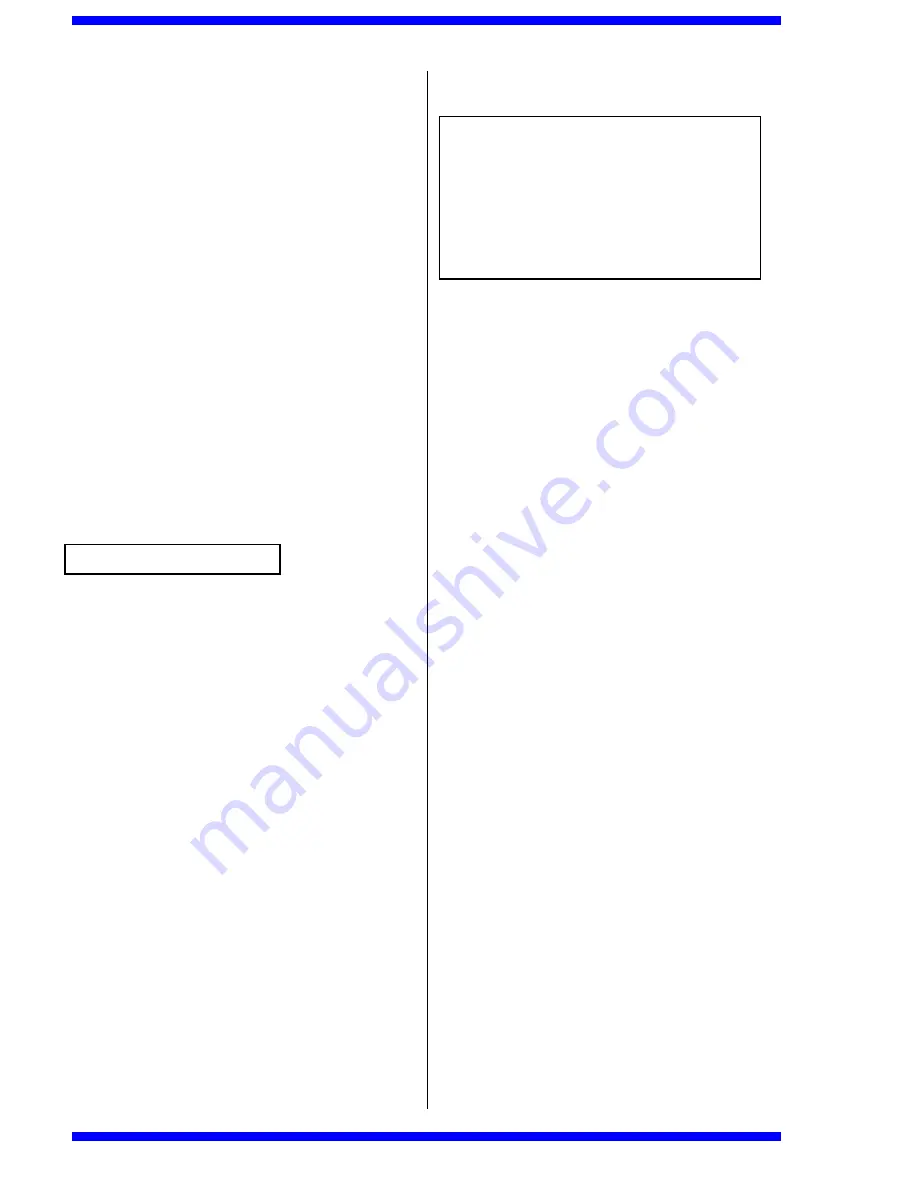
Selwood Seltorque S150 Manual
12
8. Smear soft soap on outside diameter of shaft
sleeve (C06) and inside diameter of rubber drive
band. Protect the highly polished face of the seal
with several layers of clean soft paper, and slide
seal assembly onto sleeve using finger pressure
only - USE NO TOOLS. The seal must be
positioned so that the carbon face is about 3mm
past the non-flanged end of the sleeve.
9. Within a few minutes, to ensure that the lubricant
has not set, slide sleeve seal assembly onto shaft
(seal face towards stationary seat) and press into
working position using only the sleeve's flange.
This procedure automatically causes the seal
head to slide along the sleeve into its correct
working position. Ensure that ‘O’ ring (C07) is
correctly trapped in sleeve recess (C06) and that
sleeve abuts against shoulder on shaft.
10. Push mechanical seal spring onto location
diameter provided on seal head. Ensure that the
spring's coils are correctly supported by the flange
of sleeve (C06) and will not become trapped
between the flange and the impeller (C04) Refit
key (C05) and impeller in accordance with Section
5.3.1 Impeller (C04) Instructions 7 and 9,
inclusively.
11. Replace remaining components in accordance
with Section 5.3.1 Impeller (C04) Instructions 10
and 13, inclusively.
Failure of the pump set to pump under suction lift
conditions could be due to a fault in the delivery valve
assembly.
To inspect and service, proceed as follows:
1. Ensure that pump has been shutdown and the
delivery line has been drained.
2. Release T-bolt (C19), swing locking bar (C22)
clear, and remove inspection panel (C24) and
gasket (C25). It now becomes possible to lift the
valve by hand to expose the valve seat (C16) so
allowing foreign matter to be removed. Also
undertake a preliminary check of the condition of
the valve rubber.
3. If further disassembly is required, remove screws
(C29) and washers (A13), allowing clamping bar
(C28) and delivery valve (C27) complete with
valve plates (C26) and (C30) to be removed.
4. Separate upper and lower valve plates (C26) and
(C30) by removing nut (C31), and examine
condition of rubber (C27), especially along the
hinge line and seating surface. Discard if
damaged or misshapen.
5. To replace valve seat (C16), remove valve
chamber (C18) after releasing nuts (B31) and
spring washers (C15).
6. Reassemble components in reverse order,
renewing gaskets (C17) and (C25) if necessary.
Ensure that radiused edge of clamping bar (C28)
is adjacent to hinge line of valve rubber (C27) and
that each screw is tightened a small amount so as
to produce an even clamping pressure. Correctly
tightened screws will not cause the clamp bar to
distort the rubber. Seal screws with Loctite 572.
Chamber, Air Pump
Mechanism, Drive Coupling,
Drive Shaft Bearings and Lip
Seal
Leakage of oil through the vent at the bottom of
flushing chamber (D33) could be due to failure of either
of the lip seals (D04). If the pumped liquid also leaks
through the vent, the mechanical seal (C08) will
require to be replaced in addition to its adjacent lip seal
(D04). In any of these events, proceed as follows:
1. Drain oil from flushing chamber and bearing
housing by removing filler caps (D08) and drain
plugs (D13) and (D34).
2. Remove separator assembly and suction tube
(B27) or (B35) in accordance with Section 5.3.1
Impeller (C04) Instructions 1 and 4, inclusively.
3. Remove impeller screws (C01) and washers (C02)
and
(C03),
and
withdraw
impeller
(C04)
mechanical seal spring, and shaft sleeve (C06)
complete with mechanical seal parts (C08).
Handle the sleeve and mechanical seal with great
care and store in safe place, particularly if these
parts are to be reused.
4. Remove split guard fitted around flexible coupling,
and release all of the coupling's fasteners allowing
the rubber tyre to be removed.
5. Attach lifting equipment to bearing housing and
pump body in compliance with requirements of
Health and Safety at Work Act, 1975.
6. Remove nuts, bolts and washers securing pump
to chassis and hoist clear, carefully noting the
positions of any shims between pump feet and
chassis.
7. Lower unit onto working surface and, in
compliance with Health and Safety at Work Act,
1975, tip pump onto ends of studs (C10) ensuring
that they are suitably protected from damage.
8. Remove nuts (A11) and spring washers (A12) and
carefully separate bearing housing and flushing
chamber assembly from pump body (C09).
During this operation, be very careful not to
damage the mechanical seal stationary seat by
allowing it to contact the shaft.
9. It now becomes possible to remove flushing
chamber (D33) from bearing housing (D06), after
releasing screws (D31) and spring washers (A06).
10. To replace lip seals (D04):
a) Press failed components out of housings and
discard.
Summary of Contents for SELTORQUE S150
Page 25: ...Selwood Seltorque S150 Manual 25 THIS PAGE INTENTIONALLY BLANK ...
Page 28: ...Selwood Seltorque S150 Manual 28 ...
Page 30: ...Selwood Seltorque S150 Manual 30 ...
Page 32: ...Selwood Seltorque S150 Manual 32 ...
Page 34: ...Selwood Seltorque S150 Manual 34 ...
Page 36: ...Selwood Seltorque S150 Manual 36 ...
Page 38: ...Selwood Seltorque S150 Manual 38 ...
Page 40: ...Selwood Seltorque S150 Manual 40 ...
Page 42: ...Selwood Seltorque S150 Manual 42 ...
Page 44: ...Selwood Seltorque S150 Manual 44 ...
Page 46: ...Selwood Seltorque S150 Manual 46 ...
Page 48: ...Selwood Seltorque S150 Manual 48 ...
Page 50: ...Selwood Seltorque S150 Manual 50 ...
Page 52: ...Selwood Seltorque S150 Manual 52 ...
Page 54: ...Selwood Seltorque S150 Manual 54 ...
Page 56: ...Selwood Seltorque S150 Manual 56 ...
Page 58: ...Selwood Seltorque S150 Manual 58 9 WIRING DIAGRAMS 9 1 Isuzu 4JG1 Engine Canopy ...
Page 60: ...Selwood Seltorque S150 Manual 60 9 3 Deutz Wiring Diagram ...
Page 62: ...Selwood Seltorque S150 Manual 62 THIS PAGE INTENTIONALLY BLANK ...