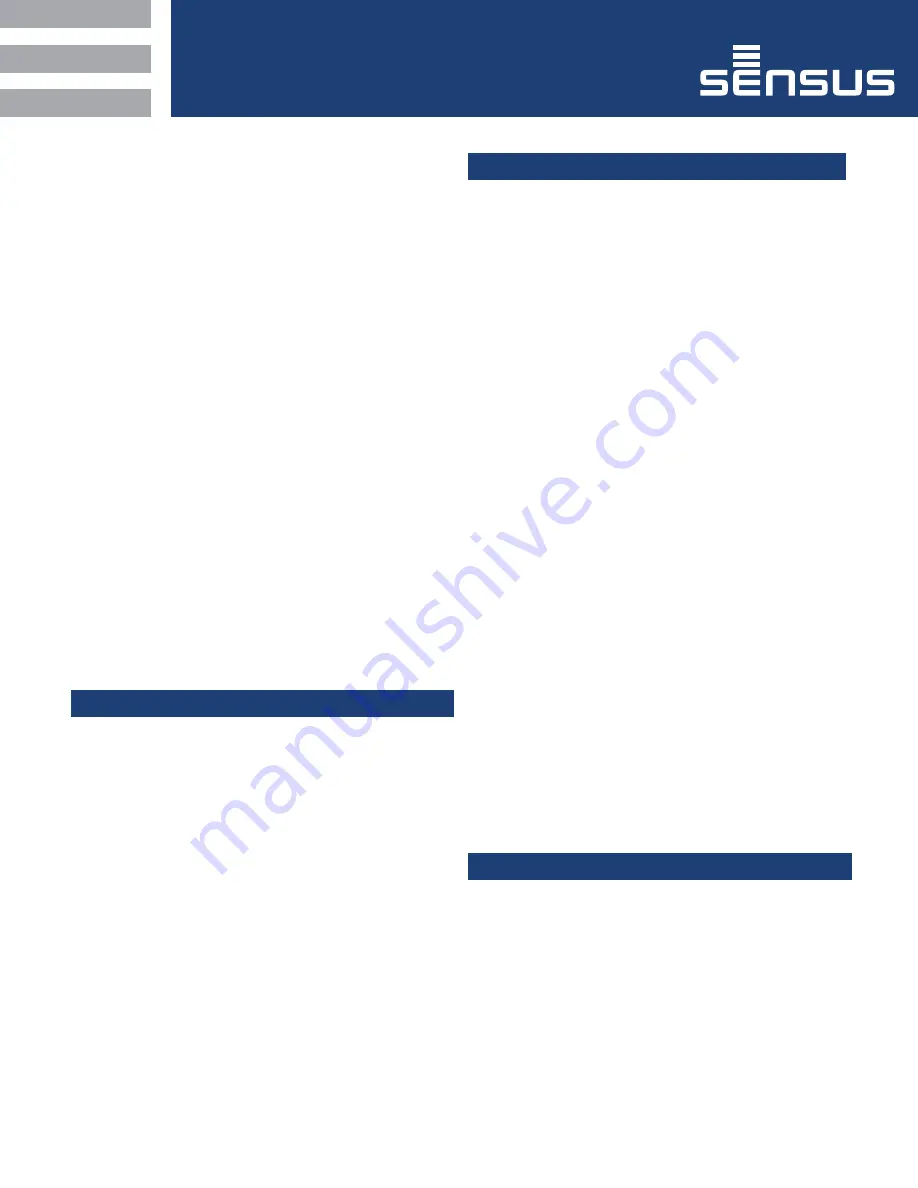
3
4
For outdoor installation, it is recommended that the regulator
be installed so that the regulator vent faces downward to
avoid the potential of water or other foreign matter entering
the vent and interfering with the proper operation of the
regulator.
5
Install the control line. It should be sturdy with adequate
protection against breakage (regulators go wide open if control
line is broken). Pitch it to drain away from the regulator, free of
moisture pockets. The control line should be no less than 1/4"
steel tubing or pipe for the 461-12S and 461-8S models and
1/2" steel pipe for the 461-S models.
The regulator will work to deliver the pressure(for which
it is adjusted) at that point in the piping where the control
connection is located.
In general, the control connection should be at least eight
pipe diameters downstream from the regulator and should be
in as straight a run as possible where turbulence is a minimum.
Keep clear of elbows, valves, and other causes of excessive
turbulence.
The control connection should be clean and smooth
inside the pipe to minimize turbulence. It should be located
on the top or side of the pipe, not on the bottom.Where outlet
piping increases in size near the regulator, it is generally
preferable to locate the connection in the larger size.
The unions for the control lines of the 461-S models contain a
small orifice (approximately 1/16" diameter). This orifice should
not be removed. Also, make certain it is open and free of foreign
material.
6
Check all connections for leaks.
CAUTION
Turn gas on very slowly. If an outlet stop valve is used,
it should be opened first. Do not overload the diaphragm
with a sudden surge of inlet pressure. Monitor the outlet
pressure during start-up to prevent an outlet pressure overload.
7
Put the regulator into operation as follows:
a.
Slowly open downstream control line valve
(A)
.
b.
Slowly open downstream block valve
(B)
.
c.
Very slowly open upstream block valve
(C)
.
d.
When start-up and adjustment are completed,
make sure valves
(A)
,
(B)
, and
(C)
are fully opened.
See diagram page 2
8
Set adjusting screw for the required outlet pressure. Turn it clock
wise to increase the pressure and counterclockwise to
decrease it. Only make the adjustment when gas is actually
flowing through the regulator.
Remove the seal cap and, if applicable, loosen locknut
to make adjustment.
After adjustment is complete, locknut (if applicable) should be
tightened firmly and seal cap replaced. The absence of this seal
cap can result in unstable operation.
9
To shut down, carefully close valves (C), (B), and (A)
in that order.
CAUTION
1 Keep pipe dope and all other foreign substances
out of the control line.
2 Never install any type of automatic shut-off device,
which closes completely, between the regulator outlet
and the downstream control line connection.
3 The vent must be positioned to protect against flooding,
drain water, ice formation, traffic, tampering etc. The vent
must be protected against nest-building animals, bees,
insects, etc. to protect from vent blockage and minimize
the chances of foreign material collecting in the vent side
of the regulator diaphragm.
Servicing and Adjustment
General Notes
1
Make sure the regulator is entirely depressured before
servicing.
2
A quick visual inspection of the valve can be made by removing
inspection plates (33) from the sides of the body. These also
provide greatly improved access to the valve when servicing or
adjusting. Valve and body parts are interchangeable with other
model 461 regulators.
3
Carefully note location and position of disassembled parts to
be certain reassembly is correct. Inspect each one carefully
and replace those that are worn or damaged or otherwise
unsatisfactory.
4
Use lubricants sparingly and with care to avoid exposing
tacky surfaces to the gas stream. Such surfaces could cause
dirt accumulation on close-clearance parts.
Use moly or silicone type lubricants.
Avoid the use of petroleum base types.
It is best to avoid lubricating the stem or the guide.
However, a small amount of silicone spray release agent
to lubricate stem O-ring will help assure free movement and
a tight seal. An application of silicone base lubricant to the
other O-rings and the tetraseals in the regulator will also help
assure their tightness.
CAUTION
Regulators are pressure control devices with numerous
moving parts subject to wear that is dependent upon
particular operating conditions. To assure continuous
satisfactory operation, a periodic inspection schedule
must be adhered to with the frequency of inspection
determined by the severity of service and applicable laws
and regulations.
Installation and Maintenance Instructions
Model 461-S, 461-8S, and 461-12S Regulator