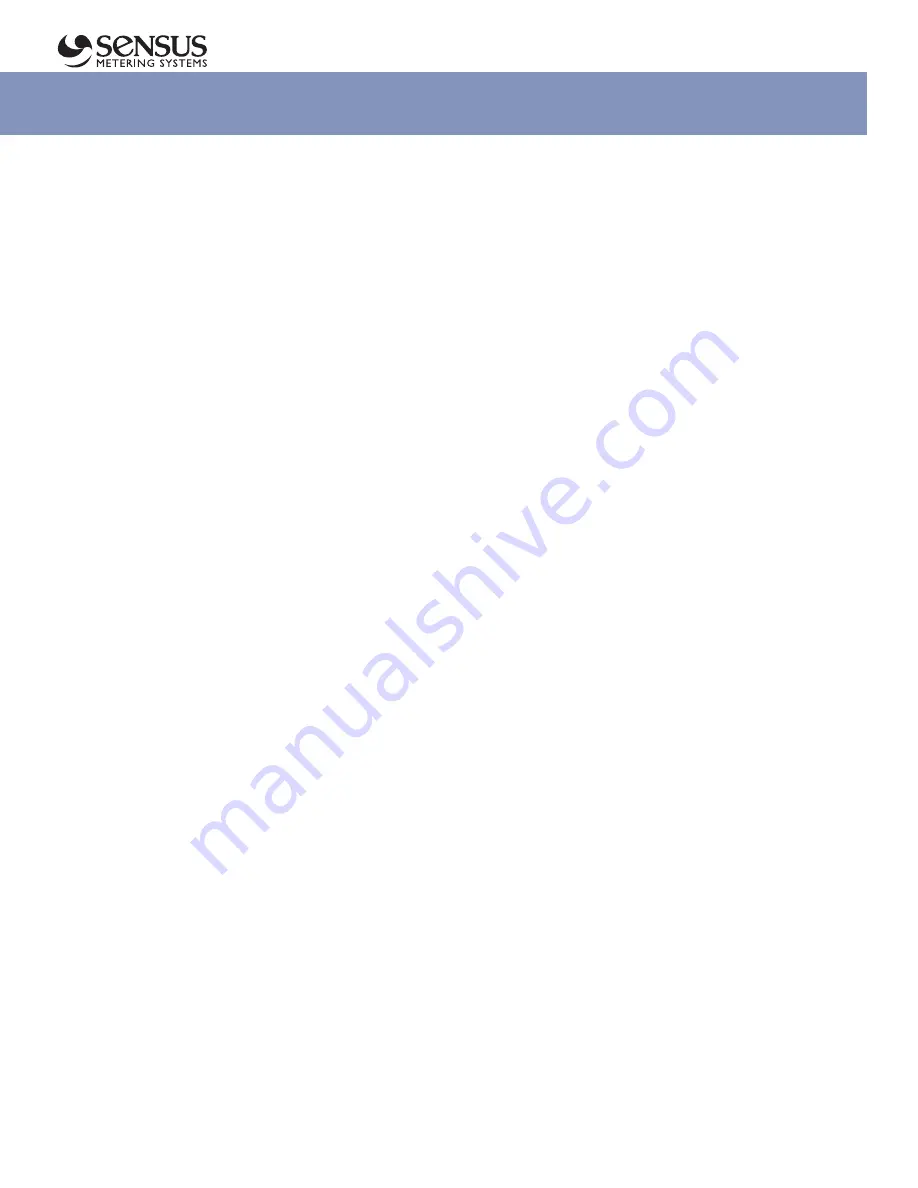
14
Servicing – 1-1/2", 2", 2-1/2"
General Instructions
1.
Make sure the regulator is entirely depressured before servicing.
2.
Carefully note location and position of all disassembled parts
to be certain reassembly is correct. Inspect each one carefully
and replace those that are worn or damaged or otherwise
unsatisfactory.
3.
A moderate application of lubricant to O-Ring
13
will help assure
free stem movement and a tight seal. Similar application of
lubricant to other O-Rings or Tetraseals will help assure their
tightness. Do not use petroleum base lubricants.
4.
Bolted connections should be tightened evenly and firmly.
Carefully tighten diaphragms into place. Bolts must be tight
enough to prevent leakage, but not so tight that the diaphragm
material is crushed or damaged.
5.
Upon completion of servicing, make certain that regulator
installation is entirely free of leaks.
To Service Valve – 15
1.
Remove bolts
38
and remove bottom cap
37
and Tetraseal
32
.
2.
Remove Retaining Ring
16a
.
3.
Remove both halves of valve holder
16b
.
4.
Remove valve
15
(wave washer
14
will likely remove with the
valve. Retain for reassembly. – To reassemble, replace parts
in reverse sequence.
To Install V-Port Wing – 12f
1.
Remove valve
15
per assembly “To Service Valve -
15
”.
2.
Remove wave washer
14
.
3.
Remove retainer
12e
. It will not be used.
4.
Reinstall wave washer
14
.
5.
Install V-Port wing
12f
on stem with v-notch side against the
wave washer and flat area exposed.
6.
Reassemble remaining parts in reverse sequence.
To Service Main Diaphragm – 11d
1.
Remove top cap
1
, and release and remove adjustment
3
.
On high pressure model remove cap
1a
, release adjustment
3a
,
and remove cover
5
and button
7a
. Mark or measure position
of adjustment
3
or
3a
. Use this to return adjustment to this
setting during reassembly.
2.
Remove spring
9
.
3.
Remove bolts
22
and upper case
21
.
4.
Rotate diaphragm assembly
11
counterclockwise (this unscrews
11h
from
12d
) and remove.
5.
To disassemble diaphragm assembly, remove nut
11a
.
Carefully note location and position of all parts to be certain
of correct reassembly. Abrasive side of emery cloth washers face
against diaphragm.
– To reassemble, replace parts in reverse sequence.
Make sure the screwed connection between 11h and 12d is
loose by approximately 1/2 turn.
To do this, carefully rotate
diaphragm assembly
11
clockwise until this screwed connection
bottoms (do not jam it together). Then back-off diaphragm
assembly
11
counterclockwise approximately 1/2 turn.
The
11h
to
12d
screwed connection must not be tight.
To Service Orifice – 19
1.
Remove valve
15
per section “To Service Valve-
15
”.
2.
Remove main diaphragm assembly
11
per steps 1 through 4
“To Service Main Diaphragm-
11d
”.
3.
Remove seal diaphragm assembly
12
per steps 3 and 4 under
“To Service Seal Diaphragm-
12b
”.
4.
Remove Retaining Ring
19a
.
5.
Remove orifice
19
through top opening.
To reassemble, replace parts in reverse sequence.
(On reassembly, ensure that
19a
is fully seated in its groove.
Also, beveled edge of
19a
faces downward toward bottom
cap
37
.)
To Service Seal Diaphragm – 12b
1.
Remove valve
15
per assembly “To Service Valve-
15
”.
2.
Remove main diaphragm assembly
11
per steps 1 through 4
“To Service Main Diaphragm-
11d
”.
3.
Remove bolts
25
and lower diaphragm case
24
.
4.
Remove bolts
29
and centerpiece
27
, and then remove seal
diaphragm assembly
12
.
5.
To disassemble
12
, unscrew piston
12a
from stem
12d
.
Use a spanner wrench in notch in skirt of piston
(this can also be done by inserting a standard 7/32"
Allen wrench in the notch).
To reassemble, replace parts in reverse sequence.
Make certain that fabric side of seal diaphragm
12b
faces
upward and “rubber” side faces downward toward body.
Do not pinch loop in seal diaphragm
12b
between ring
33
and centerpiece
27
. Also, rounded edge of
33
faces upward
toward seal diaphragm
12b
.
Periodic Inspection:
Regulators are pressure control devices with numerous moving
parts subject to wear that is dependent upon particular operation
conditions. To assure continuous satisfactory operation,
a periodic inspection schedule must be adhered to with the
frequency of inspections, determined by the severity of service
and applicable laws and regulations.
Installation and Maintenance
Model 121 Regulators