
or a specific hazard.
This is the formal structure of a safety note for a specific section:
SIGNAL WORD
Type and source of hazard.
Possible consequence(s) if disregarded.
•
Measure(s) to prevent the hazard.
28507088/EN – 11/2018